The new shipment of personal protective equipment has arrived, and your safety team has distributed the PPE to all employees. A few days later, as you make your rounds, you notice more than one worker using their PPE incorrectly — and several not using it at all.
From purchasing and distribution to ensuring it’s worn correctly, it takes a PPE management plan to be truly effective in protecting your employees and fulfilling OSHA requirements.
What Are the OSHA PPE Standards?
OSHA requires all employers to provide appropriate PPE to all employees wherever needed. According to OSHA standards, employers are responsible for:
- Identifying when and where personal protective equipment needs to be utilized
- Choosing and providing appropriate PPE
- Training employees in using, maintaining, and replacing PPE as needed
- Ensuring PPE is used properly
As you can see, following the above standards may be simple or complex depending on the type being used. The standards are general so you must discern how they apply in your situation.
If your current method isn’t working or you don’t have one in place, read on for tips on creating, implementing, and overseeing a PPE management plan.
How Important is a Well-Oiled PPE Machine?
When creating a safety program and setting PPE guides for your company, it’s crucial that management and ownership are driving the movement. Employees won’t buy into any safety standards unless those leading them do the same.
Managing your company’s PPE systematically not only saves lives and prevents injuries, it helps your business operate more efficiently and cost-effectively. That’s why having a practical, organized approach to management is crucial.
Stop Problems Before They Start
By applying the hierarchy of controls, your company can eliminate some of the problems that lead to needing PPE in the first place. The hierarchy of controls can be used on machinery, equipment, processes, and procedures. The theory behind the hierarchy of controls is that the higher methods on the pyramid are more effective, so it’s best to start there and work your way down.
At the top of the hierarchy of controls pyramid, elimination is just what it sounds like — removing the hazard itself. Examples of elimination include removing toxic chemical splashes in a manufacturing process or finding tools that allow workers to stay on the ground instead of working at heights, etc.
Following elimination, substitution attempts to replace the hazard with a safer option, such as using water-based paint rather than solvent-based paint. In the middle of the triangle is engineering controls, which isolates workers from the hazardous source. This can include controls like mechanical guards, fences, safety mats, and two-hand controls.
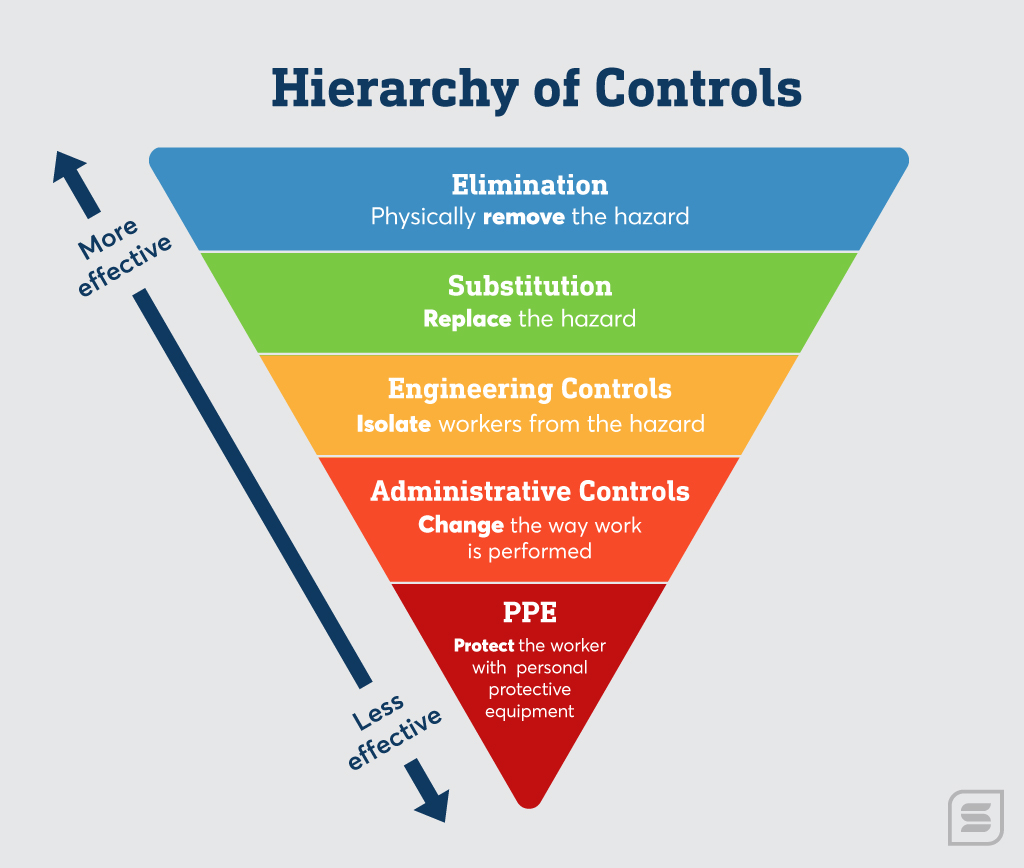
These three methods actually remove the hazard from the source, keeping the worker from even coming into contact with it. While these are the most effective options, it’s not always feasible to implement them. They can be cost-prohibitive or interfere with the equipment or process itself.
When the first three methods aren’t working or can’t be used, employers move down to administrative controls, which changes how employees do their jobs. Administrative controls can include training, signage, and procedural changes. Finally, the last method is personal protective equipment.
While PPE procedures are inexpensive and easy to start, the costs add up over the long term and can become cumbersome to manage. This is why an employer should make every attempt to use elimination, substitution, engineering controls, and administrative controls before resorting to PPE.
Be Proactive vs. Reactive: a Case Study of Current Events
When you’re dealing with the safety of employees, it’s critical to be proactive rather than reactive. Having a PPE management plan in place puts your company at an advantage in non-crisis times and is integral in case of emergency.
The COVID-19 pandemic in 2020 revealed the importance of being proactive rather than reactive when it comes to health and safety issues. A large number of hospitals and medical centers ran out of PPE in the middle of the crisis.
Many factors led to the lack of PPE, including broken supply chains and inflated prices, but in general, companies that had effective PPE management plans in place were better able to weather through the crisis. Those that didn’t have a forward-thinking plan in place were scrambling to secure the items they needed and be able to use them successfully.
Facing a worldwide pandemic is the worst-case scenario; even the best-laid plans may not protect against something so major. But, it’s still important to have a plan in place to alleviate some of the negative effects of an emergency situation.
Create Your PPE Management Plan
Every company should perform a hazard assessment to determine if the first four hierarchy of controls can eliminate hazards. If they cannot and the company must use PPE, the assessment will help you determine the types and number of PPE you’ll need for each employee and type of job.
Step 1: the PPE Hazard Assessment
During a hazard assessment, look for both physical hazards like tripping points and moving objects, as well as health hazards such as exposure to harmful chemicals. Develop a list of hazards that fit into OSHA’s basic hazard categories:
- Penetration
- Compression (roll-over)
- Chemical
- Heat/cold
- Harmful dust
- Light radiation
- Biological
Pay attention to the types of materials that employees interact with or exposed to, including chemicals and hazardous energy sources. Watch your employees as they complete their tasks so you can get a first-hand view of what would work best for PPE. You could even ask them questions to get their insights on what would make their job safer.
Step 2: Identify Your Committee Members
After you have completed the hazard assessment, you can craft a PPE management plan, starting with evaluating different models and choosing the best fit for your employees.
Most safety plans include safety committees made up of management and employees. Your company’s safety committee should be hands-on in creating your PPE management plan.
If you will have a large number of employees utilizing PPE, it can be helpful to create a subcommittee under your safety committee to oversee the plan creation and implementation.
The committee will determine who in the management team will be directly responsible for the PPE side of safety. Or, the committee may determine if the PPE responsibilities will fall on a group of employees. Determining responsibilities will help alleviate any issues down the road, as everyone knows their role and can fulfill it accordingly.
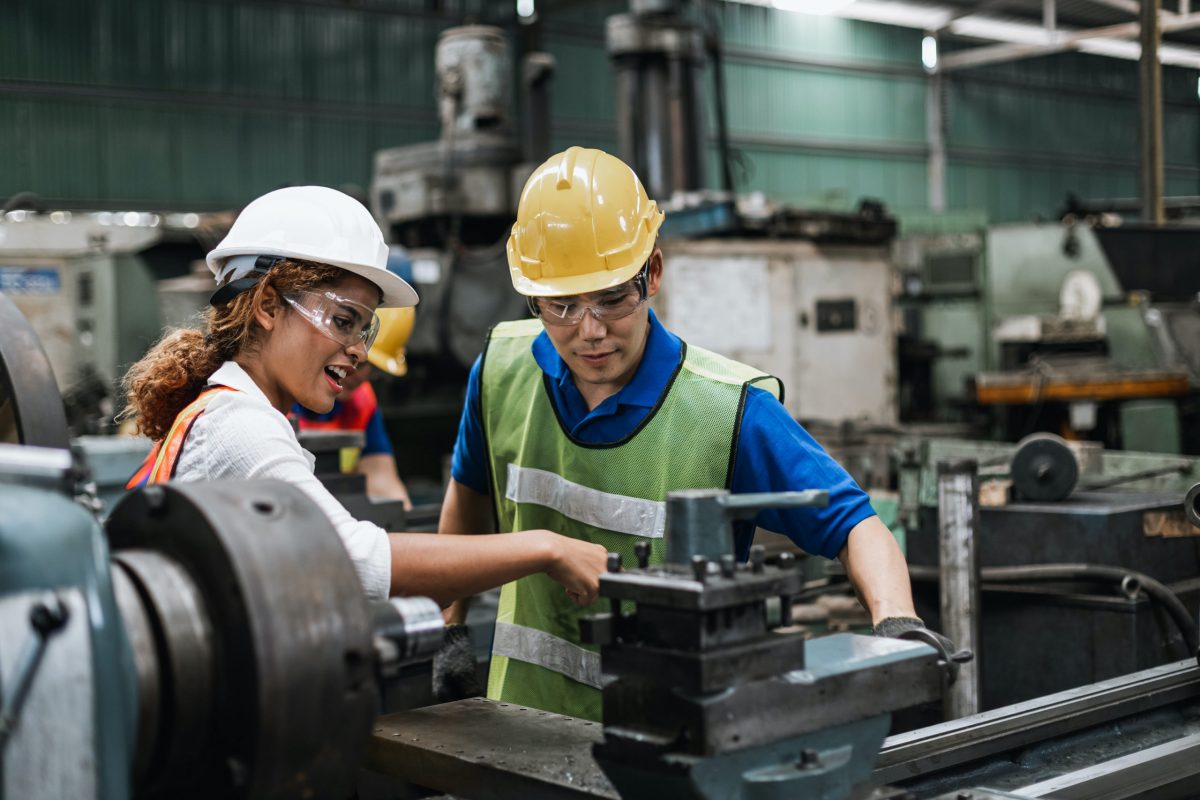
Step 3: Draft Your PPE Management Plan
The exact content of your PPE management plan will depend on your company’s needs. Some common areas to cover include:
- Purpose statement explaining why the plan is necessary and how it will benefit the company
- A section outlining who in the company is responsible for each part of the plan
- Guidelines for each type of PPE that will be used at your company
- Training guidelines
- PPE checklists that will be used to monitor your plan
Put Your PPE Plan Into Action
Your company’s PPE management plan has been researched, vetted, and is now ready to be put to use. These next steps include purchasing PPE and training employees on proper PPE use.
Step 1: Strategize for the Best Case Scenario
As you’re evaluating the types and number of PPE you’ll need, consider how each piece of safety equipment will be used and if there are ways it can be used in more than one way. PPE doesn’t have to be a one-trick pony; many types of PPE can be applied for different situations.
When your company uses fewer types of PPE, it not only saves money over the long run, but it also makes it easier for the employee to manage. Having fewer types of PPE for employees to worry about means they can focus more on their job and taking other steps to stay safe.
The evaluation phase of your PPE management plan is all about doing your research. A PPE supplier is a great source of information for what types of PPE work best for each type of job and employee your company utilizes. These companies can help you find solutions, understand the longevity of a certain PPE product, and provide insight on managing inventory and distributing PPE to employees.
Don’t wait to engage with PPE suppliers until you’re ready to purchase; involve them early to make the safest and most cost-effective decisions.
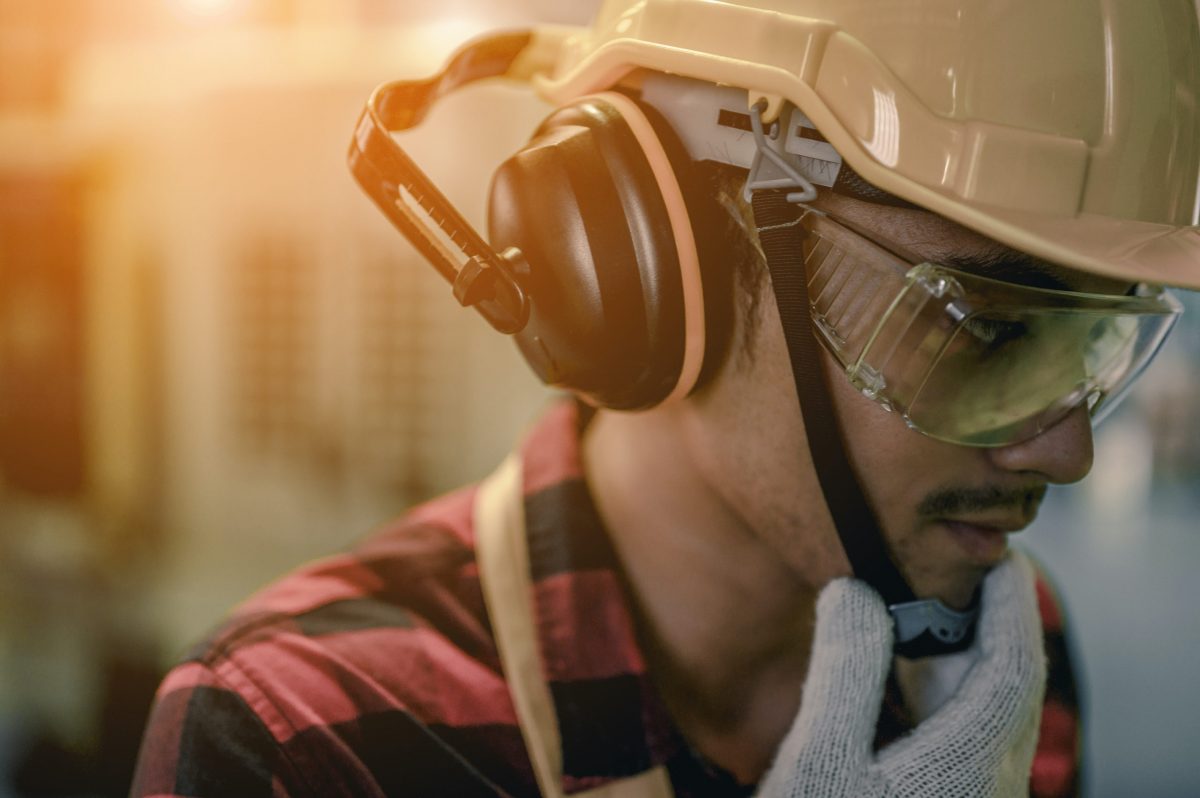
Step 2: Shop for the Cost, Convenience, and Features
Once you’ve done your homework, gather quotes from several different PPE suppliers and shop around for not only the best prices but the best products. Price is important but it’s crucial to make sure you’re also protecting your employees with a high-quality product that they will wear.
Explore your options and be sure your PPE hazard assessment considers various types used at the same time.
Know the pros and cons of various features in all PPE categories:
- Gloves
- Safety goggles, glasses, and face shields
- Head protection and hard hats
- Masks and respirators
- Hearing protection
- Gowns, overalls, and leggings
- Safety shoes, steel toe boots, and shoe covers
- Fall arrest systems
If possible, stick to just a few reputable vendors for purchasing PPE. While it may save money to buy your gloves from this vendor, glasses from another, and face shields from a third company, this will be hard to manage long-term.
When it comes time to reorder or if you have issues, it will be much easier to deal with just one or two vendors. Customer service and quality products are just as important, if not more important, than the cost.
It’s helpful to include key employees and safety committees in the evaluation and purchasing processes. This helps them buy into the safety plan even more and they can be important ambassadors to the rest of your workforce.
Step 3: Invest in Training
The best PPE in the world won’t be effective unless it’s used correctly. Create a plan to fulfill OSHA’s PPE training requirements, including proper usage, storage, and maintenance. Your training plan should include:
- What hazards each type of PPE protects against
- Why and when PPE is needed
- How to spot issues
- Hands-on demonstrations — how to properly don, doff, adjust, and wear PPE
- Limitations
- Proper care, maintenance, and disposal of PPE
For every one of your employees that must use PPE, you must document and keep records of their training. Once each employee completes the training, you’ll give them a completion certification that lists the name of the employee, date of training, and the type of training.
If you have multiple types of PPE to train on, keeping track of training and certifications can be cumbersome. Look for a safety management app like Safesite to have a tool in hand for tracking inspections, near miss and incident reports, and PPE training.
Implement, Observe, and Improve
You’ve created a PPE management plan, made your initial purchases, and trained your employees. Now it’s time to implement best practices and observe your team with the aim of improving down the road.
Don’t Overlook the Fitting Process
If the PPE doesn’t fit correctly, it won’t be effective in protecting the employee or your employee might not wear it all. Take the time to measure each employee for each type they’ll need. When your employee needs to wear multiple types at once, make sure all the PPE are compatible with each other.
The American National Standards Institute (ANSI) has developed engineering standards around various job site hazards; be sure everything you purchase adheres to these standards.
Invest in Automated PPE Vending Machines
These come with a larger upfront cost but will save money and time in the long-run. Be sure that employees know how to properly use the machines so they do not waste PPE. You’ll also want to come up with a plan with who will maintain the vending machines so they are always full and ready for employees to use. PPE vending machines are also an easy way for you to track inventory and the lifecycle of the various models in use.
Dependable vending options:
Continuously Audit Your Equipment
As mentioned above, in the hierarchy of controls, PPE is the last line of defense for employees. Use regular inspections to ensure the state of your equipment is good to excellent at all times.
While some employees can exhibit stubborn habits around properly wearing and caring for PPE, don’t forget that behind the behavior, there may be a piece of equipment making it difficult or uncomfortable to do their jobs well. Remember to audit for practicality and wearability.
Include PPE in Your Safety Culture
Along with training, signage, lockout/tagout, and other safety procedures, PPE should be a natural part of your company’s safety culture. Don’t just train employees what to do, communicate why it’s important.
But don’t stop there: look for opportunities to give workers the opportunity to influence and mentor their peers in a positive way. This may be a PPE donning/doffing activity during a toolbox talk or a new employee mentorship program.
Require Visitors to Use PPE
Your company’s PPE policies should include any visitors to your site. Decide how you plan to provide visitors with safe and clean PPE when they’re visiting your facilities.
Involve All Employees in PPE Procedures
Even if an employee will never have to use PPE, it’s important that all employees understand the procedures and importance of PPE. The health and safety of a company should not rely solely on the shoulders of the safety committee or team, but should be everyone’s shared responsibility.
Perform Regular Inspections
Just as auditing and inspections are crucial to other areas of safety, it’s important to conduct regular inspections of your PPE. The Safesite safety management app is an excellent tool for scheduling and conducting regular PPE inspections.
Consult the OSHA Guidelines
This Safety Health and Program Management publication provides recommendations you can use as you run your program. It covers four main areas: management leadership and employee involvement, worksite analysis, hazard prevention and control, and safety and health training.
The Bottom Line in PPE Management
Besides the fact that OSHA requires it, PPE usage will save your company money, improve productivity, and prevent employee injury and death. PPE management should be an integral part and a priority in your company’s overall safety management system.
Your PPE management plan should start with a hazard assessment to determine what types, models, and features you need. From there, you’ll create a plan for purchasing, training, and performing regular safety audits to be sure PPE is being used correctly.