LOTO has a reputation in the construction, manufacturing, and industrial industries, but it’s not always a great one. According to OSHA, violations of Lockout/Tagout procedures consistently rank high for most serious workplace violations and most often cited violations.
Organizations like OSHA, the NSC, and NFPA are taking steps to change that reputation by encouraging best practices for implementing better control of hazardous energy procedures and providing more effective LOTO training.
The Lowdown on LOTO
Lockout/tagout processes govern machinery and equipment that expose workers to hazardous energy. LOTO procedures give workers the steps to properly shut-down machinery and equipment and isolate the sources of energy before they begin service or maintenance work.
Following proper LOTO procedures means fewer injuries and deaths from accidents from inadvertent start-up and contact with hazardous power sources. LOTO procedures secure the hazardous energy sources in these machines, preventing the machine or equipment from accidentally starting up (or from a co-worker turning it on) while it’s undergoing maintenance or service.
It’s not enough to turn off the machine; all energy sources must be controlled and locked before guards and panels are removed and work is begun. In other words, only the workers who locked out the machine are allowed to have access to the LOTO keys: one man = one lock + one key!
OSHA’s Role in Lockout/Tagout
In its standard 29 CFR 1910.147, OSHA provides the requirements employers must follow for LOTO in the workplace. These standards cover creating a LOTO plan and policy and implementing safe LOTO procedures in the workplace, including training and auditing.
OSHA 29 CFR 1910 is the gold standard for lockout/tagout policies and procedures, but the organization also references LOTO in other standards including 29 CFR 1915 (Maritime), 1917 (Railroads), 1918 (Maritime-cargo), and 29 CFR 1926 (Construction).
LOTO Training Best Practices
LOTO procedures and plans are useless unless the employer puts training programs in place to pass along that information to its employees. To help employers implement training programs and best practices, OSHA provides resources and information on LOTO training.
A plethora of other training information is available to companies as well, through organizations like the National Safety Council and National Fire Protection Association.
OSHA Training Programs
OSHA LOTO training programs offer everything a company needs to get started creating a training program that suits its employees and work environment.
OSHA Lockout-Tagout Interactive Training Program
This online, interactive tool is easy-to-use and offers a comprehensive look at OSHA standards. Rather than creating a training program from scratch, an employer could use this online program to train employees.
It has three main components. The Tutorial portion explains the LOTO standards in question and answer format. The Hot Topics section takes users through five abstracts, providing a detailed discussion of major issues with LOTO. In the Interactive Case Studies portion, users are in control, following through seven simulated LOTO inspection scenarios and choosing the correct answers based on LOTO standards.
Topics covered in the training program include:
- Overview
- Scope and Application
- Purpose
- Definitions
- Energy Control Program
- Energy Control Procedures – Documentation
- Energy Control Procedures – Required Content
- Periodic Inspection
- Employee Training and Communication
- Additional Training (Tagout System)
- Employee Retraining
- Lockout/Tagout
- New or Modified Equipment
- Full Employee Protection
- Materials and Hardware
- Application of Energy Control
- Release from Lockout/Tagout
- Testing of Machines
- Outside Personnel (Contractors)
- Group Lockout/Tagout Requirements
- Shift and Personnel Changes
OSHA Lockout/Tagout Plus Expert Advisor
This diagnostic software for employers is an excellent way to learn the basics of LOTO and how they apply to a specific worksite. The program asks questions about a company’s equipment that uses hazardous energy sources, often posing follow-up questions based on the answers.
Using these answers, the program offers suggestions on which OSHA standards apply to that workspace and prepares a customized report.
While these tools are effective and helpful, OSHA does not recommend it as the only source of information. OSHA suggests that companies still utilize safety and health professionals when assessing their LOTO needs.
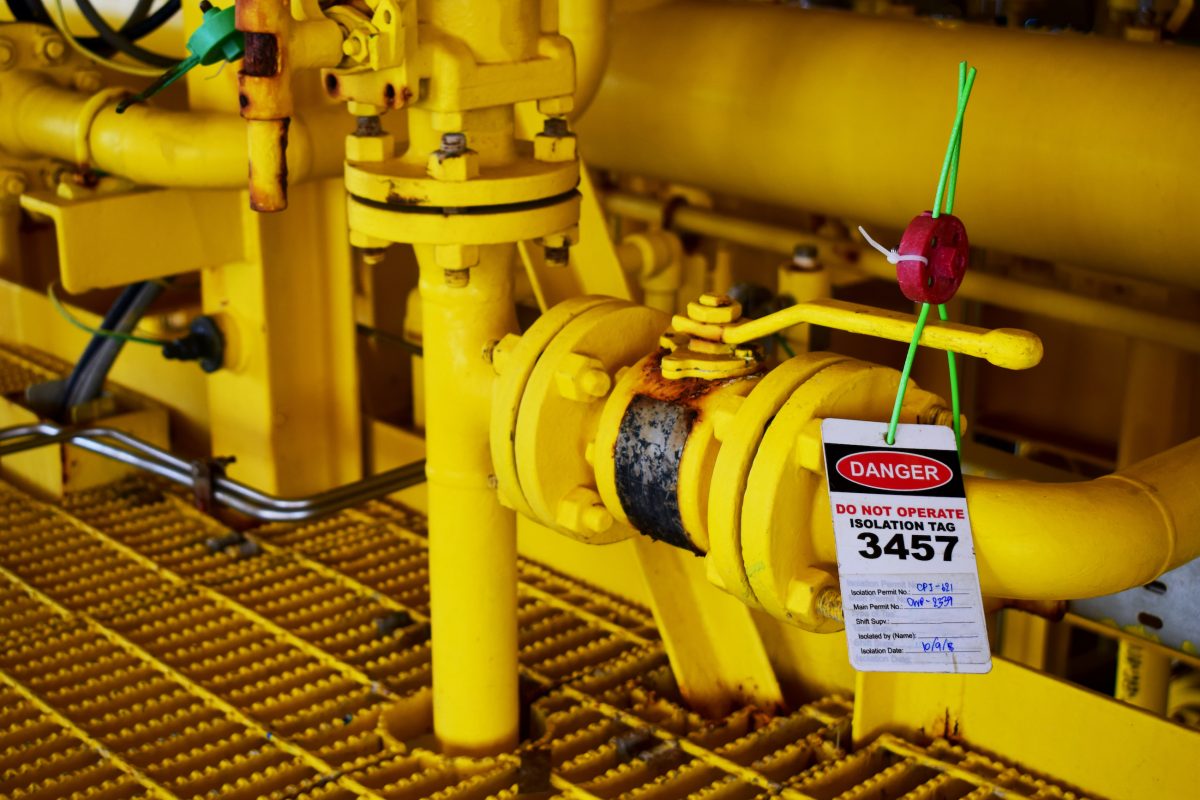
National Safety Council Training Programs
The National Safety Council (NSC) offers several training programs created for management, human resources personnel, safety and health committee members, and employees with LOTO responsibilities.
After attending one of these training programs, attendees will have the knowledge to create and implement a LOTO program and training for their employees. They’ll also learn how to use the NSC resource guide to follow OSHA standards and access checklists and contact lists.
The NSC training programs cover:
- Purposes of lockout/tagout
- Key components of a lockout/tagout program
- Main elements of LOTO procedures
- Self-inspections of energy control devices
- Group LOTO
- Performing testing or positioning on equipment being repaired
NSC training programs come in several different formats. A company or employer can purchase the NSC Lockout/Tagout Facilitator Kit to run their own training sessions. This kit is available for purchase via the NSC website.
The NSC also has online training modules available for companies and individuals to buy. These training modules cover a wide variety of safety and industry issues and include eight lockout/tagout specific courses.
For companies looking for comprehensive safety training, the NSC will come to them. Onsite safety training from NSC covers numerous safety topics and onsite training courses can be combined for a full training experience.
National Fire Protection Association Training Programs
The National Fire Protection Association (NFPA) offers several training programs created for companies that perform maintenance and repair on electrical components and systems. This training is geared towards Qualified Electrical Workers, EHS personnel and Managers with LOTO responsibilities.
After attending a live or online training program, attendees will have the knowledge to create and implement a LOTO program that complies with NFPA 70E’s Standard for Electrical Maintenance and training for their employees.
The NFPA training programs cover:
- Introduction to Electrical Safety and the 2018 NFPA 70E
- Electrical Hazard Analysis
- Establishing an Electrically Safe Work Condition
- Working While Exposed to Electrical Hazards
- Personal Protective Equipment
- Safety-Related Maintenance and Special Equipment
NFPA training programs can be accessed via the NSC website.
Training Plans
Employers looking for a more personalized training experience can create their own training plan and program. Or, they can customize a sample program from another company or organization.
The Texas Department of Insurance and the Maine Department of Labor, for example, provide sample written programs on OSHA’s website. These programs are free for other companies to use and modify to suit their own needs and offer a starting point for writing your own training program.
All training plans should cover three main areas: specifics of the employer’s energy control program, each employee’s specific duties and assignments in regards to LOTO safety, and an overview of OSHA standards related to lockout/tagout procedures.
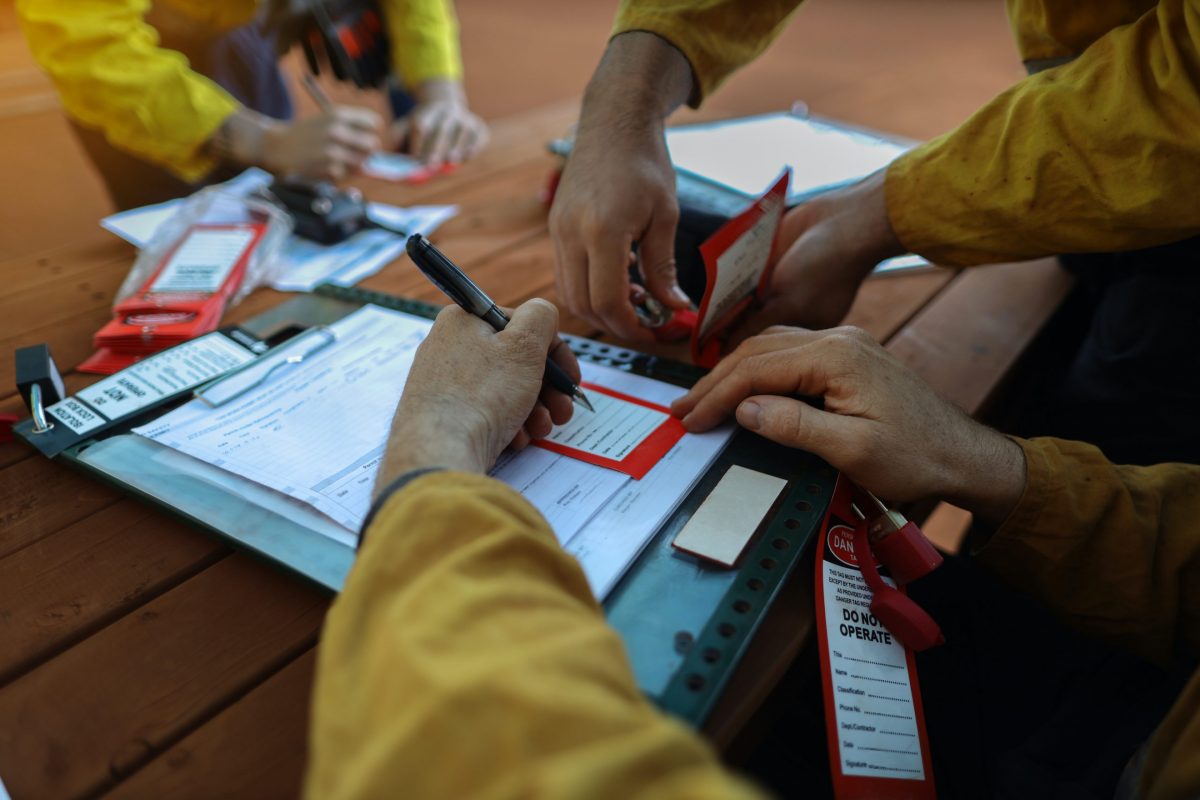
Training Components
Each time a new employee joins the team, the company should provide the required LOTO training for that employee. Every authorized employee must have a “certificate” from the employer that includes their name and the dates they underwent training.
Retraining
Retraining should be done anytime a new employee is assigned to an area or machinery with LOTO procedures, any time the machinery or equipment shows a new hazard, and anytime the energy-control procedures change.
All employees should be retrained if an inspection reveals a lack in understanding your LOTO procedures.
Types of Training
LOTO training generally falls under three categories—authorized, affected, and other. These categories describe the different levels of responsibility an employee may have in relation to LOTO.
Authorized employees are those workers with the responsibility for physically performing the LOTO duties. These employees are the only ones authorized to start LOTO procedures and remove the LOTO equipment.
Affected employees are those who operate the machinery or are in the direct area where the machinery is located. Any employees who work or will be present in an area where energy-control procedures are in process fall under the other category.
Authorized employees must receive training that allows them to recognize hazardous energy sources, the types and magnitudes of hazardous energy sources, and ways to isolate each type of hazardous energy. Training for affected employees should include information on the recognition of LOTO devices, and the purpose and use of energy control procedures.
All other workers should receive training that allows them to identify locked out equipment in their workplace and understand the importance of LOTO procedures. An employer must make sure that every employee knows how dangerous not adhering to LOTO procedures can be to themselves, other workers, and the workplace.
In addition, every employer must have procedures for working with contractors who may need to interact with company equipment. Company personnel must know if contractors are using their own LOTO equipment or working with Authorized employees from the company to perform the LOTO.
Tagout Training
In some instances, a company uses tagout procedures instead of lockout. When this is the case, employees should receive additional training that addresses the limitations of tagout compared to lockout. Tagout training should cover:
- Reinforcing that tags are only warning devices and do not offer the restraint of a lock
- Tags must be legible and in a language understood by all employees
- Tags must be able to withstand any and all harsh conditions of that workplace, including heat, cold, wind, weather, etc.
- Tags must be securely attached and not able to be removed accidentally
- Only the person who attached the tag has the authority to remove it
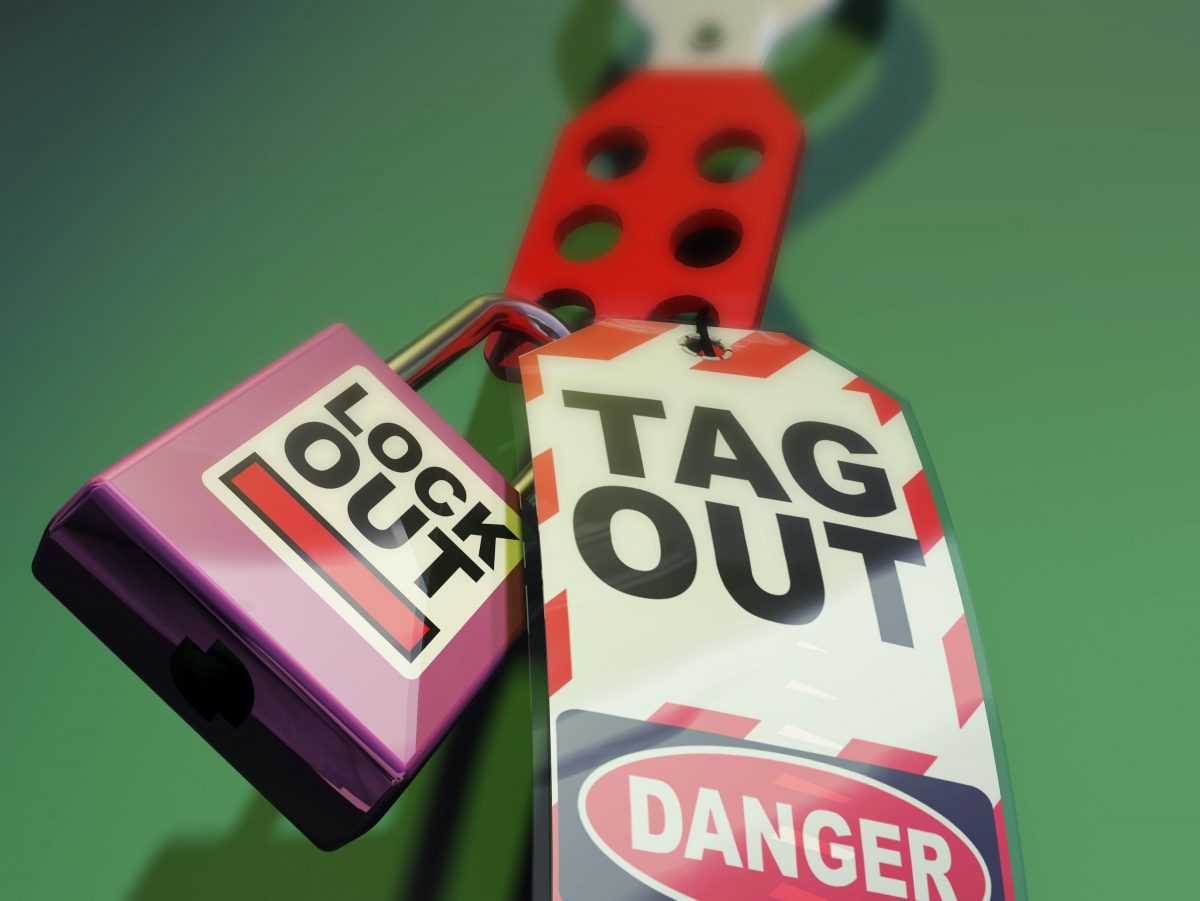
ANSI Training Standards for LOTO
Along with OSHA standards, which are mandatory for companies to follow, many companies choose to follow voluntary standards. Standard development organizations across the country create these standards that companies can choose to follow.
The American National Standards Institute (ANSI) plays a large role in standards development as well, by accrediting the SDOs that create standards. ANSI also develops and lays out the requirements SDOs follow when creating standards.
Working in conjunction with the American Society of Safety Professionals, ANSI offers a standard for lockout/tagout safety. The Lockout, Tagout, and Alternative Methods Standard (ANSI/ASSP Z244.1) includes requirements for controlling hazardous energy using lockout/tagout and alternative methods. The standard covers:
- Three LOTO methods
- What activities require LOTO such as installing, repairing, inspecting, etc.
- LOTO responsibilities
- Machinery/equipment design for control of hazardous energy
- Creating a hazardous energy control program
- Control of hazardous energy
- Alternative methods of hazardous energy
Companies can purchase the ANSI/ASSP Z244.1 standard on the ASSP website. The standard is discounted for ASSP or ANSI members. Even though this standard is voluntary, it is an excellent resource for implementing LOTO training and adding an additional layer of protection for workers.
Other Best Practices
Going beyond an effective lockout/tagout plan and training program, certain best practices can add that extra assurance that LOTO will be successful.
Engagement
Keeping employees engaged can make a huge difference in LOTO procedures and training. While the authorized workers have defined responsibilities in LOTO procedures and training, EHS Today recommends assigning additional LOTO mentors. These mentors oversee one or more machines, providing assistance when needed, answering questions, and acting as a resource.
Keep LOTO Gear Handy
While it seems simplistic, employers should keep LOTO gear and devices near the machines they are used on. Having the right equipment at hand, organized, and ready to use saves workers time. During training, teach employers how to keep LOTO devices organized and ready to use.
Inspect Regularly
Again, this seems like a no-brainer, but regular inspections of machinery and equipment and the LOTO devices that guard them can prevent loss of life and income. OSHA recommends yearly inspections, but performing inspections more regularly can find problems before they become problems. Regular inspections also can also provide additional training touchpoints for employees.
Tighten Up LOTO Training
Where LOTO training is concerned, it’s usually not a matter of convincing employees to do it your way. They already want to be kept safe from the dangers of hazardous energy.
Focus your efforts on improving training clarity, relevance, and documentation. Include plenty of opportunities for participation during training and provide feedback in realtime.
Finally, use LOTO training as a way to boost your entire safety management system. Run audits, hold safety meetings, and track your training with an app like Safesite, so you can get out of the office and back onto the floor.