Safety management: it sounds simple enough. Only safety professionals know the power packed into such a small term: the depth of learning, planning, coordination, interpersonal skill, and raw perseverance involved in keeping workers safe.
The Safety Manager’s Guidebook series covers every aspect of health and safety program management. Get a concise overview of established safety management systems, system design, and safety management skills.
In this part of the series, the Ultimate Guide to Safety Management Systems, career safety director David Paoletta explores established health and safety frameworks. By the end, you’ll be able to use what you’ve learned to improve your company’s processes and workflows.
What is a Safety Management System?
A Safety Management System (SMS) is a program for promoting safety and reducing risk to employees at work. It is implemented by an organization to identify, assess, and control hazards to employees and the public in all operations.
Effective safety management systems prevent injuries, process failures, and improve the long-term profitability of the companies that implement them.
Approaches to Safety Management Systems
In order to design an effective system, you need to be familiar with the primary frameworks for safety management systems in operation today, including:
ANSI Z-10
ISO 45001
OSHA Safety Management Guidelines
Behavior Based Safety
Fundamentals of Scientific Management
New View of Safety Management
I’ll walk through each one and then discuss applying them in the second part of the article, Designing Your System.
But First: Organizational Management
No overview of safety management systems would be complete without a discussion of organizational management. Safety management practice is derived from basic principles of business management, financial management, quality management, and, when needed, the organization and administration of bureaucracies.
Management is defined as “the interlocking functions of creating corporate policy and organizing, planning, controlling, and directing an organization’s resources in order to achieve the objectives of that policy.”Contemporary safety theorist and writer Thomas R. Krause uses the following definition: “’management’ is getting work done through others” (Leading with Safety).
Politicians, academics, and businessmen have been talking about management since at least 500 BC, when Sun Tzu wrote “The Art of War” — still studied in business schools and military academies to this day.
Bureaucracy Hasn’t Alway Been a Bad Word
The word bureaucracy has come to be associated with needless complexity and inefficiency. But at the turn of the century, work (especially manufacturing) was transitioning from small-scale artisanal production into large-scale centralized production.
Nations and States were also starting to provide civil services and regulate more of their citizens’ daily lives, leading to the need to organize and larger and larger workforces.
German sociologist Max Weber was the first to officially study bureaucracy, defining it as “… an organizational structure that is characterized by many rules, standardized processes, procedures and requirements, number of desks, meticulous division of labor and responsibility, clear hierarchies and professional, almost impersonal interactions between employees.”
Weber’s Bureaucratic Organization was characterized by:
- Specialization of employee function
- Hierarchy of management authority
- Selection of employees on the basis of education, experience or suitability to the task
- Rules and regulations, codes of conduct, etc. and a disciplinary system to enforce them
- Objective (i.e. impersonal) relationship between management and employees
- Career orientation (i.e. specialization leads to expertise in an area leading to lifetime employment)
The bureaucratic coordination of the action of large numbers of people has become a dominant structural feature of modern safety program management systems. It is only through this organizational device that large-scale planning and coordination become possible.
This bureaucratic approach is often necessary to organize safety activities to align them with the numerous compliance requirements of local, state and federal enforcement agencies such as the Occupational Safety and Health Administration (OSHA, Federal & State); the Environmental Protection Agency (EPA, Federal & State); Department of Transportation (DOT, Federal and State), State and Local Fire jurisdictions, State Workers Compensation Authorities, and private insurers.
Scientific Management
In 1911 Frederick Taylor published The Principles of Scientific Management. In it, he notably asserted, “In the past the man has been first; in the future the system must be first.”
During Taylor’s time, factory work was accelerating and large numbers of unskilled people were moving to the cities from rural areas of England to find work. Management at this time focused on utilizing this unskilled labor by breaking work tasks into easily understandable, sequential processes that were optimized for early factory production lines.
The scientific management approach to safety can be seen in organizations with rigid rules and procedures guiding work, rigorous training and educational requirements for employees in certain roles, and strict oversight and enforcement of company rules.
Industries like commercial airlines and nuclear facilities are examples of organizations using the bureaucratic and scientific safety management approaches to ensure compliance with internal rules and outside regulators.
Beyond Bureaucracy
While bureaucracy and scientific management are proven approaches to reducing injury and days-away rates, there are limits to the true effectiveness of any safety system.
An overly rigid, bureaucratized, and compliance-based management structure can serve your company but leave your employees weakened by a lack of knowledge and initiative.
The safety structure you choose must exist to protect your organization from enforcement actions and fines, yes, but more importantly, it should increase the engagement and participation of every employee in your safety initiatives.
An Overview of ANSI Z10
Founded in 1918 by five engineering societies and three government agencies, the American National Standards Institute (ANSI) remains a private, nonprofit membership organization supported by a diverse constituency of private and public sector organizations.
ANSI is a non-governmental organization that manages the production and publishing of consensus standards. These standards, including the ANSI Z10, are produced by committees of subject matter experts from universities, national laboratories and individuals, industry representatives, and representatives from relevant government organizations. Most standards are revised and updated at three-year intervals to reflect industry best practices and emerging technologies.
What is the ANSI Z10?
ANSI Z10 is an American consensus standard (developed by a committee of volunteer experts) that outlines a complete safety management framework and process for improvement. The original standards-making committee was approved in 1999. The first edition of ANSI Z10 was released in 2005.
The ANSI Z10 standard is organized to contain eight required elements. Most company safety management programs based on the Z10 standard are written to conform to these sections for ease of auditing after implementation.
- Scope, Purpose, and Application
- Definitions
- Management Leadership and Employee Participation
- Planning
- Implementation and Operation
- Evaluation and Corrective Action
- Management Review
- Appendices
One of the goals of a program such as ANSI Z10 is to foster continuous improvement; i.e. process management and hazard reduction steps included in the process lead to fewer injuries and operational failures year-over-year.
Steps 3 through 7 are considered to be a continuous improvement cycle, usually graphically presented as a never-ending circle or infinite loop.
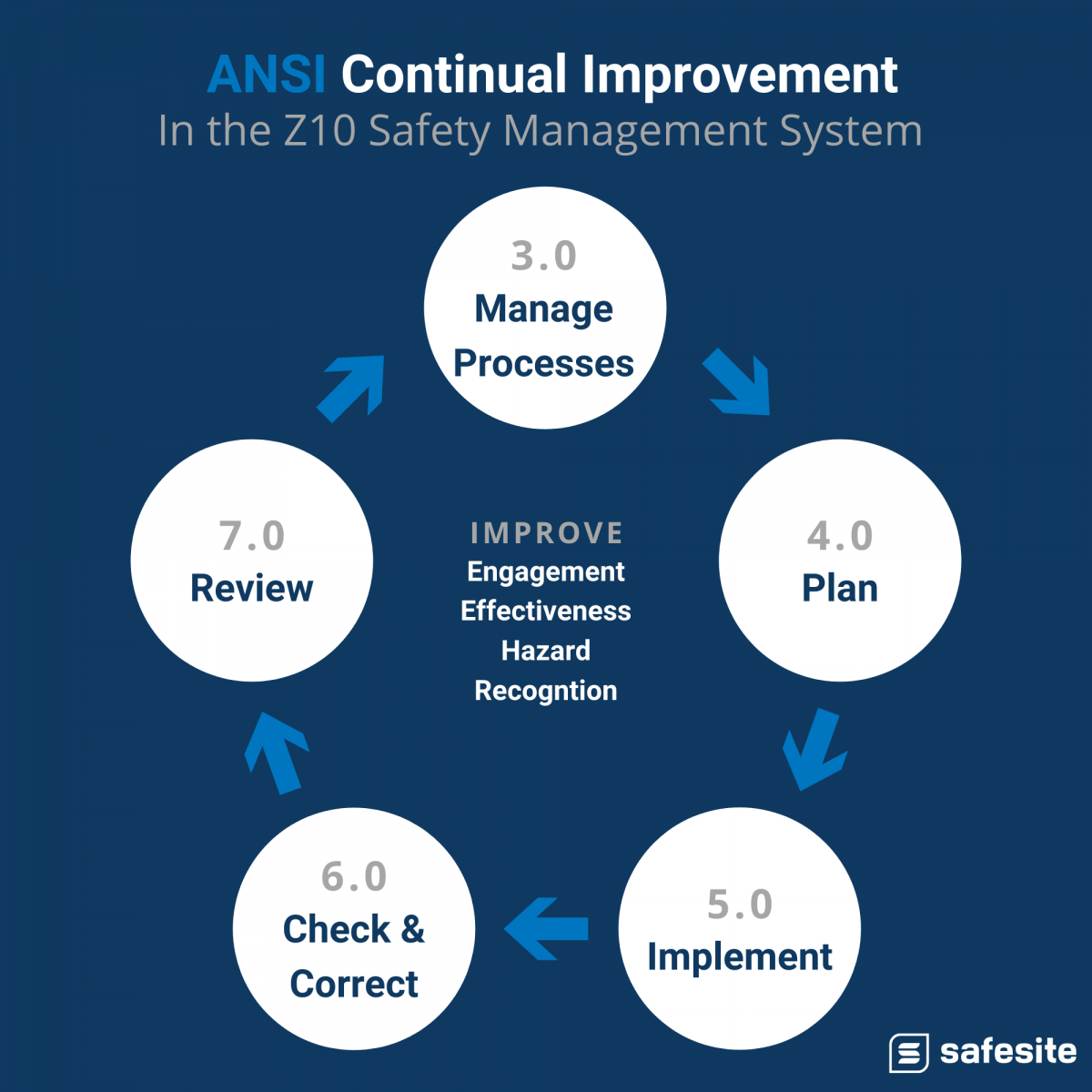
Fred Manuele elaborates: “Throughout all sections of Z10, from management leadership and employee participation through the management review provisions, a key theme is prominent: Processes for continual improvement are to be in place and implemented to ensure that:
- hazards are identified and evaluated
- risks are assessed and prioritized
- management system deficiencies and opportunities for
- improvement are identified and addressed
- risk elimination, reduction or control measures are taken to
- ensure that acceptable risk levels are attained.”
The ANSI Z10 organization is harmonized with the other major standard-making body, the International Organization for Standardization (ISO). The ISO is an international standard-setting body composed of representatives from various national standards organizations.
ISO-45001 is an International Standard that specifies requirements for an occupational health and safety (OH&S) management system similar in scope to the ANSI Z-10 and will be discussed below.
It’s important to note that this is a framework for a safety management system and not a prescriptive set of policies and procedures to be followed by every organization.
The intent is for companies to use this process to analyze their unique operations, risks, and hazards and to develop a set of policies and procedures, training, and self-audit activities that are the most effective for their activities.
Over time, as performance metrics are tracked, further optimization of the process should result in improvements to safety and health.
I will highlight several sections that can help define and explain this management approach to those unfamiliar with ANSI Z10:
Section 4.0 – Planning
The first step in the continuous “Plan–Do–Check–Act” process laid out by ANSI Z10 is to design a system for performing an assessment of current safety programs and identifying places for improvement. This is commonly called performing a “gap analysis” and should involve people within the organization who have a range of job descriptions and functions.
A key component of this is performing a risk assessment of operations that identifies the probability of something going wrong and the estimated severity of an event. That way the company can prioritize the higher risk operations and work on the most serious ones first, directing time and resources towards issues that directly affect safety. This leads into the next step: risk assessment.
Section 5.1.1 – Risk Assessment
This section establishes the requirement for organizations to conduct formal risk assessments and hazard analysis of their activities and worker exposures. From there, the company establishes programs such as respiratory protection, PPE, hearing conservation, fall protection, machine guarding, etc.
The standard says, “The organization shall establish and implement a risk assessment process(es) appropriate to the nature of hazards and level of risk.”
The specific form and complexity of the resulting programs should reflect the level of hazard determined by the hazard analysis process used.
For example, a drywall company may be required to have a respiratory program for its workers exposed to silica, but the PPE and work rules required for employee safety in the drywall trades are much simpler to comply with than a respirator program for a company with welders cutting and welding stainless steel tanks.
In this example, the welders are exposed to toxic metal particles and fumes that require tight-fitting air-purifying respirators or supplied air respirators; while the drywaller may only need N95 disposable masks. The medical monitoring program required for the welders would also be more complex and expensive (i.e. blood tests are required) than the simple respirator medical fitness exam for the drywall finishers.
When the hazard analysis determines that there is no hazard present (e.g. there is no production machinery to be guarded at a software company), then there is no need to establish a program. The initial hazard analysis and subsequent analysis of any process or equipment change will be used to justify the lack of a program in the event an enforcement agency inquires about it.
Section 6.0 – Evaluation and Corrective Actions
This section describes the requirements for processes to evaluate the performance of the safety management system, to take corrective action when shortcomings are found, and to provide feedback to the planning and management review processes. The section also contains guidance on performing post-accident incident investigations and program-wide audits.
Section 6 is one of the most important to achieve continuous improvement because if the audit and corrective action processes are not meaningful, then the changes recommended will not be meaningful improvements.
About ISO 45001 and OHSAS 18001
The OHSAS 18001 was developed by the British Standards Institute (BSI) and others in 1996. By 2007, it was superseded by ISO 45001 and is no longer actively supported.
Organizations already certified to OHSAS 18001 have until March 2021 to comply with the new ISO 45001 standard if they want to maintain recognition (certification of conformity to ISO 45001 is not a requirement of the standard).
What is ISO 45001?
ISO 45001 is an International Standard that specifies requirements for an occupational health and safety (OH&S) management system, with guidance for its use, to enable an organization to proactively improve its OH&S performance in preventing injury and ill-health.
ISO 45001 is intended to be applicable to any organization regardless of its size, type, and nature. All of its requirements are intended to be integrated into an organization’s own management processes.
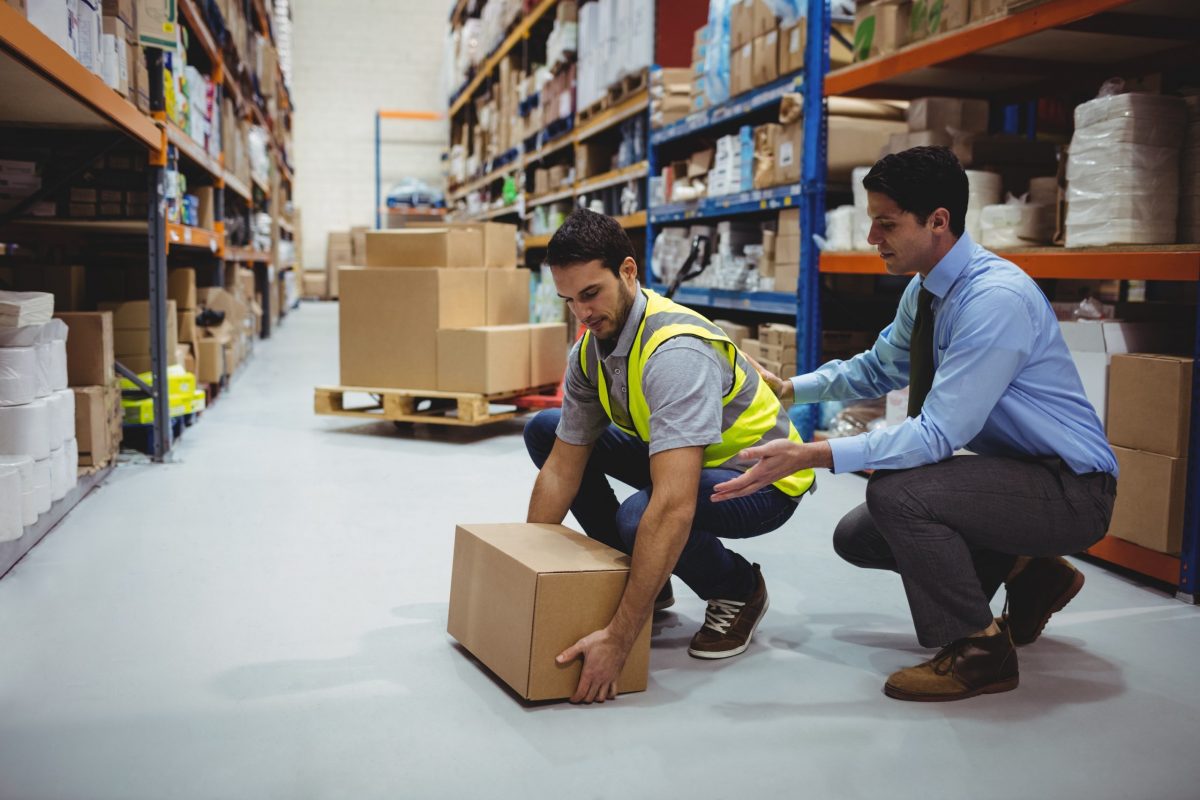
The standard enables an organization, through its OH&S management system, to integrate other aspects of health and safety, such as worker wellness/wellbeing; however, it should be noted that an organization can be required by applicable legal requirements to also address such issues.
ISO 45001 does not state specific criteria for OH&S performance, nor is it prescriptive about the design of an OH&S management system.
An organization’s OHS management system should be specific to meeting its own needs in preventing injuries and ill-health; consequently, a small business with low risks may only need to implement a relatively simple system, whereas a large organization with high levels of risks may need something much more sophisticated.
Any type of system may be adequately in compliance with the requirements of the standard, provided it proves to be appropriate to the organization and is effective.
As long as your organization has people working on its behalf, or who may be affected by its activities, then using a systematic approach to managing health and safety will bring benefits to it.
The standard can be used by small low-risk operations equally as well as by high-risk and large complex organizations. While the standard requires that OH&S risks are addressed and controlled, it also takes a risk-based approach to the OH&S management system itself, to ensure that it is a) effective and b) being improved to meet an organization’s ever-changing context.
This risk-based approach is consistent with the way organizations manage their other business risks and hence encourages the integration of the standard’s requirements into organizations’ overall management processes.
ISO 45001 follows the high-level structure approach that is being applied to other ISO management system standards, such as ISO 9001 (quality) and ISO 14001 (environment).
In developing the standard, consideration has been given to the content of other international standards (such as OHSAS 18001 or the International Labour Organization’s ILO–OSH Guidelines) and national standards, as well as to the ILO’s International Labour standards and conventions (ILSs).
Along with the benefits of applying the ISO processes to managing safety in an organization, there are some costs, including the monetary cost of certification from the ISO organization and administrative costs involved with developing the documentation and recordkeeping infrastructure required.
Some companies have become so focused on maintaining the systems required to validate the certification that process changes leading to new hazards failed to be identified.
The OSHA Safety Management Guidelines
In the US, safety laws and regulations are what most people associate with OSHA. However, OSHA provides non-mandatory safety management system guidelines to help employers think beyond the rules.
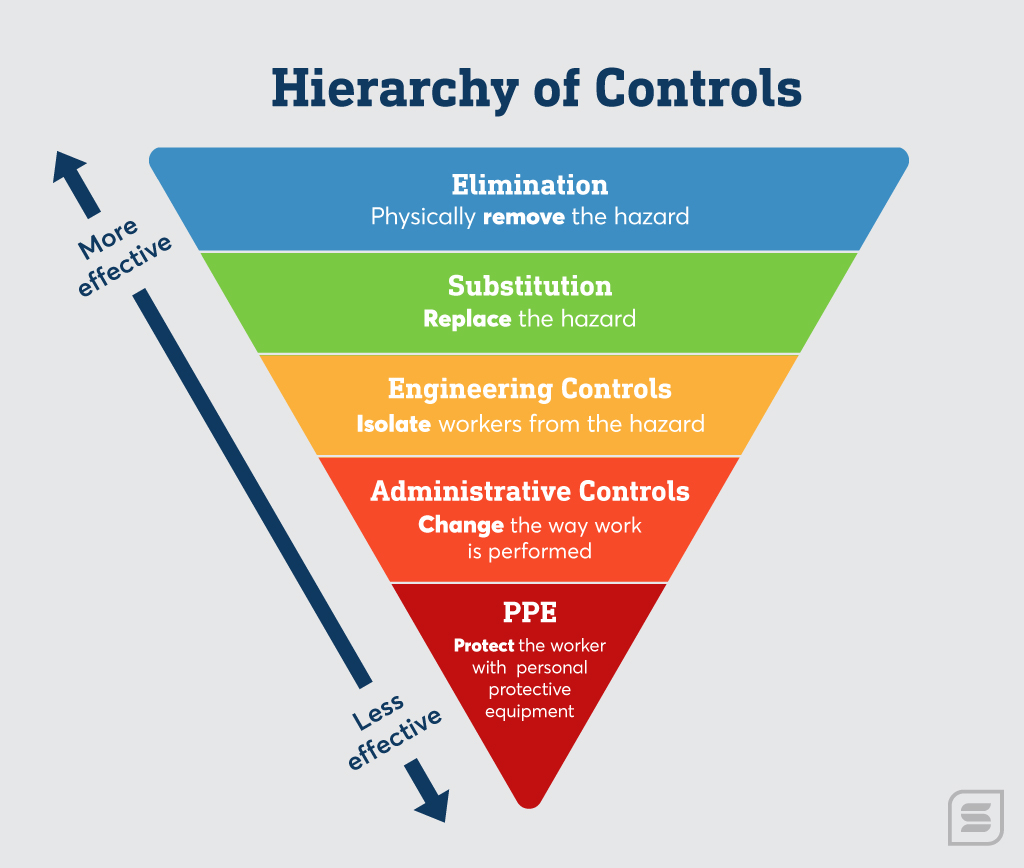
The OSHA Safety Program Management Guidelines, first published in 1989, are a simple framework for ensuring that essential compliance programs are put into practice at the organizations that require them. The Recommended Practices for Safety and Health Programs were updated again in October 2016.
As I mentioned, the practices are not mandatory and OSHA cannot cite a company against them. The basic elements consist of:
- Management Leadership
- Worker Participation
- Hazard Identification and Assessment
- Hazard Prevention and Control
- Education and Training
- Program Evaluation and Improvement
- Communication and Coordination for Host Employers
- Contractors and Staffing Agencies
ISO vs. OSHA vs. ANSI Management Systems
As you can see, there is a high degree of overlap between the ISO 45001, ANSI Z10, and OSHA safety management system approaches. Basic principles behind effective safety management — process improvement, worker participation/training, and risk assessment/control — have not changed much over time.
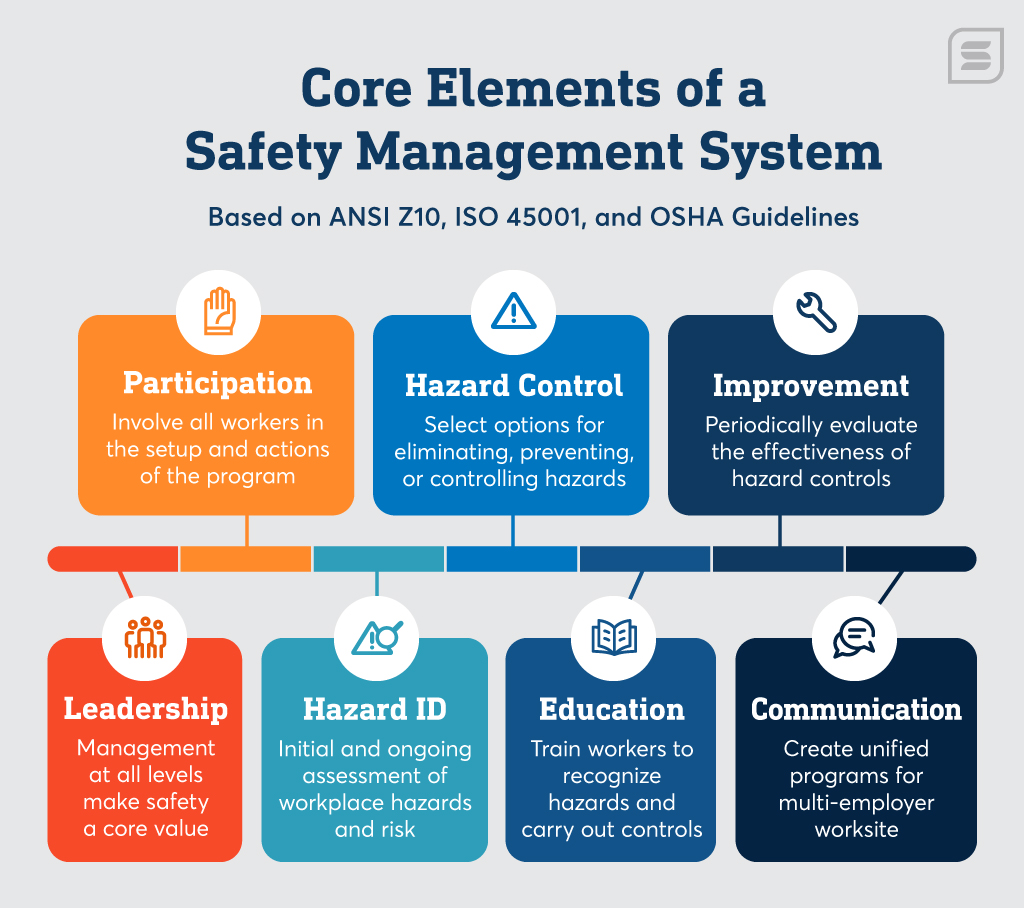
No matter which framework is selected, success depends upon management support, employee involvement, and a willingness to analyze hazards and make the necessary changes within the organization.
Long-term success involves consistent leadership from the Environmental Safety and Health Department and a robust change management process.
Whatever the framework, safety management success depends on management support, employee engagement, a willingness to make changes when necessary.
Behavior-Based Safety (BBS) Systems
The behavior-based approach to safety was originally an outgrowth of B.F. Skinner’s (1938-1971) experimental analysis of human behavior.
Without considering internal factors such as people’s attitudes, intentions, etc., Skinner instead focused on observable behaviors that are unsafe or undesirable in the workplace. Interventions are then designed to modify behaviors in the direction of safer or more efficient outcomes.
Over time, the behavior-based approach to occupational safety was refined and offered to businesses by for-profit safety consultants as opposed to international standards-setting organizations.
Original thinking by Geller, Krause, Peterson, and others leveraged the human psychology of earlier studies and refined techniques of observation and metrics for use in a wide range of industries.
There are many methods of implementing a BBS system, but most rely on the steps below:
- Designate an implementation team of Managers, Supervisors and Line Workers who are knowledgeable about the process.
- Perform analysis of past injuries, near-miss accidents and plant disruptions. Develop a list of “safe” behaviors to be encouraged and reinforced.
- Develop a checklist to be used for safety observations that will yield numerical data for comparison over time.
- Create a dashboard or other method to track and compare metrics over time.
The success of a behavior-based system is largely determined by the quality of the checklist and the willingness of the workforce to be observed and participate in the improvement process.
Organizations have used both positive incentives and negative consequences to encourage compliance with varying degrees of success, but too often, only the hourly workforce is faced with the oversight and critical feedback involved in operating the program.
The Fundamentals of Scientific Management
Working at the turn of the twentieth century, Frederick Taylor was a Mechanical Engineer studying industrial efficiency in early factories. He was the first to look at the manufacturing process and how workers interacted with it, with the objective being maximum production from each individual. Taylor published his masterwork “The Principles of Scientific Management” in 1909.
According to Frederick Taylor, the principal object of management should be to secure the maximum prosperity for the employer — coupled with the maximum prosperity for each employee.
The words “maximum prosperity” are used, in their broad sense, to mean not only large dividends for the company or owner, but the development of every branch of the business to its highest state of excellence, so that the prosperity may be permanent.
In the same way, maximum prosperity for each employee means not only higher wages than are usually received by men and women of their class, but more importantly, it also means the development of each man and woman to their state of maximum efficiency. The result is that people may be able to do, generally speaking, the highest grade of work for which their natural abilities fit them, and it further means giving them, when possible, this type of work to do.
It would seem to be so self-evident that maximum prosperity for the employer, coupled with maximum prosperity for the employee, ought to be the two leading objectives of management. To state this fact seems unnecessary.
Scientific management, on the contrary, has for its very foundation, the firm conviction that the true interests of the two are one and the same; that prosperity for the employer cannot exist through a long term of years unless it is accompanied by prosperity for the employee and vice versa, and that it is possible to give the worker what they most want—high wages—and the employer what they want—a low labor cost—for their manufactures.
How Taylorism rose and fell in the early 20th century:
- Taylor deconstructed manufacturing tasks and rationally optimized tooling, sequence, and line speed to optimize output.
- WWI made it necessary to optimize industrial production at a time when Taylor’s theories were popular.
- Although Taylor argued that workers should benefit from increased efficiency as much as owners, these benefits largely failed to trickle down.
- Taylor’s “time and motion studies” yielded a maximum output/worker/time that was unsustainable over the workday. Efforts to adjust for worker variation came to discredit “scientific” management.
- Although Taylor’s approaches to manufacturing line optimization are still valid and in use today, the negative associations of “Taylorism” with respect to the exploitation of labor have become part of our culture.
Today the term “Scientific Management” is still used as an approach to studying and understanding complex workplace tasks and interactions and bringing engineering, chemistry, ergonomics, and other scientific fields of study to bear on improving safety in organizations.
Current efficiency and quality approaches such as LEAN and Six-Sigma utilize tools developed during the era of Taylorism to analyze and improve workflow, plant layout, and worker ergonomics.
The New View of Safety (Safety-II)
The New View of safety, also called Safety-II, came about in the late 1990s and 2000s. During this time, practitioners and academics in the safety field began to question the effectiveness of the traditional safety management practices described above.
Although the rate of workplace illnesses and injuries had been reduced from 11.0 in 1973 to 6.1 in 2000 (representing recordable injuries per 100 workers), fatalities had not been reduced to the same extent.
In fact, the average occupational fatal injury rate in US industries has hit a statistical “plateau,” stuck at 3.4 since 2008 (R. Gantt, “Safety Differently – A New View of Safety Excellence,” Session 590, ASSE Proceedings, Feb 2015.
So industry leaders and insurers began to ask why all of the money invested in safety staff, equipment and procedures, training and safety audits had not virtually removed every hazard and prevented every injury by now?
Why did so many “Drive to Zero” safety programs have such minimal results?
As illustrated above, traditional safety practice tends to be backward-looking and based on responding to failures like injuries and lost days. Accident analysis focuses on behavioral and system failures that result in injuries or process interruption.
Although the effort put into understanding “what went wrong” and trying to fix it is effective in preventing the recurrence of the exact same failure (assuming the corrective actions selected are effective long-term), focusing solely on preventing recurring failures precludes an understanding of 99.99% of the other actions that do not result in accidents.
In other words, safety staff often spends time looking at the wrong things.
The Flaw in Heinrich’s Triangle
The concept that serious accidents occur after a finite number of minor accidents (i.e. the Injury Pyramid Theory) was developed by H.W. Heinrich in “Industrial Accident Prevention: A Scientific Approach”(1931).
“Heinrich’s Pyramid” as it came to be called, can be found on safety posters in company break rooms worldwide; and the belief that by eliminating minor injuries and unsafe conditions, the major breakdowns and catastrophes would be avoided has launched a thousand corporate safety initiatives.
Unfortunately, Heinrich got it wrong, since some of the worst industrial accidents in recent times—the Challenger explosion, Deep Water Horizon disaster, the Texas City Refinery fire, etc.—have happened within organizations with OSHA VPP status and below industry average injury and illness rates.
Clearly, minor incidents and major catastrophes were not statistically linked as common sense, as Heinrich’s theories would indicate.
According to the U.S. Chemical Safety Board’s analysis of the Texas City refinery explosion, “BP Texas City explosions was an example of a low-frequency, high-consequence catastrophic accident. Total recordable incident rates and lost time incident rates do not effectively predict a facility’s risk for a catastrophic event.”
Beyond Anticipating and Correcting Failures
Recognizing that the nature of organizations and work processes has become so complex and interrelated that conventional approaches to hazard analysis are no longer up to the task of anticipating and correcting likely failures, a new approach is clearly needed.
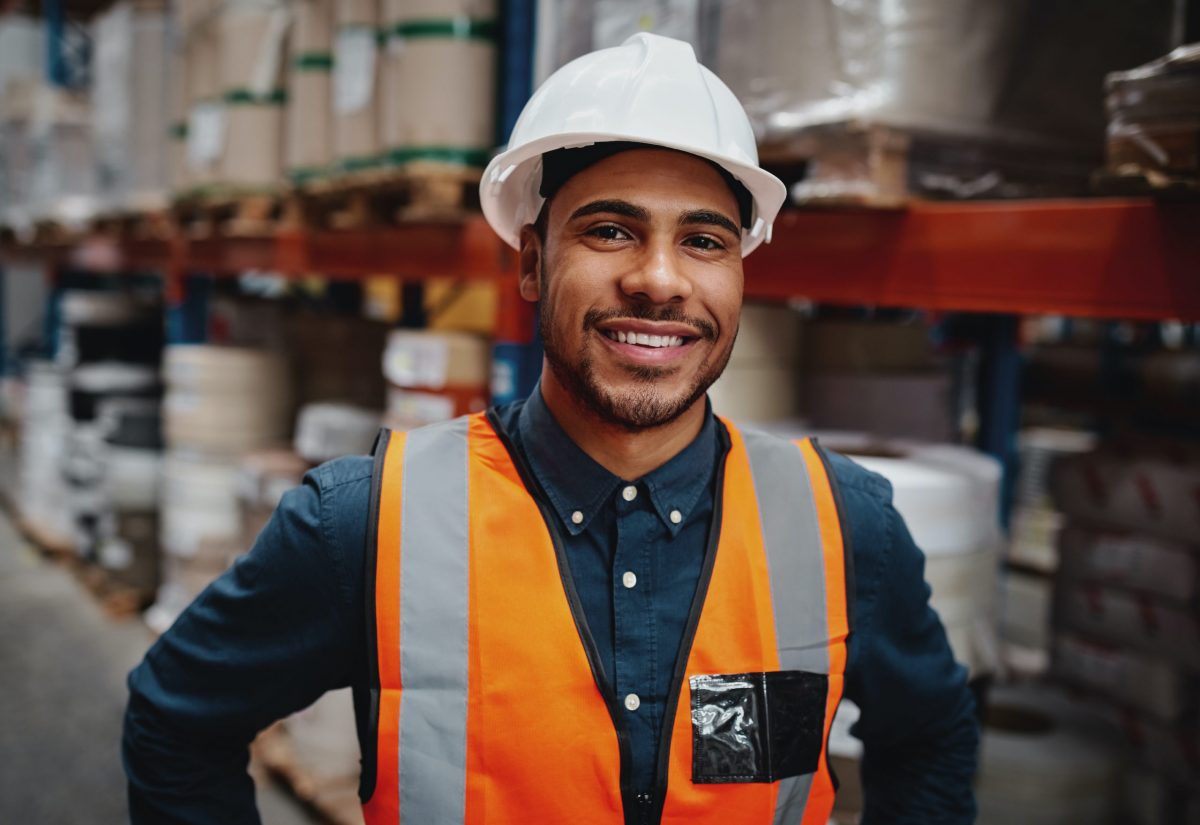
“Safety and risk in a complex system are not a matter of controlling, governing, standardizing, and understanding individual components. So-called system accidents (Perrow, 1984), while rare, are caused by the interactive complexity of the system itself…System accidents result from the relationships between components, not from the workings or dysfunction of any component part.” (Dekker S, The Safety Anarchist, p. 134 (2018)
This includes actions and inactions of workers who are part of an increasingly complex process. Although a worker may make a “mistake” to start a chain of events, it’s the system design and operating characteristics that determine if the consequences will be catastrophic or minor.
The New View Explained
“New View” safety programs are not based on checking the usual compliance boxes that traditional safety management is built on. Since many companies embrace New View principles after having used a conventional approach for many years, they already have the compliance-driven, audit-based, highly bureaucratic structures in place.
The goal in these companies is to increase the effectiveness of the safety effort and to reduce injuries and hopefully guard against those low-probability, high-impact catastrophic accidents.
Breaking down some of the bureaucracy and emphasizing employee operational knowledge over the “expert” knowledge coming from the Safety and Quality departments is a first step.
Some broad principles of the new safety approach are listed below: (Todd Conklin, Pre-Accident Investigations, 2012)
- Safety is not the absence of accidents; safety is the presence of defenses.
- Humans are born to make mistakes.
- Employees come to work wanting to perform their jobs well.
- Workers don’t cause failures (failure is built into the system).
- Workers are not problems to be fixed, but solutions waiting to be found.
- After an accident, you can blame and punish or learn and improve.
This approach places a high value on employee knowledge and focuses on communications between the shop floor, safety department, production, and quality.
Allowing employees to influence work processes and use their knowledge to drive system improvements is the key to New View Safety Management.
With Safety-II, safety staff concentrates on the 99% of worker actions that result in positive outcomes and use the occasional incident or failure as a learning opportunity to understand how the system failed and what might be done to make predictable failures have less severe consequences.
Designing Your Safety System
So far, we’ve reviewed many of the pillar concepts of safety management. Some systems have been used for over one hundred years and some are still being researched and deployed in workplaces.
Of course, consensus systems like ISO 45001 are meant to serve as a guide for all sorts of work environments, from the office to the plant to the job site. Your specific SMS has to make sense for your company’s size, workflows, hazards, personnel, and regulatory jurisdiction.
Whether you want to build safety into the way you do business from the ground up or want to improve processes that have remained the same for years, the following steps will help you plan and execute your program.
1. Identify Hazards
At the most basic level, all a company has to do is “provide a workplace free from serious recognized hazards and comply with standards, rules, and regulations issued under the OSH Act.”
Simple right? But answering that question has grown a thriving industry in safety consulting and software management systems! The challenge is in determining which regulations your company needs to comply with, how to manage compliance, and how to document that you are managing it.
The best place to start is with a reference like OSHA’s Small Business Handbook, available free at the OSHA website.
This reference contains guidance on how to perform a self-inspection at your business to determine if specific OSHA requirements — for example, Lockout Tagout — apply to you. It even contains a checklist to aid the process:
- Download the OSHA Construction Self-Inspection Checklist (.PDF) or access it as a DOC template.
- Download the OSHA General Industry Self-Inspection Checklist (.PDF) or access it as a DOC template.
A similar process is called Task-Hazard Analysis (THA). To perform a THA, get employees, supervisors and engineers who know the most about the business together and list all of the different job steps and tools and other materials that are used in the process.
2. Build a List of Essential Programs
Then, using technical data like Safety Data Sheets for chemicals, determine the worst case of what could harm employees or damage the facility if there is an accident.
Match up the hazards with applicable OSHA, EPA, etc. regulations that are required for compliance, and build a list of the essential programs from there. For chemicals, you will create a Hazard Communication Program, and so on and so forth.
3. Identify Roles and Responsibilities
Part of designing the SMS is to assign roles and responsibilities to those who will be responsible for keeping them up to date and managing them.
Typically, accident reporting and OSHA recordkeeping is assigned to the company’s Workers Compensation program administrator because so much confidential personal data is involved.
In the absence of a dedicated safety specialist or safety manager, the other programs should be assigned to supervisors and managers who can lead them.
The Maintenance Manager usually has responsibility for electrical safety, Lockout-Tagout, Confined Space Entry, Overhead Hoists & Cranes, etc.
The Operations Manager or Production Manager often leads facility inspection programs such as Portable Fire Extinguisher Inspections, Emergency Action Plan, Walking-working Surfaces, etc.
How the roles are split up is not as important as making sure that the important programs are implemented and maintained.
4. Implement Safety Training
In the area of training and records management, some companies implement a parallel system called Safety Training Management (STM). Most OSHA regulations require employee training, and some, like forklift operations, require very specific recordkeeping.
Smaller companies will typically determine training needs (i.e. who needs the training and how often) and place them on a training matrix organized by job title, then create a perpetual training calendar to better spread the various types of training out over the course of the year.
Individual employees should have a record of all training received, including dates, instructor name, and a description of the topics covered. Training programs requiring quizzes, exams, or on-the-job demonstrations should also be kept in the employee training file.
For larger companies or companies with distributed workforces like electrical contractors, keeping track of all this becomes a full-time job. That’s why safety management software has been developed and refined to include training and certification tracking.
5. Manage Information with Technology
Although the basic requirements for OSHA compliance haven’t changed much, the ability to manage information about the company’s compliance program has grown far easier.
Regardless of whether your SMS is on a spreadsheet or carried on a server in the cloud, the process for determining what OSHA standards are relevant to your business and what type of hazards your employees are exposed to while on the job is still the basis for any safety management system.
Building on the Foundations
Most organizations assert that their safety program is about protecting workers when it is actually more focused on accidents (and preventing them).
Remember that the single-minded focus on lowering incident and days-away rates in American industry has led to an overly rigid, bureaucratized, and compliance-based management structure.
Such a structure exists to protect the organization from enforcement actions and fines rather than concentrating on building knowledge and resilience into the workforce. Accident prevention does not always equal safety.
Safety Management Systems for Real People
In my research into how different management approaches actually work in real companies, I have noted some practices which tend to be successful across all types of industries and management models:
- Management that is truly safety-oriented (and makes resources available to prove it)
- Well-trained, motivated safety staff, who report directly to top management yet spend their time with workers in the factory, on the job site, etc.
- Employees who feel valued and can bring their concerns to management without fear of reprisal
- Supervisors and forepersons who reflect management’s concern for safety and act accordingly
- A learning atmosphere where processes and procedures are constantly questioned and upgraded
Moving forward, new safety principles will prove their worth by addressing the statistics, yes — but only as an outgrowth of lowering the hazard level that company employees are exposed to doing their jobs.