Forklift training management is challenging. Because each operator must demonstrate their knowledge before they start work (and at least once every three years), you must ensure that trainers are effective, workers are competent, and training is scheduled so that work continues seamlessly.
The neverending cycle can make you feel like you’re always playing catchup. This guide will help you focus in on the true north — the most important things — when it comes to your sit-down counterbalance and stand-up forklift training program.
The Benefits of Effective Forklift Training
Powered Industrial Truck (PIT) training is required by OSHA and many other regulatory bodies around the world. Effective training is ground zero for maintaining worker safety. OSHA regulations have been in place for years and yet over 20,000 forklift accidents and 100 deaths still occur each year.
The benefits of maintaining a healthy training program include compliance with your local and national regulations, workplace safety, cost reduction, efficiency, lower turnover, and a better safety culture overall.
Compliance with the OSHA Forklift Training Standard
The OSHA (Occupational Safety and Health Administration) is the regulatory body in charge of ensuring safety practices among US businesses. To comply with OSHA’s safety regulations, forklift operators must meet certain qualifications and standards.
The Federal OSHA requirements for drivers of powered industrial trucks may be found in CFR 29 1910.178, 1926.602, and 1915.20. Your OSHA-approved state plan may have more stringent requirements, but the federal guidelines can be summed up as follows:
- Drivers must undergo complete training and become certified by the employer before being allowed to operate the forklift.
- To obtain a certification, the operator must be evaluated by her employer and found to be competent.
- After this, an evaluation of the operator’s performance must be conducted at least once every 3 years.
- Drivers assigned to drive a new type of truck or who have been in accidents or near misses must undergo refresher training courses.
The US Department of Labor is serious about minimizing accidents in the workplace. This is why forklift training and certifications are mandatory. All businesses that use powered industrial trucks should train their workers in order to comply with the OSHA.
The National Safety Council (NSC) provides a one-day forklift training course that is fully compliant with OSHA regulations. The training can be done at the NSC training center or at the business’s work location. Certificates of completion are then awarded to those who successfully finish the course.
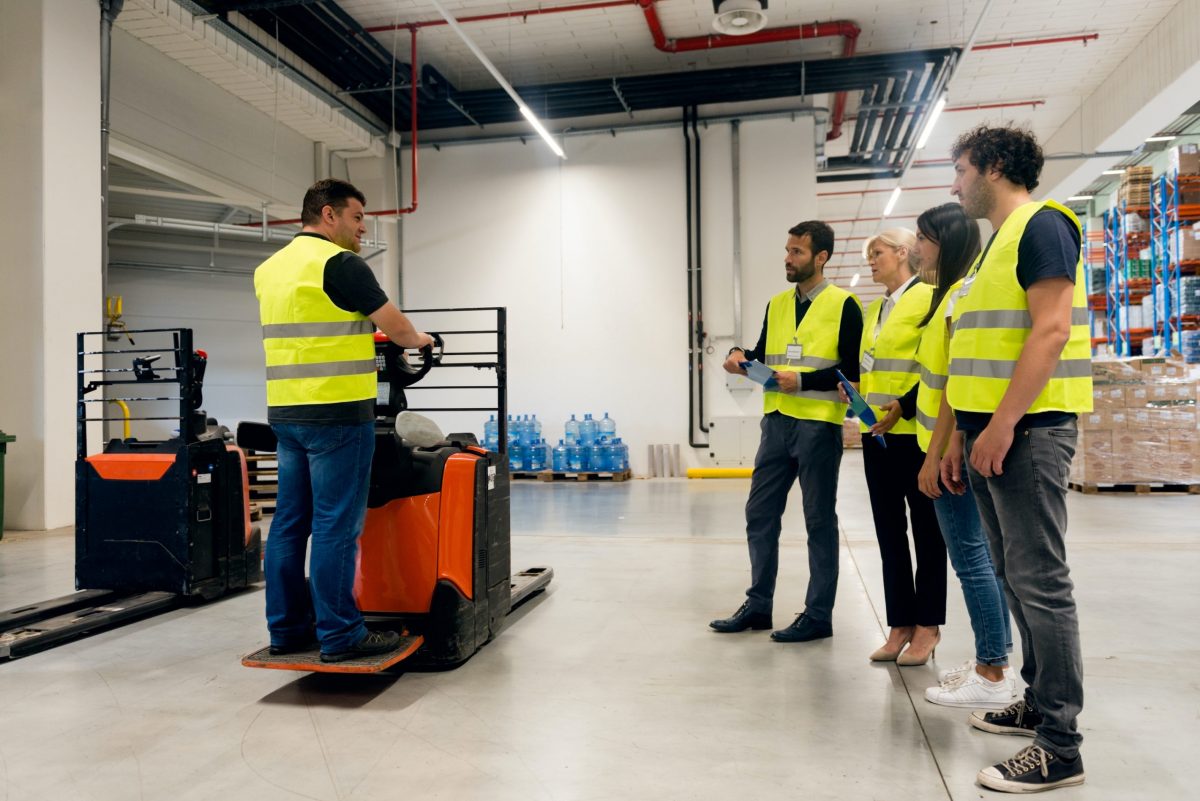
Workplace Safety
As much as employers must certify forklift drivers for compliance purposes, that’s not the only reason to run a good training program.
Providing effective forklift training to drivers and pedestrians (those who work around forklifts) will generally lead to a safer workplace. It will also lessen the risks of incurring property damage that leads to more accidents. This is advantageous for employers who simply want to focus on making their business grow.
Accidents take a toll on staff and company assets. Therefore, they should be prevented at all costs with proper training.
Increased Life Of The Equipment
Forklifts that have been used improperly for long stretches of time can have shorter life spans. Powered industrial trucks that undergo heavy wear and tear have a greater danger of malfunctioning. This could lead to potential accidents long before the expected end of life for the equipment.
Cost Reduction
Forklift injuries come at a high price. Some costs directly arise from the injuries themselves, while others are incurred due to conditions resulting from the injury (indirect costs).
- Examples of direct costs are compensation for injured workers, medical expenses, and legal costs if necessary.
- Indirect costs include repair/replacement of damaged equipment, OSHA penalties, temporary staffing changes during employee absence, and damage to the company reputation and resulting loss of sales.
With a good training program, you can steer clear of such costs and increase your bottom line.
More Efficient Operations
Properly trained forklift drivers tend to perform more productively. Unsafe conditions are minimized because materials are not being dropped in workspaces. Other workers feel more confident to move around the work area. Just having the assurance that the forklift driver is properly trained can boost overall morale among employees.
Less Workforce Turnover
The most common-sense way to decrease workforce turnover is to lower the incidence of accidents. If forklift operators keep getting injured permanently, the company will be on a constant search for relievers and replacements. This is time-consuming and draining for employers and leads to low morale in employees.
Frequent staff turnover can be a headache for any business. New workers need to be oriented again with the job description and workplace rules. Meanwhile, during the search for new workers, forklifts may be left unmanned and unable to contribute to production.
This problem can be avoided by getting the proper forklift training right the first time. The longer an operator stays at his job, the lesser need for the company to start from scratch with new hires.
Enhances Company Reputation
Having a safer workplace can enhance company reputation. In the long run, employees will have higher job satisfaction because they know that management cares for their safety.
On the other hand, if a company is known for accidents and injuries, it will reflect badly on management. This could lead employees, clients and even regulatory bodies to view the company in a negative light.
Because of its weight, speed, and limited maneuverability, the forklift is one of the most dangerous vehicles to use. It could cause permanent disabilities and even death. Therefore, a company that’s serious about implementing safety standards should emphasize forklift truck training for its operators.
It’s always better to try to prevent mishaps than do damage control later. A good safety training program is like nipping future nasty accidents in the bud.
It’s the Right Thing to Do
Of course, many employers and safety managers like you prioritize safety training simply because it’s the right thing to do. You can never go wrong by protecting your employees as you would yourself.
Forklift License vs. Certification
Some online sources tout a forklift driver’s license. There is no such thing. The only operating license needed by the OSHA is a documented record, or certification, from the employer stating that:
- the driver has completed forklift training (with the date and provider of training)
- the driver has passed their evaluation successfully (with the date and name of person evaluating the driver)
In fact, OSHA does not even require forklift operators to have a valid driver’s license.
Companies that use the term “license” with regard to employee forklift training are likely using it interchangeably with “certification,” as a way to clarify that forklift operators have the qualifications and permission to drive powered industrial trucks.
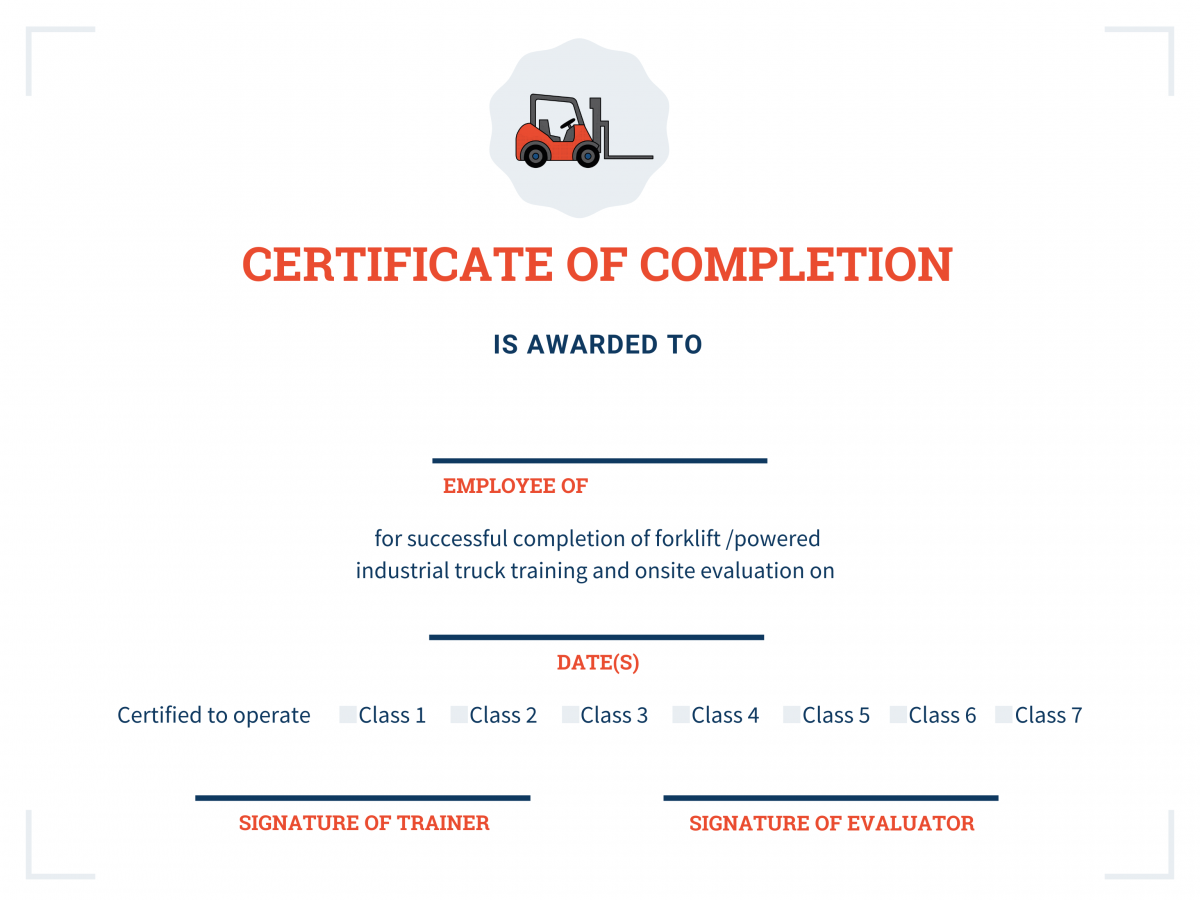
Getting Forklift Certified During a Job Hunt
Some job seekers want to show they have forklift skills when seeking a new job or re-entering the workforce after an absence. They can seek training through an organization that provides heavy equipment training, such as the National Safety Council.
While third-party providers like the NSC provide certificates of completion to its course takers, employers must ultimately evaluate and certify every employee who is to operate a lift truck at work.
While third-party certifications can be attached to the employer’s documented record or kept by the forklift driver as proof of finishing the training, there must be documentation of an operator’s competency that is updated every three years.
Aspects of a Good Training Program
Your forklift training program shouldn’t be treated as a mere formality. To reap the benefits, aspiring operators should receive comprehensive training that covers all the important aspects of forklift safety.
Forklift training should result in a demonstrated ability to operate powered industrial trucks safely. If not, drivers will get certified but won’t get the full knowledge they need.
Here’s what to include in your training program:
How To Avoid The Primary Causes of Forklift Deaths
Sure, everyone keeps on saying that operating the forklift is “dangerous;” however, a good training program doesn’t just allude to the risks, it identifies the main causes of accidents related to powered industrial trucks.
According to the National Traumatic Occupational Fatalities (NTOF) surveillance system, there are four types of incidents that lead to forklift mishaps:
The forklift overturns. This represents 22% of related deaths. Loss of forklift control could cause the vehicle to overturn and smash objects nearby. The main cause of this is a lack of familiarity with how the vehicle works.
A nearby worker is hit by the forklift’s moving parts. In 20% of forklift accidents, the driver’s life is spared, but an unlucky nearby worker gets hit fatally by the moving parts of the vehicle or its load.
The driver or a nearby worker gets crushed by the forklift. This is, by far, one of the most brutal ways to perish from a powered industrial truck mishap. The reality though, is that it happens in 16% of all forklift-related deaths.
A person falls from the forklift. This is the cause of 9% of all forklift fatalities.
By helping trainees identify the main causes of forklift injury and death, steps can be taken to prevent these conditions from happening. Your training program should then focus on showing trainees how to take precautions in order to avoid the top 4 causes of forklift deaths.
The Principles Of Physics That Empower The Forklift
While there’s no need for a physics class, a good training program should orient trainees on the basic principles that allow the forklift to lift heavy materials and loads. All employees should understand the weight of the forklift truck and how it affects its ability to slow down and stop.
Operators should understand the significance of the hydraulic and pulley system, the mechanisms that power the forklift, and the tipping risks involved with overloading the fork. They must also understand the stability triangle of forklifts and how the center of gravity impacts the handling characteristics of the forklift.
An understanding of the physical laws that govern the operation of the equipment will significantly reduce risk of personal injury.
How A Forklift Operates
The bulk of the entire training program should focus on teaching trainees how the forklift operates. It might seem “easy”, but it’s trickier than it seems. There are various types of forklifts. This means, there is no one-size-fits-all kind of training that teaches how to operate a specific brand or truck model.
A good training program discusses the important functionalities of the specific forklift that the worker will use. This can be done instead of showing general instructions on how to operate all kinds of forklift brands.
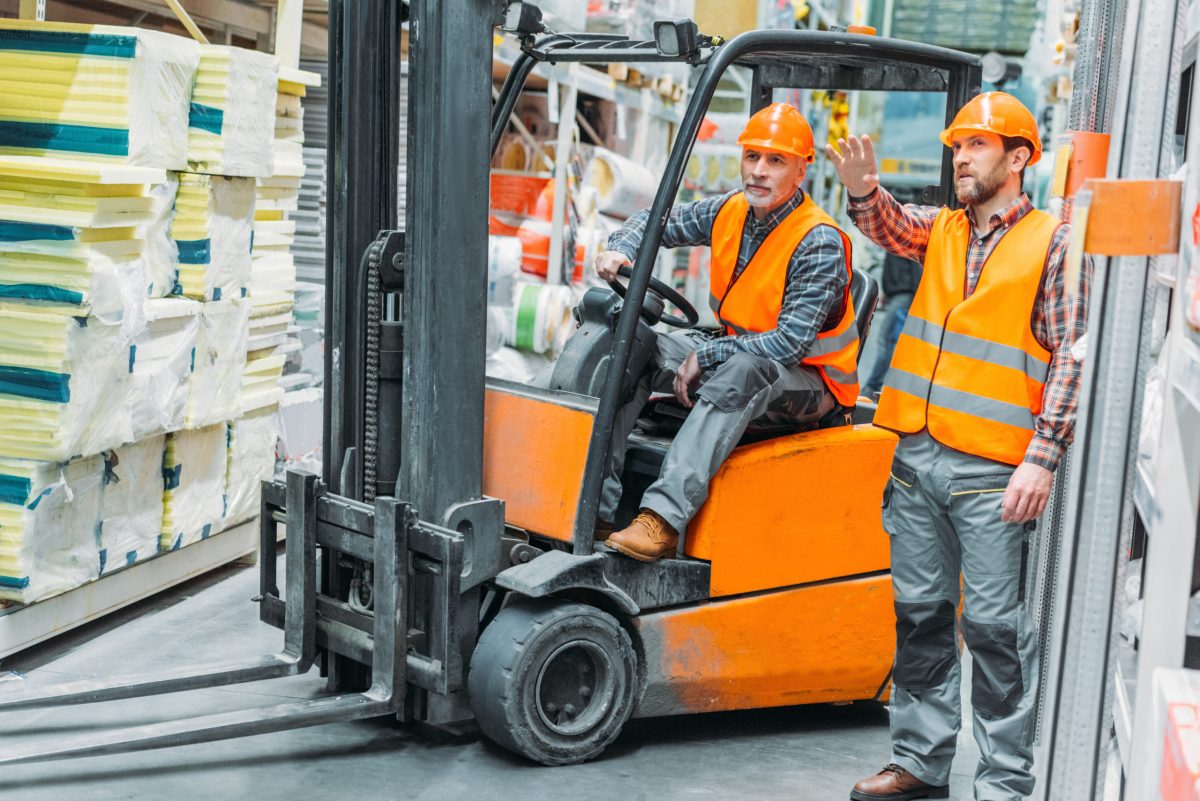
Here are some of the basic skills your training program must cover:
Pre-Shift Forklift Inspections
Forklifts must be inspected before each shift. Teach your employees to use your forklift inspection log to run a:
- Visual check of all operational components, including lights, tires, hoses, mirrors, fluid levels, filters, and fork and mast condition.
- Operational check to ensure proper working controls and functions.
Instruct your employees to document their pre-shift inspections and to immediately remove questionable forklifts from service. Your employees should understand the dangers of operating a faulty PIT and/or not labeling the forklift correctly if removed from service.
How To Move With and Without a Load
Trainees should be taught how to drive a forklift when carrying heavy loads. A powered industrial truck is in greater danger to cause accidents when it is moving with a heavy object. If the bulky load drops, property can be damaged, or lives can be lost. Moreover, if the driver doesn’t know how to move with a heavy load, the forklift may lose its balance and smash nearby objects and people.
On the other hand, drivers should also be oriented on how to move without a load. Driving the forklift too fast or turning too rapidly can present a lot of hazards. Therefore, best practices should be communicated to trainees, so they are able to prevent those hazards in the future.
How To Approach, Pick Up, and Stack A Load
The OSHA has recommended best practices on how to approach, pick up and stack heavy loads into the forklift. To summarize, here are the basic guidelines for approaching and picking up loads:
- Approach the load slowly and with caution
- Ensure the forklift is at a full stop and brakes are set
- Check if there is enough overhead clearance before picking up and lifting the load
- Make sure the vehicle is in the proper position
- Put the fork into proper position
- Pick up the load by adjusting the forks to distribute weight evenly
- Lift the load carefully and slowly
- Ensure the load is secure before moving
Of course, there are more specific instructions and practices needed to be learned in order to properly implement the above. The ideal training program should cover all the required steps outlined by the OSHA for full compliance.
Powered Truck Operation Under Special Considerations
Aside from the usual movements, lifting, lowering, loading and unloading, there are other special considerations that a forklift driver must be familiar with:
Working With Trailers. Drivers should be trained on how to load and unload trailer trucks using a forklift. There are many safety considerations when using powered industrial vehicles for trailer loading and unloading. A good training program should cover the best practices as well as the most common hazards that must be avoided.
Driving Across Ramps. Drivers should understand how to operate forklifts across ramps or elevated surfaces. The OSHA has specific requirements and measurements for dock ramps that can be used for forklift operation.
A safe distance must then be maintained from the forklift to the edge of the ramps. Ramps should also be ascended or descended slowly with the load facing uphill while the forklift is loaded and counterbalance facing uphill while unloaded.
There are other OSHA guidelines that govern the use of forklifts across ramps. For example, driving in reverse when going up on a ramp incline is recommended for forklifts without a load. This and many other compliance guidelines must be discussed in a forklift safety course or certification program.
Using The Elevator. A good forklift training program also shows how to use a powered industrial truck with elevators. Checking the overhead clearance and weight capacity of the elevator is mandatory. Safety precautions must be performed to avoid floor damage, overloading, and elevator accidents.
Forklift Training Mistakes
Whether you’re managing your training program in-house or selecting a third-party provider, aim for effective training that prioritizes active participation. You’ll want to avoid the most common forklift training mistakes.
Mistake #1: Lack Of Practical Application
One of the cardinal “sins” of forklift training is giving trainees a lot of lecture-type studies without any practical application.
While lectures can be an effective way to introduce powered industrial truck safety, the best way to learn is through discussion and activity. If trainees can’t practice, they can’t really learn.
The forklift training program by the NSC (National Safety Council) is a one-day training session. It is mostly done in a non-lecture setting and provides a more practical approach.
A mix of classroom learning and practical application works best for most adult learners. In fact, the OSHA requires that companies document both the formal instruction (classroom learning) and practical performance evaluation of their operators.
Mistake #2: Using Training Material With Outdated or Incorrect Info
Training providers must be able to supply materials that are free of mistakes or outdated info. OSHA, ANSI, and forklift manufacturers continually update their guidelines. Because of this, a forklift training provider should consistently update course info and materials to reflect current best practices.
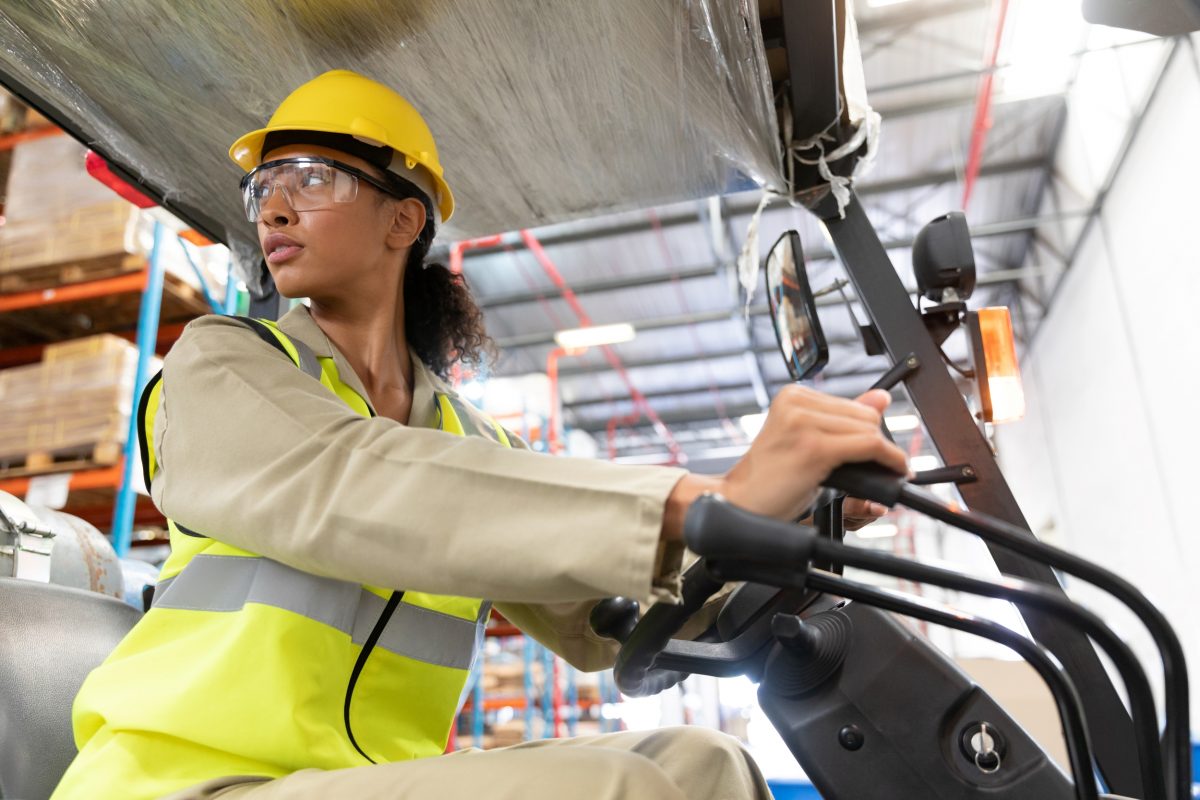
Mistake #3: Training That’s Too Broad
Familiarizing trainees with only the broad basics of operating forklifts is a big mistake. While it’s understandable to want your operators to have a solid grasp on PIT basics, you must include the specific forklift classes/types and activities each driver will be responsible for in the workplace.
This doesn’t mean, however, that trainers should overwhelm their trainees with loads of information. Trying to learn skills that don’t apply within a short time isn’t good for retention.
The solution is to ensure that there is at least some amount of personalization in your training program. For example, you may wish to focus on the basics at the start of your training and then break your trainees up into groups to learn specialized skills.
When it comes to forklift competency, there are no shortcuts. Operators should be taught everything they need to know before handling a powered industrial truck.
Mistake #4: Assuming That Trainees Already Know
This mistake applies to in-house training programs more often than third-party programs. Some trainees in your company will already show signs of familiarity with how a forklift operates. In some cases, they have already been certified operators in the previous companies they worked with.
However, it is a mistake to assume that they already know everything they need to know. Allowing them to simply skim through the material or skip important parts can lead to a near miss or accident.
According to OSHA guidelines, a powered industrial truck (PIT) certification from previous employment is not transferable to another job. This means, if an operator has been certified before in ABC Company, he needs to be certified again at XYZ Company.
Companies are required by the OSHA to develop their own unique PIT Written Program. This written program contains forklift usage guidelines that specifically fit the needs of the company. Therefore, no two forklift training programs are the same. Each is unique and tailor-made to an organization.
This is why employees with previous PIT certifications must be retrained and certified in a new employment setting.
Mistake #5: Using Trainers Who Lack Relevant Firsthand Knowledge
According to OSHA, trainers must have the “knowledge, training, and experience” to train operators and evaluate driver competence. What some companies overlook, however, is ensuring the trainer is knowledgeable in the specific skills required for their operational environments.
These specific skills include but aren’t limited to the type of forklifts in-use, the overall environment/traffic-level, and the types of hazards present at your company.
If only your long-time employees possess that firsthand knowledge, then hiring a third-party trainer probably isn’t enough (unless the training vendor is willing to work with long-time workers to become familiar with operational conditions)
Another good option is to develop an in-house training program. Workers who have extensive experience with the company operations and PIT equipment can be groomed as forklift trainers.
Let’s discuss the benefits of an in-house training program below.
In-House Forklift Training Programs
In-house training generally means that the forklift training sessions will be done in one’s place of business instead of sending employees to a third-party location.
Of course, this definition has evolved as well. It’s no longer just a question of where the training is going to be held, but who will facilitate the sessions.
Many employers are beginning to realize the advantages of “training their own trainers” so that forklift safety programs can be handled by internal personnel. Here are some of the benefits of going the in-house route:
Advantages of In-House PIT Certification Training
The training will be facilitated by people who work within the company. They are skilled and experienced with the company’s operational environment, specific equipment, and work processes. This firsthand knowledge gives them an edge over third-party trainers.
Lesser costs in the long term. Although a company still needs to spend money on training resources, you’ll save a lot of money on third-party trainer fees. An experienced worker can simply facilitate forklift training as part of his or her job, or for a small additional compensation. Also, instead of sending employees to a third-party training location and paying repeatedly, in-house training resources can be bought for just a one time fee.
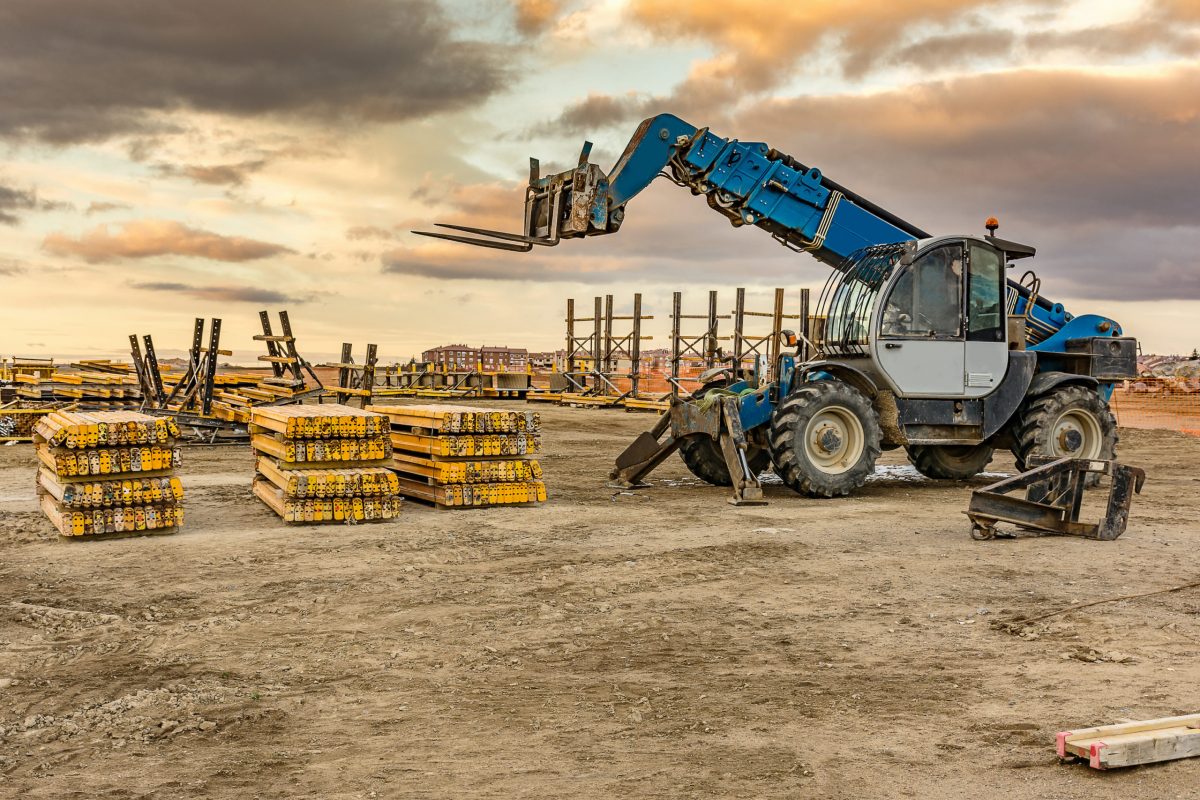
In-house trainers are readily available. Instead of inviting a third-party trainer to come over each time there’s a new hire, in-house trainers are already on hand when you need them. This saves the company precious time, especially if the goal is to start the new worker on the forklift immediately. Plus, in-house trainers are able to follow up, observe, and reinforce safe work practices long after the certification has been given.
Equipping Your Trainers (Free and Paid Resources)
Not every Tom, Dick and Harry in your company can perform forklift operator training. According to OSHA safety training guidelines, in-house training must be provided in a manner employees understand and result in a demonstrable understanding of the topic.
Those who will handle the powered industrial truck training within a firm must be adept at operating forklifts themselves. On top of this, they need to be able to train effectively and be knowledgable on OSHA PIT guidelines for your industry.
This highlights the importance of acquiring the right training resources for your in-house forklift safety program. There are various resources out there that are OSHA compliant and will help equip your trainers.
Free resource providers include:
Forklift Academy – They provide free resources that can be used by trainers in an in-house forklift safety program. Daily inspection checklists, forklift safety rules, and forklift certification tests can be downloaded from their site.
Business and Legal Resources (BLR) – The BLR website has lots of forklift training resources, including training tips, handouts, quizzes, speaker notes, power points, and supporting audio/video clips. The resources themselves are free for all subscribers of the BLR website (subscription is also free).
Below are some paid programs and resources that will help equip your trainers:
American Training Resources – They provide a 4-part video training that can be used for operator certification (OSHA compliant). It also comes with an instructor’s guidebook, trainee’s guidebook and training certificate template. The cost for the resource is only $495.
Certifyme.net – this a web-based training platform that provides forklift safety training. They also have a “train the trainer” certification for those who prefer forklift certifications to be done internally. The cost is only $149 per trainer.
NSC University – The National Safety Council conducts a train-the-trainer program that only costs $425 (for members) and $555 for non-members.
The resources found in the above examples can benefit both trainers and trainees. Incorporating useful resources in your in-house forklift training program can do wonders for your firm.
To handle in-house or outsource forklift training? In-house training costs less and saves time in the long-term. Third-party training lessens the burden to keep up-to-date training materials. A combination of third-party and in-house provides your operators with general safety skills and practical application in your working environment.
Remember: you are still required to document your operator certifications and stay on top of re-certification every three years.
Third-Party Training Programs
Although in-house training programs have their advantages, there are situations when they are not the best option for an employer.
For example, an in-house training program makes little sense if a company doesn’t require ongoing use of the forklift. If a powered industrial truck is only needed occasionally by one or two workers, choosing a third-party forklift training program is a better option.
Some employers do not like the trouble of equipping their workers to become trainers. They want their workers to focus on their jobs and not worry about training newcomers. In these situations, sending employees to a third-party training program would allow employers to outsource the training somewhere else.
If you work with a third-party trainer, you may have less flexibility when it comes to scheduling. Plan ahead for new employees and emergency needs. Track your certification expirations with a spreadsheet or with an app that will alert you when an employee is up for re-certification.
Choosing A Third-Party Trainer
The main thing to keep in mind when choosing a third-party forklift training provider is this: full compliance with the OSHA guidelines.
While it is easy to claim that the course being sold is “OSHA compliant,” more verification is needed. Request a course overview from the provider and make sure it follows the OSHA requirements for training program content.
The OSHA has a complete list of specific topics that need to be covered within a forklift training program. Essentially, a true OSHA compliant forklift course will include the following:
- Truck-related topics such as operating instructions, steering, maneuvering, vehicle capacity, vehicle stability, refueling, etc.
- Workplace-related topics such as surface conditions, load manipulation, load stacking and unstacking, how to navigate hazardous locations, ramps and slopes, etc.
- Refresher training and evaluation content
- Proper certification format (as required by the OSHA)
Remember: OSHA compliant training programs don’t always guarantee sufficient training for your unique work situation. Talk to each vendor to see whether there will be gaps after training and how you, as the certifying employer, can fill them.
Training Providers And Cost
It may be helpful to compare a few leading forklift training providers side-by-side. Here’s a sample comparison chart below using a few leading national providers. We suggest comparing local/regional providers who can provide in-person training as well.
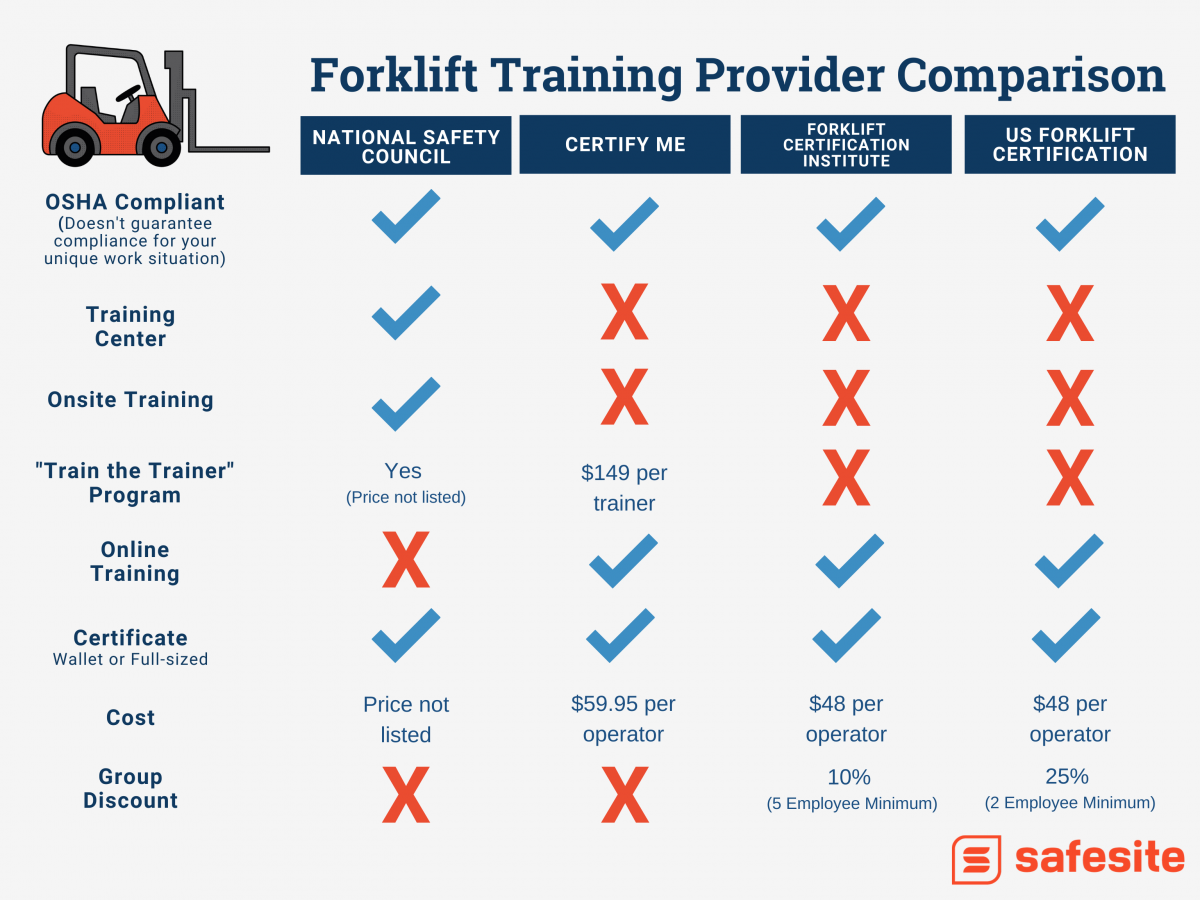
National Safety Council. The NSC is one of the most reliable providers of third-party forklift training. Their program is fully compliant and updated with OSHA guidelines and can be done in their training center or onsite. However, the costs are not mentioned on their website.
CertifyMe. The forklift certification training from CertifyMe costs $59.95 per operator (as mentioned earlier, they also have a program for those who want to be trainers). The training here is web-based.
Forklift Certification Institute. This website also offers OSHA compliant training content and is fully web-based (can be taken online). They allow students to take unlimited practice exams without any additional fees. They also provide a free forklift operator training manual. The cost for individual training is $48, but discounts apply for group purchases.
US Forklift Certification. This provider asserts that their forklift certification applies to the US, Canada, and Mexico. They offer on-the-go training that can be taken via smartphones. Forklift certificates are sent digitally and can be printed by the student upon completion of the course. Their platinum-level course costs $48.
The True North for Improving Forklift Training
The key to maintaining a great forklift training program is integrating it into your overall health and safety system. When the safety of your staff is your true north, it’s easier to trash the activities that don’t truly benefit your company.
Successful safety programs follow-up on forklift training with 1) observations (good or bad), 2) hazard recognition and resolution, 3) inspections, 4) near miss reporting, and 5) certification tracking. These tasks help to ensure your training is effective and repeatable.
When deciding between in-house or third-party forklift trainers, the most important factors to consider are the practical needs of your organization and your employees.
In summary, the investment that goes into quality training programs will pay off in the long term. The elimination of forklift accidents from your workplace is well worth the price of training.