Most people don’t think twice about it. They place an order and a package arrives on their doorstep in a day or two, sometimes less; or they head to their local box store and pick up just what they need.
This scenario is becoming so ordinary for consumers that it’s easy to forget the hands that scan, stock, pick, and sort our goods in warehouses across the world. In this new era of immediate product gratification, are warehouse workers able to do their jobs safely?
About This Guide
Warehouses across the country are facing new and unusual safety challenges — but warehouse safety programs are not keeping up the pace, as indicated by elevated injury and fatality statistics.
To make matters worse, companies struggling to keep up with e-commerce giants often make sweeping changes and expect safety processes to catch up. But if a company doesn’t have a safe warehouse, they are in danger of losing good-quality workers, facing large lawsuits and fines, and losing their customer base.
In this guide, we’ll look at practical ways to prioritize and improve your warehouse safety program.
Want to download this article and read it later? Get the PDF straight to your device.
Today’s Warehouse Safety Challenges
The reasons for the drop in safety at warehouses are many, but a low unemployment rate and lack of properly-trained workers are two examples. Other challenges include workflow and workload changes, worker engagement, and injuries and fatalities, whether from unsafe working conditions, human error or other reasons.
Warehouse Injuries and Fatalities
Annual warehouse injury and fatality rates are rising, which is a disturbing trend. According to the U.S. Bureau of Labor Statistics, over 683,000 employees work in some type of warehouse setting. These roles include everything from truck and tractor operators to material movers to order fillers. In 2015, 11 workers were killed; in 2016, 16 warehouse workers died from injuries sustained on the job.
In 2019, the transportation and warehousing worker injury rate was 4.4 per 100 full-time workers. The sector has the second-highest rate of recordable cases in private industry after agriculture, forestry, fishing and hunting. There were also 914 fatal occupational industries in transportation and warehousing in 2019, and trucking accounted for 617. In 2015, there 765 fatalities in the sector, which presents a worrying trend.
Talent Shortage
While injuries and fatalities can still occur with properly trained and highly qualified workers, they tend to happen in lower numbers. Like many other service and trade industries, warehouse jobs are plentiful but the workforce to fill those spots is slim. The shortage of experienced workers across supply chains leads to higher rates of accidents, injuries, and fatalities.
The talent shortage is the product of several factors. First, Baby Boomers are retiring at high rates, and companies don’t have the managers needed to replace them. Additionally fewer high school graduates and college-educated workers choose warehousing and transportation as a long-term career, which means there are entry-level applicants but a shortage of middle management.
Cost-cutting measures also play a role. The physical demands of warehousing, coupled with relatively low wages and job security at some companies results in higher turnover throughout the year. And due to seasonal changes in workload, warehousing employs more temporary, contract, and aging workers than industries like manufacturing. Plus, companies reduce headcount and cut training programs during times of downturn, which further shrinks their talent pools.
The e-Commerce Boom
The talent shortage is a crucial problem that grows year on year. The growth of e-commerce saw a request for an additional 452,000 warehouse workers in 2018-19. And it’s likely the COVID-19 pandemic and the shift in online shopping trends will mean even bigger numbers for 2021-22.
As e-commerce continues to explode, business slowdowns and lay-offs at brick and mortar retailers impact worker safety. As more and more people turn to the Internet for their shopping needs, brick and mortar stores struggle to keep up. These businesses often have to lay off workers in all shifts, which can be an especially dangerous proposition when it comes to backroom, stock, and warehouse workers.
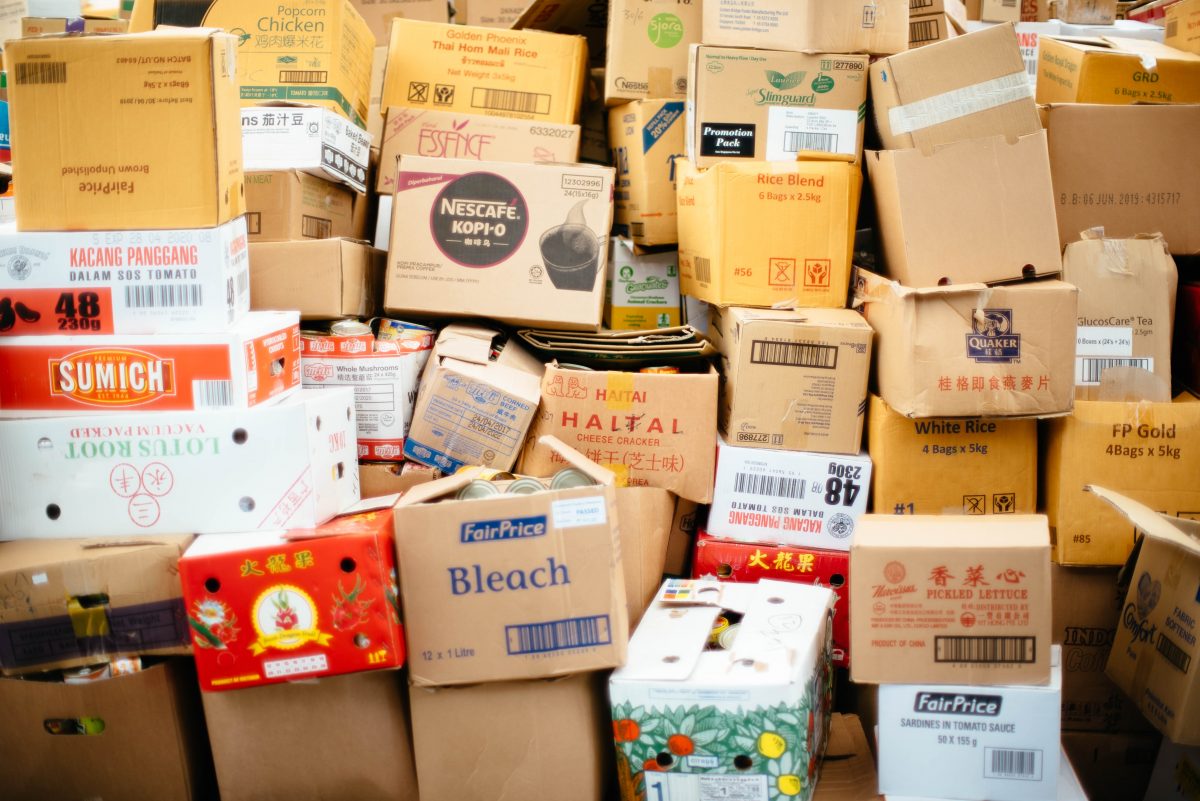
Without enough stock and warehouse workers, backrooms and warehouses fill up with boxes of merchandise, creating hazardous working conditions ripe for injuries.
In a 2019 article, Business Insider explored the numerous overnight stock and backroom shift cuts at Target stores across the United States. Target employees expressed concerns that these cuts have led to more injuries for workers on the job.
In Idaho, OSHA cited four Dollar Tree Stores for storage and walkway violations leading to over $800,000 in fines. Brick and mortar stores aren’t the only ones facing possible fines and allegedly exposing employees to dangerous conditions.
According to a 2018 article on Patch.com, Amazon warehouses are fraught with unsafe conditions, including grueling schedules, unrealistic goals, and dangerous procedures.
Constant Workflow and Workload Changes
Even under safe conditions, working in a warehouse can still be hard work. Workers are constantly on their feet, walking, bending, lifting and working; making it a physically demanding job. The workload needs in a warehouse are also dynamic, changing from day-to-day and even from hour-to-hour.
Environmental factors such as high or low temperatures, noise levels, and poor lighting also affect workers’ health and safety in warehouses. These ever-changing conditions, if not properly managed, can have a negative impact on safety.
2020 OSHA Warehouse Citations
In the last few years, OSHA has seen an uptick in violations, especially those violations that incur six-figure fines. In 2020, general warehousing and storage facilities received 300 federal OSHA citations for:
- Powered industrial trucks – $296,349 in fines
- Handling materials – general – $120,300 in fines
- Maintenance, safeguards, and operational features for exit routes – $32,149 in fines
- General – $44,170 in fines
- Hazard communication – $26,319 in fines
- The control of hazardous energy (LOTO) – $91,658 in fines
- Wiring methods, components, and equipment for general use – $22,254 in fines
- OSHA Act General Duty – $104,848 in fines
- Respiratory protection – $23,707 in fines
View the complete list of 2019-2020 citations for NAICS CODE 493110 General Warehousing and Storage.
Companies that received citations failed to maintain OSHA compliance in one or more of the above areas. The resulting unsafe conditions led to harm or unnecessary risk to employees.
Warehouse Safety Standards
Setting common warehouse safety standards that can be applied across the board is one way to improve working conditions. Currently, a patchwork of General Industry Standards governs safety in the warehouse environment, but not all hazards, such as Heat Illness and Ergonomic hazards are contained in a current standard that is enforceable in the Warehouse industry.
OSHA’s Role in Warehouse Safety
To help facilitate worker safety in warehouses, the Occupational Safety and Health Administration offers a brochure on safety, Worker Safety Series: Warehousing. This publication covers the most common hazards in a warehouse setting. It covers specific areas of the warehouse, from the docks to the conveyors, providing tips on reducing hazards in those areas. The brochure also contains Think Safety Checklists covering:
- General Safety: dock areas, floors and other areas, ventilation systems, and employee procedures
- Materials Handling: any loose and unboxed materials, storage areas, proper lifting techniques
- Hazard Communication: hazardous materials trainings, procedures and documentation
- Forklift: training and maintenance
Other helpful resources on safety from OSHA include:
OSHA Warehouse Standards
OSHA recognizes 10 warehouse standards when assessing properties and companies for safety. These safety standards include:
- Forklifts
- Hazard communication
- Electrical, wiring methods
- Electrical, system design
- Guarding floor & wall openings and holes
- Exits
- Mechanical power transmission
- Respiratory protection
- Lockout/tagout/LOTO
- Portable fire extinguishers

PPE Required in a Warehouse
OSHA requires employers to provide all employees in a warehouse with the appropriate PPE (Personal Protective Equipment). Employers looking for a comprehensive guide to PPE can utilize OSHA’s Personal Protective Equipment brochure. OSHA requires employers to perform continuous hazard assessments to determine what types of PPE is needed. Each employer is also responsible for:
- Providing needed PPE for employees
- Training employees on proper use and care of PPE
- Maintaining PPE and replacing as needed
The onus for proper PPE use doesn’t just fall on the employer. Employees must properly wear PPE, attend training sessions, care for, clean and properly store PPE and inform supervisors when PPE needs to be replaced or repaired. Common types of PPE used in a warehouse include:
- Hard hats
- High-visibility jackets
- Safety glasses or goggles
- Safety boots with steel toe caps
- Overalls
- Safety gloves
Mandatory Safety Signage
Each warehouse is also required to post mandatory safety signage. All of OSHA’s signage guidelines are found in 29 CFR 1910.145. The signage guidelines tell employers what types of signage is needed, where it should be placed and exactly what it should look like.
Safety signs in warehouses fall into several different categories: notice, general safety, admittance, fire safety, and non-hazard. Within these categories, signs should have one of three levels of classification.
Danger signs alert to the most serious of hazards. Warning signs show areas that could be hazardous but do not need as much caution as danger areas. Finally, caution signs highlight areas that could cause minor injuries or damage but should still be taken seriously.
Here are some helpful resources to help determine what signage is needed for your warehouses:
- Graphic Products: Five Ways to Meet OSHA Requirements for Safety Signage
- ID Label: A Guide to Warehouse Signs
Required Training for Warehouse Workers
Other OSHA requirements include mandatory training for employees. Training requirements for general industry, maritime, construction, agriculture and federal employee programs are laid out in OSHA’s Training Requirements in OSHA Standards booklet. Companies should consult the booklet to see which requirements apply to their warehouses and overall business. For additional training, employers can utilize OTI Education Centers. These nonprofit organizations are authorized by OSHA to provide occupational safety and health training to workers, supervisors and employers. OSHA also offers educational materials to supplement training, including:
- Brochures and booklets
- Fact sheets
- Online safety and health topics pages
- Posters
- Online newsletters
Warehouse Safety Management
Warehouse safety starts with a solid management plan that includes training, regular meetings with employees and strategies for safety.
How to Train Employees in Warehouse Safety
As mentioned before, well-trained and qualified workers are safer workers. While an employer cannot control the type of training an employee brings to the job, they can be sure that any continuing training is applicable, useful and comprehensive. It’s particularly important with today’s multi-ethnic workforce to provide training in the primary languages spoken by the workers.
When evaluating and considering which training programs to offer employees, look for programs that apply to all workers, as well as those that will help more specific warehouse roles. Everyone should learn proper procedures for hazardous material spills, while only certain workers who operate the forklift would need detailed forklift operation training.
OSHA’s Hazard Identification Training Tool helps companies identify hazards in their own warehouses. Using this information, employers can then develop and find training programs to match where it is most needed.
Test employees with pop quizzes to see what information the employees have mastered and what needs more review.
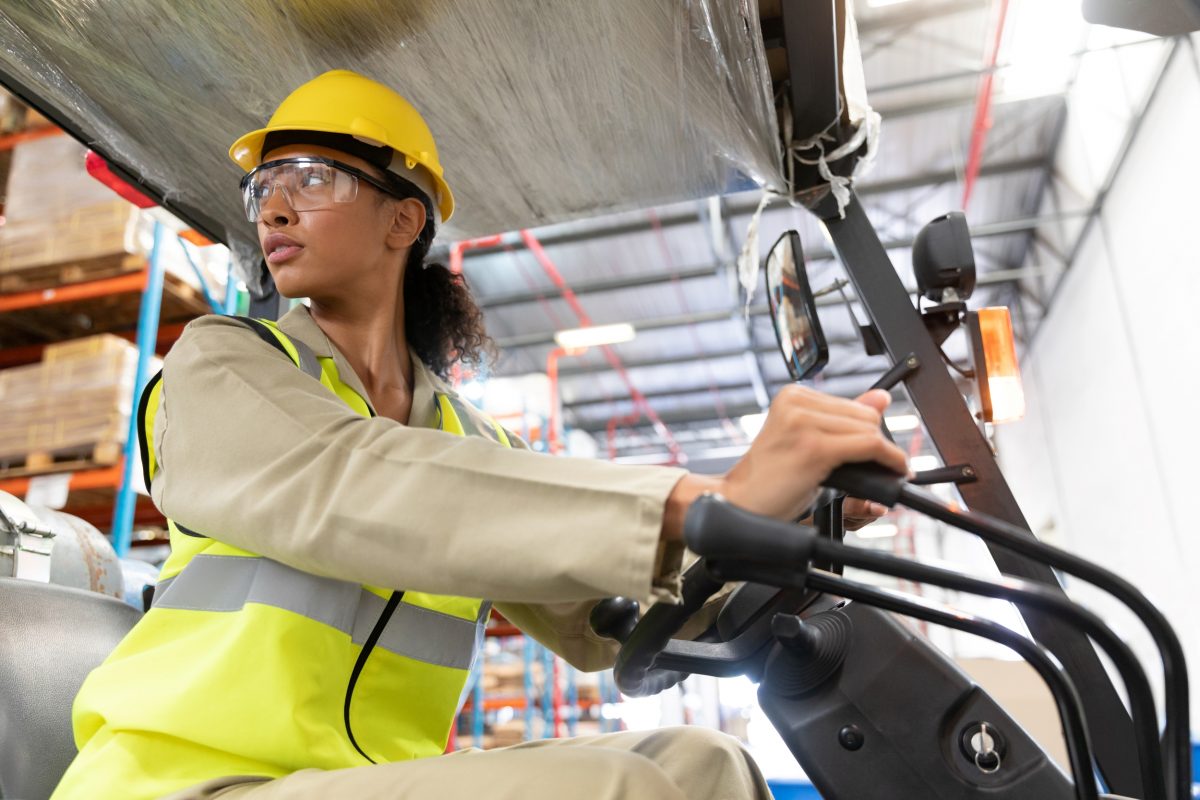
Warehouse Safety Meeting Topics
An extension of training, regularly scheduled meetings are integral to keeping safety at the forefront of employees’ minds.
Warehouse safety topics to cover:
- PPE
- Forklifts
- Walkways
- Loading docks
- Hand trucks
- Lift table
- Hazardous materials
- Conveyors
- Material storage
- Charging stations for equipment
- Fire safety and evacuation plans
- Medical emergencies
- Ergonomics
- Heat illness prevention
The above safety meetings are available as free templates in Safesite. To access them, create a free account or download the Safesite app on Android or iOS. Then, search the meeting template library to find the one you want. Next, edit it to fit the needs of your organization. Finally, conduct your meeting, take attendance, and log your meeting — all using your mobile device.
Warehouse Safety Checklists
Keeping all the safety requirements straight can be a daunting task. Use checklists to ensure nothing slips through the cracks. Here are a few examples from our article on essential warehouse checklists:
- The Worker Safety Series: Warehousing includes safety checklists covering general safety, materials handling, hazard communication, and forklift safety.
- Walkthrough: Meant to be checked once a month, this list covers general warehouse areas, interior and exterior docks, equipment, sanitation, and general safety.
- Forklifts: Because forklifts are part of a warehouse worker’s daily job, it’s important they are well-maintained and workers receive proper training. Parts of this checklist can be used daily.
- Ergonomics: Protect your employee’s bodies by assuring that they use proper ergonomics during their daily duties.
Each of these checklists is available as a template in Safesite. To access them, create a free account or download the Safesite app on Android or iOS. Then, search the template library to find the checklist you want. Next, edit it to fit the needs of your organization or use the checklist as-is and immediately conduct an inspection with your mobile device.
Standard Operating Procedures
Every warehouse safety plan should also include Standard Operating Procedures. These SOPs outline in detail how to perform various warehouse jobs and duties, so that everyone who needs to do those can follow the same protocols. SOPs should incorporate safety checklists, everything covered in training and emergency procedures.
Safety Observations, Inspections, and Audits
With over 7 million workplaces under its jurisdiction, OSHA does not have the capacity to inspect all workplaces unless a report of unsafe conditions or illness/injury occurs.
Avoid OSHA inspections by remaining in compliance. Warehouse owners and managers should conduct their own audits and inspections. Basic high-level inspections should be done daily or weekly, while a detailed audit should be done at least once a year.
Warehouse Safety Rules and Tips
Below are warehouse safety tips covering different areas that can help get you started as you put together your own safety management plan.
General/OSHA
- Rope off, chain off or block any open docks where an employee could fall 4 or more feet.
- All floors and aisles should be clear of anything that employees could trip on or over.
- Give plenty of rest breaks and assign employees attainable and realistic goals.
- New employees should receive ergonomic training.
- Warehouses should be well ventilated.
- Employees should be trained in working in extreme hot or cold conditions.
- All facilities should have lockout/tagout procedures.
- Keep emergency buttons or pull cords for conveyors at each employee workstation.
- Instruct and train on how to handle fire, natural disaster and other hazard emergencies.
- Train all employees on safety vernacular and terminology.
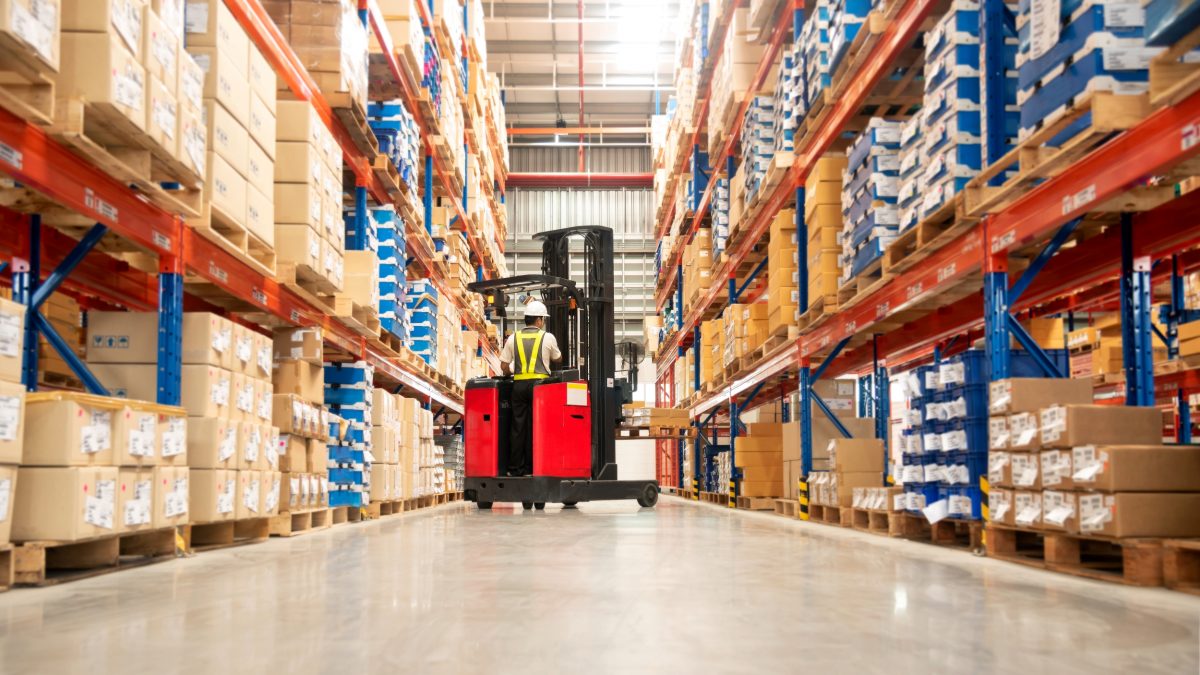
Stacking/Loading/Unloading
- Stack loads straight and keep items as even as possible.
- Put heavier loads on lower shelves.
- Remove tripping hazards from storage areas.
- Keep hazardous materials that could lead to fire, explosion or pest infestations in designated storage areas.
- Keep safe clearances for aisles where mechanical handling equipment is used.
- Center loads as close to the forklift mast and centered on the forks.
- Cross-tier loads when stacking for greater stability.
- Separate non-compatible goods to keep storage stabile.
- Paint walls or posts to show maximum stacking height.
- Adhere to height limitations when stacking materials.
Forklifts
- Operators must be trained and licensed by the company.
- Inspect the forklift before each use.
- Always look every direction before moving the forklift.
- Wear a seatbelt at all times.
- Only operate the forklift in a well-lit area clear of any hazards.
- Do not allow anyone but the operator to be on any part of the forklift during operation.
- Workers not operating the forklift should always be aware of where it is operating.
- Do not overload the forklift or lift the load above unsafe heights.
- Create designated paths for forklifts to travel safely.
- Sound forklift horn at intersections, crosswalks and in other busy areas.
Cold Storage
- Give employees proper cold environment work attire.
- Remove ice buildup regularly and keep all areas clean.
- Install safety features like doors that can unlock from inside and alarms in case of lock-ins.
- Regularly check on employee’s health and physical fitness to make sure they can handle the rigors of cold storage.
- Provide regular training on what to do in case of a lock-in or other type of emergency.
Signage and Tape
- Create an organizational system that works best for your warehouse and label accordingly.
- Identify potentially hazardous areas like docks, entrances and exits, etc. and clearly mark emergency exits.
- Follow OSHA guidelines for signage colors: red for danger, yellow for caution, and orange for warning.
- All equipment (forklifts, manual lifting machines, etc.) should have directions for operations as well as hazard warnings printed on them.
- Charging stations should be well labeled and include instructions on what to do in case of a fire in that area.
- Use Caution or Danger tape to temporarily isolate areas where pedestrians would be at risk when motorized machinery is in use.
Ergonomics/Lifting Tips
- Whenever possible, use powered equipment instead of manual lifting.
- Train workers when and how to use manual lifting equipment.
- Assure all areas of the warehouse have proper overhead lighting.
- Teach and reinforce proper lifting techniques.
- Always use legs when lifting and keep your back in a natural position.
- Test the load weight, size and bulk before lifting to determine the best way to lift.
- Ask for help if a load is too heavy or bulky for manual lifting.
- Don’t twist while carrying a load; shift your feet in small steps to move directions.
- Make sure workers have proper safety gear including gloves, safety glasses, hard hats and steel-toe boots.
- Give employees with injuries plenty of time to rest and recoup before returning to normal work activities.
Warehouse Management Solutions for Safety Challenges
All these tips and resources are helpful for general safety concerns in a warehouse. What do you do with special situations or when especially tough problems arise?
Behavior-Based Warehouse Safety Program
A relatively new concept in the safety and risk management sphere, Behavior-Based Safety programs start by changing behaviors to increase safety. These programs are a collaboration between employer and employee and require cooperation on both sides.
With BBS, employees are observed in various work situations. Employers then use that data to determine ways they should train employees to react, behave or act differently in a safety situation.
Work with HR to Develop Safety-Related Policies
Work with your human resources department to develop policies, expectations, and accountability plans related to safety behavior. Work safe behavior into your job descriptions and leadership development plans.
Create a Positive Safety Culture
Safety in the workplace should also be part of the company’s culture. From the top managers down to the employees, everyone needs to buy into an atmosphere of safety. Here are several ways companies can create a positive safety culture:
Communicate, Communicate, Communicate
Always keep the lines of communication open between management and employees, among co-workers and from the company to the public. This transparent atmosphere assures that everyone is on the same page safety-wise and can move toward common goals. Open communication also assures that when problems do arise, they can be solved quickly and efficiently.
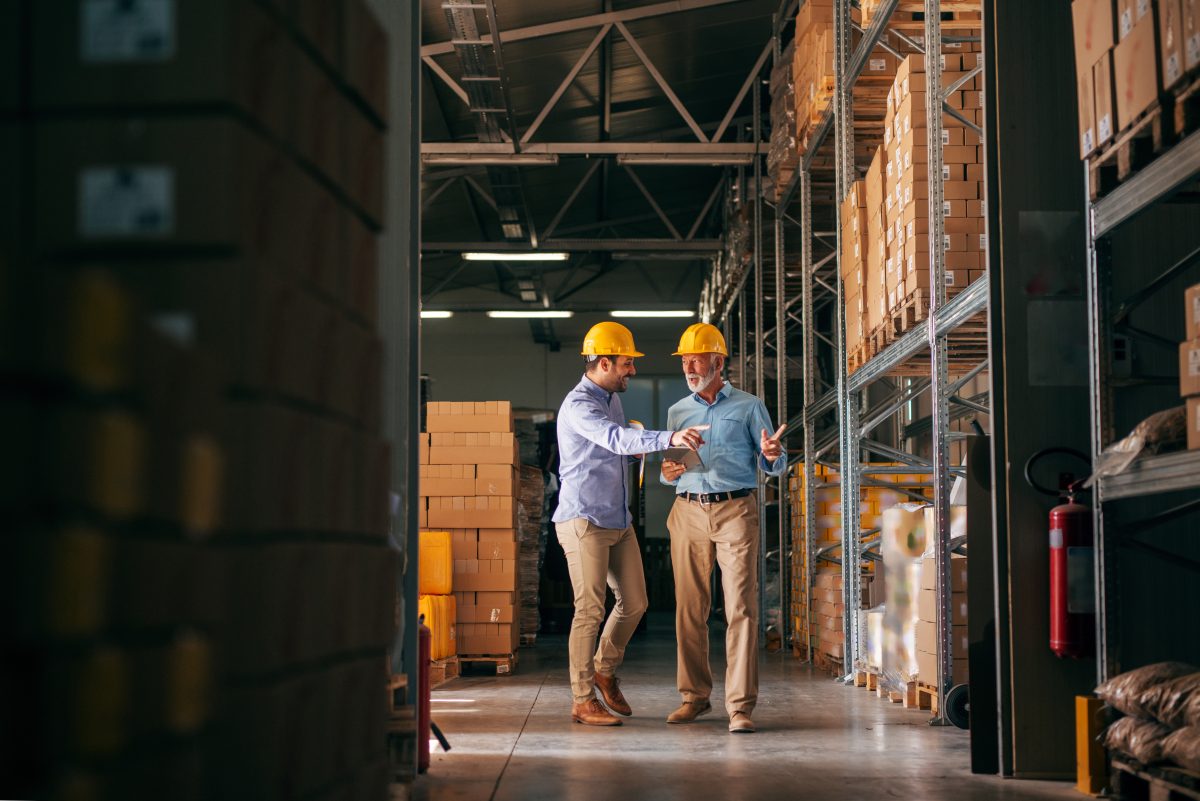
Talk about safety at every company meeting, mention it in employee newsletters and other publications and provide plenty of opportunities for training. When communication is encouraged and expected, it allows for better accountability across the board.
Care About Worker Wellbeing
Developing safe workers and a safe work environment starts with management and top leaders caring for their workers and their wellbeing. This begins from the time a manager hires an employee and continues throughout that employee’s time with the company.
When an employee feels like those in management roles actually care about them, they often perform better with better output. Employees who feel valued at work also tend to remain loyal to that employer.
Pay Attention to Risky Behaviors
Even if it’s done in jest or a joking manner, risky behaviors are a red flag for other unsafe actions. If an employer sees workers engaging in horseplay, pranking, teasing and/or bullying, they should address the situation. These types of actions can lead to more serious unsafe behaviors and disregard your culture of safety.
Reward Safety
Positive reinforcement is another effective way to encourage safety in the workplace. Industry Week offers several easy ways to reward safety including:
- Setting both long-term and short-term goals that are reasonable and attainable. Some examples include “lowering the minor injury rate by 10% for next year” and “100% attendance at the next safety meeting”.
- Combine different types of programs, using recognition rewards along with monetary and merchandise rewards.
- Recognize workers’ efforts publicly and often. Seeing their co-workers working hard and getting rewarded for it can motivate other employees. Recognizing positive behaviors also reinforces your culture of safety.
- Give out frequent, small rewards rather than just a few big rewards. This keeps the rewards attainable to more people and makes workers more likely to want to earn them.
Invest in Leadership Development
A company can assure their culture of safety continues by raising up leaders well versed in those ideas and beliefs. Company leaders should invest in leadership development programs to raise up the next generation of leaders in the company.
Even if those workers don’t move into higher roles in the company, leadership development gives them a sense of ownership in the company, making them more likely to work hard and be loyal. When company leaders lead by example, this helps employees understand the importance of safety and why the company places it in such a high category.
Conclusion
Creating a safe and productive warehouse setting starts with a culture of safety. This culture should be reinforced by the managers at all levels, especially executives and owners.
Creating a safe working environment begins with a safety plan that covers all parts of the warehouse and applies to all employees. Owners and managers should expect to put resources of time and money toward safety and willingly build these costs into the overall budget.
Employers should always remember that safe employees are more productive and more likely to remain loyal to the company. If employers take care of their employees, their employees will take care of their jobs.