Even though OSHA is the agency that many love to hate, there are many benefits to complying with OSHA standards for workplace health and safety.
From insurance and workers’ compensation cost reductions to employee satisfaction and retention, a safe workplace has a competitive advantage.
Want to download this article and read it later? Get the PDF straight to your device.
About This Guide
All employers would agree that the workplace should be safe for their employees. The Occupational Safety and Health Administration (OSHA) takes that sentiment and translates it into concrete, actionable standards that are enforceable by law.
Below, you’ll find a comprehensive guide to aligning your workplace with OSHA standards. Whether you’re new to management or a seasoned business owner, use this guide as a digest of the information on osha.gov.
Who Has to Comply With OSHA?
OSHA was set up to keep employees in the US as safe and healthy as possible. So, the simple answer is that any business or organization that employs workers should be compliant with OSHA’s guidelines for the sake of their employees.
Who is Covered by OSHA?
The OSH Act covers most private employers and the people who work for them, along with some public sector employees throughout all 50 states and federal territories, including: District of Columbia, Puerto Rico, the Virgin Islands, American Samoa, Guam, Northern Mariana Islands, Wake Island, Johnston Island, and the Outer Continental Shelf Lands.
It either covers employees directly through the federal OSHA program or it covers them indirectly through state-run programs that OSHA helps fund and oversee. In some states, the coverage of private and public sector employees is split between federal OSHA and the state-run program. Regardless of how coverage is split, most private and public sector employees have coverage and OSHA is the final authority on workplace health and safety standards in the US.
The following states and territories have their own state-run workplace health and safety programs overseen by OSHA: Alaska, Arizona, California, Hawaii, Indiana, Iowa, Kentucky, Maryland, Michigan, Minnesota, Nevada, New Mexico, North Carolina, Oregon, Puerto Rico, South Carolina, Tennessee, Utah, Vermont, Virginia, Washington, and Wyoming.
Is OSHA Compliance Mandatory?
Yes. If an employer is covered by OSHA, they must be in compliance with federal OSHA or the state-run program, which must be at least as effective as the federal program.
Who is Exempt?
According to OSHA, the agency does not cover: Self-employed people Immediate family members of farm employers Workplace hazards that fall under a different federal agency (the Mine Safety and Health Administration, the Coast Guard or the Department of Energy, for example)
What Does OSHA Compliance Require?
Since virtually every employer needs to be compliant with OSHA standards and regulations, it’s crucial to know exactly what being compliant means. To put it as simply as possible, being OSHA compliant means following the rules of the agency. Let’s take a look at what those rules entail.
Rights & Responsibilities of Employers
Any employer who is covered by OSHA has a duty to create a safe working environment free of recognized hazards and to follow all the OSHA health and safety standards that apply. Employers must identify and fix any health and safety hazards by making possible physical or engineering changes to working conditions before simply relying on personal protective equipment (PPE) like masks and gloves, etc. to deal with a hazard.
For example, if there is a hazardous situation where harmful fumes are posing a risk to workers, the employer would have to try something like switching to safer chemicals, improving ventilation or trying to keep fumes away from workers before simply stating that workers have to wear a certain type of air-purifying mask to address the hazard.
Employers must try to address the hazard in a way that improves the working conditions rather than just mandating protective equipment, rules, or warning signs as a solution.
In addition, employers must also:
- Display the official OSHA Job Safety and Health: It’s the Law poster on-premises.
- Inform employees of chemical hazards via training, labels, alarms, color-coded systems, information sheets, and other methods.
- Provide safety training to employees in a language they can understand.
- Keep accurate records of all workplace injuries and illnesses.
- Conduct required exposure testing in the workplace (air or noise sampling, for example).
- Provide required PPE to employees at no cost to the employees.
- Provide hearing exams and other medical testing for employees that OSHA regulations require.
- Post any OSHA citations and injury and illness data where employees can easily see them.
- Notify OSHA (by calling 1-800-321-OSHA [6742]) within 8 hours of a workplace fatality or 24 hours of a workplace injury resulting in inpatient hospitalization, amputation or loss of an eye.
- Refrain from retaliating against employees who use their rights under the law, including their right to report a workplace injury or illness.
Under OSHA law, employees are entitled to work in a workplace that does not pose a risk of serious harm.
Rights & Responsibilities of Employees
Employees have certain rights they can exercise to help maintain a safe workplace. These include:
- The right to file a complaint with OSHA and request an inspection of their workplace.
- Receive training in a language they understand about the hazards specific to their workplace and how to lessen or eliminate these hazards.
- Receive copies of records about injuries and illnesses in their workplace.
- Receive copies of records of environmental tests done at their workplace.
- Receive copies of their workplace health records.
- Participate in an OSHA inspection and speak with the inspector privately. File a complaint with OSHA if any of their rights have been infringed upon and if an employer has retaliated against them for requesting an inspection.
- File a whistleblower complaint if they’ve been retaliated against for making a safety complaint.
OSHA Standards
OSHA standards are proven guidelines for providing a safe, hazard-free workplace. provide a safe, hazard-free workplace. Always posted for free on the OSHA website under Laws and Regulations, the standards may also be found as printable (.PDF) summaries, or digests, on the Publications page.
- General Industry (Digest available as an English .PDF and Spanish .PDF)
- Construction (Digest available as an English .PDF and Spanish .PDF)
- Maritime (Multiple .PDF Fact Sheets and QuickCards are available)
- Agriculture (Multiple .PDF Fact Sheets and QuickCards are available)
- Recordkeeping (Overview .PDF)
- Whistleblower (Available as an English .PDF and Spanish .PDF)
Laws, Regulations, and Interpretations Overview
Laws in the context of OSHA refer to the Occupational Safety and Health Act, which became law in 1970 and which created OSHA, and the laws contained within that act, which all pertain to occupational health and safety.
OSHA regulations (or standards) are the regulatory requirements OSHA has developed to serve as criteria to test whether employers are adhering to the laws in the OSH Act.
Interpretations are letters and memos written by OSHA in response to inquiries from actual employers about aspects of OSHA regulations, including enforcement. They are meant as a way to guide people when complying with OSHA regulations, but they cannot establish or revise an OSHA policy.
OSHA standards are covered under six broad categories:
- General Industry
- Construction
- Maritime (parts 1915, 1917, 1918)
- Agriculture
- Recordkeeping
- Whistleblower (contained in the statutes)
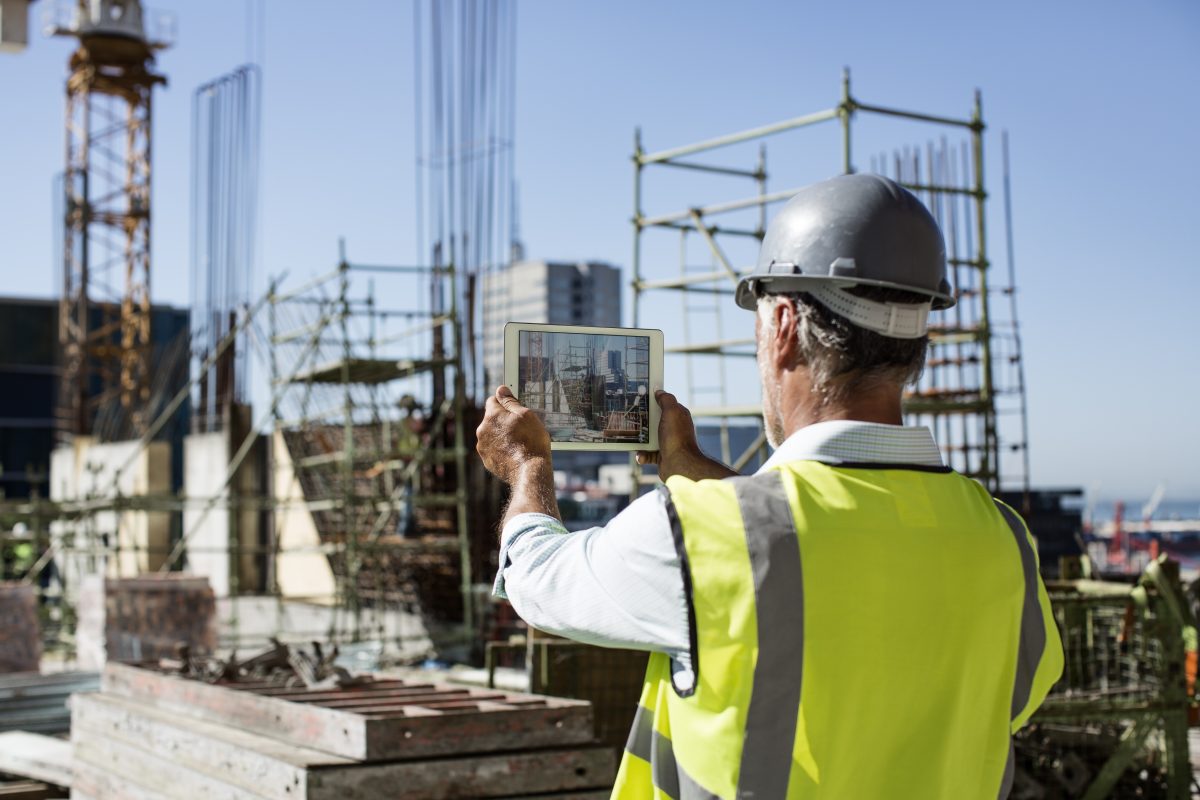
General Industry Vs. Specific Industry Standards
OSHA General Industry Standards (1910) apply to every organization covered by OSHA. You must learn and abide by the standards that apply to your company and working conditions. OSHA will not hold you accountable to a standard that doesn’t apply. Call your local OSHA office or consult your Safesite success coach for help identifying which standards apply to your company. If you work in one of the 22 states with an OSHA mandated State program, state-specific regulations may apply.
In addition to being bound by general industry rules, construction, maritime, and agricultural operations have an industry-specific set of standards.
You can find all OSHA Law and Regulations on the OSHA website or you can download and print them.
What are the OSHA Personal Protective Equipment (PPE) standards?
OSHA PPE standards are the sets of regulations that deal specifically with PPE. These standards are found throughout the general industry and construction standards — they don’t have one dedicated section. However, OSHA provides a PPE Booklet that you can download and reference as needed.
Briefly, employers are responsible for the following when it comes to PPE:
- Performing a “hazard assessment” of the workplace to identify and control physical and health hazards, which may require PPE.
- Identifying and providing appropriate PPE for employees.
- Training employees to use and care for PPE.
- Maintaining PPE, including replacing worn or damaged PPE.
- Periodically reviewing, updating and evaluating the effectiveness of their PPE program.
Generally speaking, in terms of PPE, employees should:
- Properly wear PPE. Attend PPE training sessions.
- Care for, clean and maintain PPE.
- Inform a supervisor of the need to repair or replace PPE.
What are the OSHA Safety Meeting requirements?
There are safety training requirements dispersed throughout the regulations, but regular safety meetings may or may not be a required part of your safety training program.
With the exception of electric utilities, there is no OSHA regulation that specifically covers safety meeting frequency, length, and topic. However, some states do have requirements that must be followed. It is important that employers know the state-specific regulations in all the states they operate in.
OSHA safety training standards are typically task or hazard-specific and are therefore dispersed throughout the regulations.
Recent Changes & Additions
Like all laws and government regulations, OSHA’s standards sometimes change and sometimes new interpretations are handed down. OSHA updates its website regularly. Updates are announced via news release post and email newsletter, and you can search past updates by year or by category.
Inspections & Enforcement
The main way OSHA enforces regulations is with inspections performed by compliance safety and health officers who are experienced, well-trained industrial hygienists and safety professionals.
Normally, OSHA will not announce an inspection before it happens, but employers do have the right to require compliance officers to identify themselves and/or obtain a warrant prior to an inspection. The complete inspection process is outlined in a video produced by OSHA.
Often, the main goal of an inspection is to investigate employee complaints of unsafe work conditions. OSHA inspections follow a hierarchy based on what type of workplace hazard has been brought to the agency’s attention. The hierarchy is:
- Imminent danger situations – where there is almost certainly going to be a bad incident at some point if nothing is done.
- Severe injuries and illnesses – where there has already been a bad injury or bout of illness.
- Worker complaints – where a worker has brought something to OSHA’s attention, but it is not an imminent threat.
- Referrals – where a workplace is referred to OSHA by a third party.
- Targeted inspections – in some high hazard industries and/or workplaces.
- Follow-up inspections – where a workplace has been inspected previously and OSHA wants to ensure it has followed all recommendations.
OSHA has two different types of inspections that it performs:
- Phone/Fax – An OSHA representative will call the employer, detail allegations that have been expressed and then fax over a list of the alleged hazards. The employer has to respond within five business days detailing what has been done to correct the hazards.
- In-person – An OSHA representative will show up on-site to conduct an inspection that consists of:
- Preparation by reviewing the workplace’s inspection history.
- Presentation of credentials by the OSHA employee.
- Opening conference where the OSHA rep explains what will happen.
- Walkaround where the OSHA rep checks for hazards in the workplace.
- Closing conference where the OSHA rep discusses the findings with the employer and employee representatives.
These inspections can result in citations and fines for the employer.
What if You Aren’t OSHA Compliant?
If you are not OSHA compliant, you may be putting your employees at risk of injury, or illness, or worse. OSHA standards are meant to create the safest possible working environment and if you are not following them, your workplace might not be as safe as it could be. Workers are more likely to file an anonymous safety and health complaint if they are experiencing unsafe conditions.
If OSHA finds that you are not in compliance with its standards, you risk receiving citations from the agency that can result in hefty fines and a hit to your company’s reputation. People likely will not want to work at a company that does not put a priority on safety.
OSHA Complaints
Employees can register safety and health complaints on the OSHA website or by calling their local OSHA office. OSHA will not reveal the identity of the complainant to their employer.
OSHA evaluates each complaint it receives to determine the best way to handle each one. If a worker makes a complaint and wants an in-person inspection, they must submit a request in writing to an OSHA office.
At least one of the below criteria must be fulfilled for OSHA to conduct an in-person inspection.
- A written complaint signed by a current employee or employee representative that contains enough detail to enable OSHA to determine that a violation or danger is likely to exist that threatens physical harm or that an imminent danger exists in the workplace.
- An allegation that physical harm has occurred on-site as a result of the hazard and that the hazard still exists.
- A report of imminent danger in the workplace.
- A complaint about a company in an industry covered by one of OSHA’s local or national emphasis programs or a hazard targeted by one of these programs.
- Inadequate response from an employer who has received information on the hazard through a phone/fax investigation.
- A complaint against an employer with a past history of egregious, willful or failure-to-abate OSHA citations within the past three years.
- Referral from a whistleblower investigator.
- Complaint at a facility scheduled for or already undergoing an OSHA inspection.
An employee representative (either via the workers’ union or chosen by the workers if no union is involved) has the right to accompany an inspector while they are conducting an inspection. Any employee has the right to talk with an inspector confidentially. Workers are encouraged to inform the inspector of any concerns they may have.
After either type of inspection has been conducted, OSHA will share the findings, including penalties and actions undertaken, with the person who made the complaint. Copies of citations must also be posted at or near the site of violations so all workers can be informed of the hazard and what was done to fix it.
For a phone/fax inspection, an employer must fix the issues identified within five days. Because of OSHA’s hierarchy of complaints, there is no average time for dealing with them. Imminent danger complaints will be dealt with first and then others in the order of importance.
If an employer receives an OSHA complaint, they should immediately fix any issues identified within the complaint.
What Happens if You Receive a Whistleblower Complaint?
A Whistleblower Complaint is not the same thing as a regular Safety and Health Complaint, which is when an employee alerts OSHA to a workplace hazard that exists because the company is not following OSHA standards.
A Whistleblower Complaint can be filed when an employee has made a regular Safety and Health Complaint and the employer has threatened or retaliated against them in some way, such as firing or demoting them. If an employer retaliates against an employee for making a complaint, that employee can then file a Whistleblower Complaint and the company will then be investigated (not inspected) by OSHA.
Whistleblower Complaints set off a completely different series of actions and there is an entirely separate website dedicated to the investigative process and how to avoid these types of complaints. The easiest way to avoid a Whistleblower Complaint is to be OSHA compliant, fix any hazards that you are aware of, and avoid retaliating against an employee if they make a general Safety and Health Complaint to OSHA.
Becoming OSHA Compliant
OSHA compliance will make your workplace safer and save you money. The people who benefit the most from OSHA compliance are your employees, although your company’s Workers Compensation and Liability insurance will be lower, so owners and shareholders also benefit.
Following OSHA’s standards should always be viewed as a way to make sure your workplace is as safe as it can be.
Getting Started
Becoming OSHA compliant can seem like a huge task and sometimes companies don’t know where to start. OSHA has resources for employers who may be feeling overwhelmed with compliance.
The two most important resources for a company that is just getting started with compliance are:
These two resources will help a company quickly gain OSHA compliance and create a safer working environment for employees.
Evaluate the State of Your Safety Program
Many workplaces that have obvious hazards have some kind of written safety program. Workplaces where hazards may not be as obvious—in a grocery store or a beauty salon, for example—may not have official written safety policies, but there is likely an unofficial (and possibly unwritten) policy of working as safely as possible.
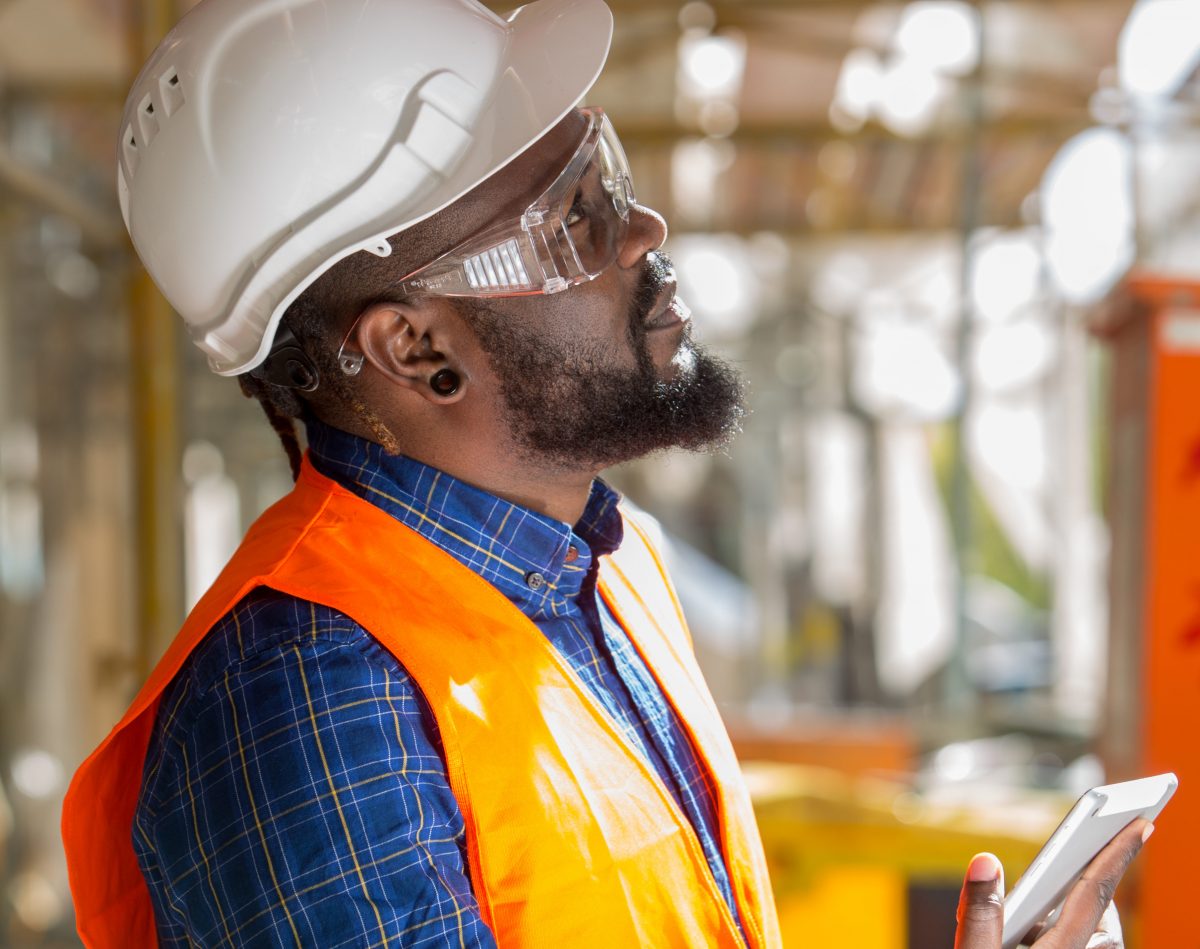
To evaluate your safety program, conduct an in-house assessment of your policies and practices. Review your current safety program (or create an official one if you don’t have one) that follows OSHA standards for workplace safety. You don’t need to do it alone. There are many resources you can use to help you update or create your workplace safety program.
OSHA Help For Employers
One set of tools that OSHA provides for employers is their Recommended Practices for Safety and Health Programs. Here, you can find many downloadable safety checklists, safety program self-evaluation sheets, and information packets that will help you make your workplace safer and help bring it in line with OSHA’s standards.
OSHA also provides free consultations to companies that want to make sure they are OSHA compliant. Compliance Assistance Specialists (CAS) offer outreach to groups like small businesses and other employers, trade and professional associations, union locals, and community and faith-based groups.
Separate from the CAS program, OSHA also offers a free consultation program that is aimed at small businesses in high hazard industries. You can request a free consultation with OSHA and even receive a one-year exemption from inspections while you make your business OSHA compliant.
Private Consulting
If you want a more specialized type of consulting than the free services offered by OSHA, you can hire a private consultant to help you become OSHA compliant. Perform your due diligence and research a consultant to make sure they are reputable and worth your time and money. Find reviews of them online and personally call any businesses that have given them testimonials to see what they are like to work with.
Safety Apps
Safety management apps can help you become OSHA compliant by giving you a compliance framework for your safety program.
Look for an app, like Safesite, that allows multiple levels of management to see your safety activities, hazard reports, and incident reports as they are logged by staff. Track compliance-related items such as PPE for workers, worker training, and recordable incidents.
Handle Hazards Immediately
While you are performing your self-evaluations, fix any hazardous situations immediately. Don’t mark them down to fix later. This way, you know for sure that a hazard will be dealt with and not fall through the cracks. Fixing problems immediately will also make sure that your workplace becomes instantly safer and help cut down risks to employees.
When OSHA inspectors perform an in-person inspection, they require you to fix any minor problems they find immediately rather than noting them down to fix later, and you should adopt this same strategy for the sake of your employees.
Education
In theory, everyone in your organization should know all of the safety standards for their area and should have updated training on a regular basis. OSHA offers a few different ways to help you with this:
QuickTakes Newsletter
OSHA’s QuickTakes Newsletter is distributed twice-monthly and provides readers with the latest news about enforcement actions, rules, outreach activity, compliance assistance, training, and educational resources.
OSHA Materials
Along with the newsletter, OSHA also provides businesses with other resources that can be used for informational and training purposes. These include OSHA Publications (fact sheets, brochures, etc.) and OSHA Videos.
Training
OSHA requires employers to train employees who face hazards on the job and to help businesses do this, the agency has many resources employers can draw from. You can find the required training by OSHA standard to see exactly what type of training you will need to provide.
OSHA also provides businesses with a number of resources to help them deliver the necessary training. Along with the publications and videos mentioned above, OSHA also provides:
- Resource for Development and Delivery of Training to Workers
- Interactive Web-Based Training
- Safety and Health Topics Information
- Hazard Alerts
- Susan Hardwood Training Grants and accompanying materials
- OSHA Alliance Program developed educational products
- Other third-party educational materials
Third-Party Training
Employers can find third-party entities that will provide training in OSHA compliance. If you opt to hire a third-party trainer or subscribe to an eLearning service, you should make sure they are reputable. They may not be associated with OSHA and therefore, their standards might differ.
Certification
The OSHA Outreach Training Program provides workers with basic and more advanced training about common safety and health hazards on the job. People who complete either a 10-hour course or a 30-hour course receive a course completion card. The shorter course is meant for entry-level workers while the longer course is for more advanced employees who have to take on some safety responsibility in their workplaces. You can find a thorough overview of the courses on the OSHA website.
OSHA also provides training for people interested in becoming trainers themselves so they can teach an OSHA Outreach Training Program. See the requirements on the program publication. You can find Outreach Trainers on the OSHA website for classroom training, online training and training in Spanish.
Improving Your Safety Program
Now is the time to create or update your Safety Management Program in your workplace to make sure that your business is OSHA compliant. You will need strong leadership involvement, effective processes and the right tools to help you.
Leadership
Safety starts from the top down in any organization. Leaders in management must “walk the walk” when it comes to safety and lead by example. If the CEO wants to visit a site that requires a hard hat and steel-toed boots, they have to wear that PPE without exception.
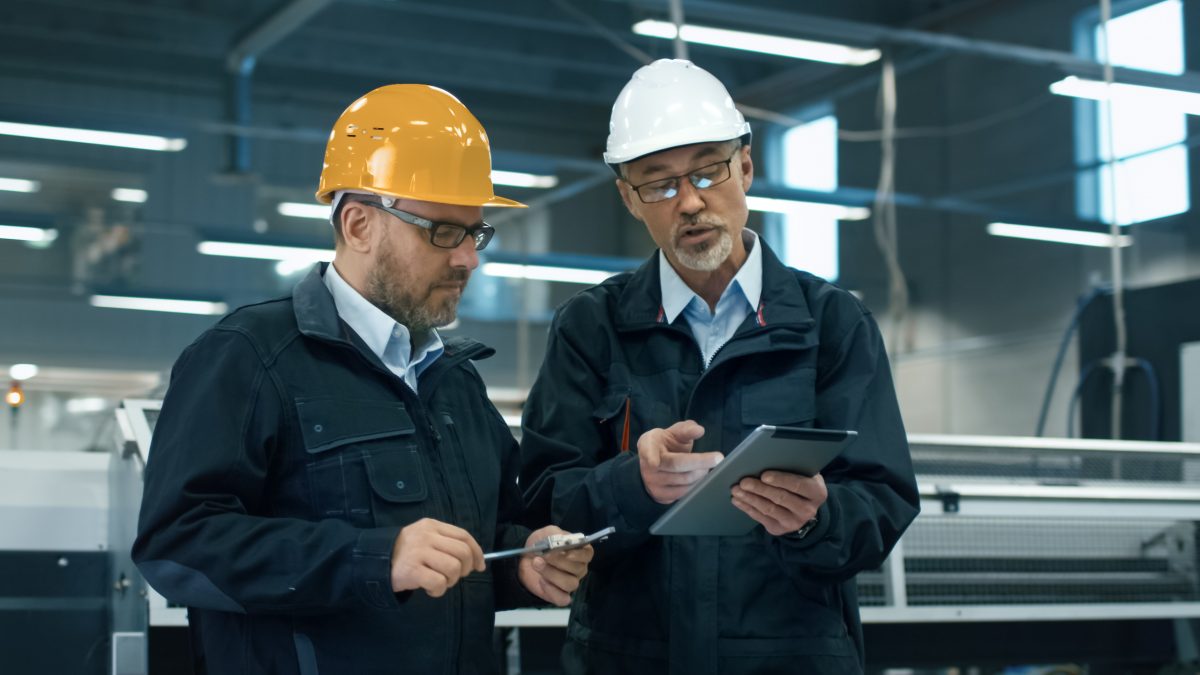
It is their duty to make safety a part of the company’s core values and identity. Everyone in management is responsible for making sure that safety is the number one priority within the company and displaying that so employees pick up on it.
Processes
To address safety as effectively as possible, a business needs easy-to-follow processes and procedures to make it as simple as possible to work safely. All workers must be trained to follow safe work procedures so nobody can say they did not know what to do in a given situation.
For this to be effective, there should be open communication lines between workers and management and employees should be encouraged to bring any concerns to management’s attention so they can be dealt with. Employees on the front lines are the ones with the best vantage point when it comes to doing things safely and their feedback in developing safe processes is important.
Inventory
Whether it’s PPE, color-coded tags or information sheets, a safe workplace will have the necessary inventory to keep workers injury and illness free. Check your various safety tools and replace any that are old or worn out and make sure all employees know how to properly use them.
Software & Apps
Safety management software (SMS, also known as environment, health, and safety or EHS software) can help you achieve OSHA compliance. Time savings is an often cited reason for implementing SMS. Where paper and spreadsheet-based systems require administrative hours, apps require only minutes.
Features like real-time incident reporting, safety observations, hazard management, and daily reports can help you manage every facet of safety in your workplace.
Staying OSHA Compliant
Staying OSHA compliant is an ongoing process. Equipment needs replacing, processes and standards change, and new people who require safety training come on board all the time. This means you have to constantly upgrade your safety program. You should aim for continual improvement with your safety program. It’s never completely finished because safety standards and practices are always evolving.
Daily, Weekly, Monthly, and Yearly Safety Processes
In order to make sure that your safety program is always at the top of your employees’ minds and stays up-to-date, you should have daily, weekly, monthly, and annual processes that you follow. Most companies create a “compliance calendar” to make sure no mandatory activities or reports are missed.
Daily
If your industry is especially hazardous, hold daily safety meetings at the beginning of shifts, highlighting any specific areas that require extra attention. Conduct daily inspections for workplace cleanliness, PPE, fall protective equipment, and other high-impact areas.
Weekly
At least once per week, go over your company’s safety record with employees during the safety meeting. This includes any incidents and near-misses that happened throughout the week. If your industry is not highly hazardous, you can hold monthly safety meetings. This should be the minimum frequency for safety meetings.
Monthly
Perform monthly safety roundups of all incidents and near-misses. This can be done via an in-house newsletter or memo. Check for any new training available from OSHA or other safety-oriented organizations that you deal with. Send necessary employees for upgraded training. Inspect PPE and safety equipment to see if anything needs to be replaced. (This can be done on a rotating schedule.)
Annually
Audit your safety program and update it where necessary. Conduct a review of your safety activities and identify quantifiable goals to help you improve in the coming year.
Checklists
Work through checklists during safety meetings and inspections. Free digital checklists allow you to easily record, track, and trend inspection items.
Go Paperless
Digitize your safety program to reduce waste and administrative time. Safety Management Software (SMS) ranges from checklist apps to multi-faceted safety systems with user-specific roles and reports. As you’d expect, the cost ranges from free to thousands of dollars per year.
Safesite is a free SMS offering real-time near miss and incident reports to alert leaders to pressing safety concerns. It also includes digital inspections and meetings to help you track leading indicators. When every element of your safety program is viewable on a dashboard, you can spend less time discovering what’s going on and more time on making improvements.
Hiring for Safety in a Talent Shortage
The job market in the United States is tight right now. You can increase your company’s chances of hiring top talent by keeping a safe record. Employees like knowing their employer cares about them and a safe workplace is a draw for top talent.
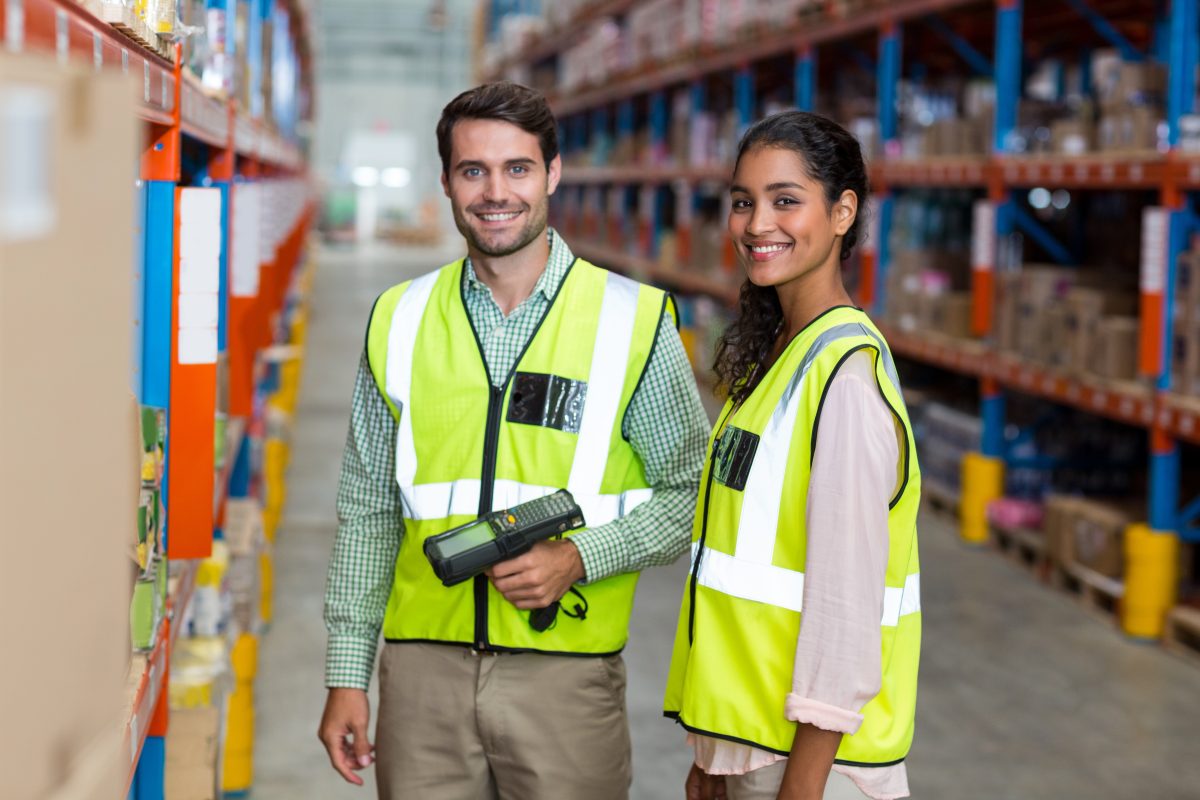
By consistently training your own employees, you can fill safety positions from within, saving you from having to attract people from outside your organization to fill vacant safety roles. If you do have to hire from outside, a good safety record will help attract talent.
Safety Program Change Management
If there are any changes to your safety program, all employees should be made aware with a comprehensive information push that includes a company-wide email, posters and bulletins, talking about it during safety meetings, and including it in the company newsletter.
Checklists are a go-to tool for auditing and inspecting workplace safety. OSHA standards-based checklists are an important tool for ensuring nothing is missed or forgotten during safety walk-throughs.
Additional Standards
OSHA is not the only organization that sets safety standards. Depending on your organization and where it conducts business, you may also have to follow standards from other regulatory bodies.
International Organization for Standardization
Consisting of representatives from 164 national standards bodies, the International Organization for Standardization (ISO) provides international specifications for products, services, and systems that make sure they are safe, efficient, and of high quality everywhere in the world. These standards are especially important for international trade and cover almost every industry.
American National Standards Institute
The American National Standards Institute (ANSI) is a private, not-for-profit organization that is dedicated to supporting and strengthening the US voluntary standards and conformity assessment system.
American Society of Safety Professionals (ASSP)
The American Society of Safety Professionals is a global organization with chapters in most states and cities dedicated to supporting occupational safety and health (OSH) professionals in their efforts to prevent workplace injuries, illnesses, and fatalities. ASSP provides education, advocacy, standards development, and a professional community in order to advance workplace safety and the OSH profession as a whole.
Others
There may be safety standards from other organizations that your business is obligated to follow based on the industry you are in or where you conduct your business (internationally, for example). Find out all of the safety standards that your business is governed by and incorporate them into your safety program.
Conclusion
OSHA exists to guarantee safe working environments for anyone employed in the United States. OSHA sets the safety standards for all businesses operating within the United States, either through the federal agency or through a corresponding state-run agency. It provides free resources to small businesses to help them comply with OSHA standards and provides training for employees, along with a process for employees to raise safety concerns with OSHA about their workplace.
If you haven’t yet, create a comprehensive safety program for your business (or audit your current one), make sure you are in compliance with all of OSHA’s standards that pertain to your industry and immediately start making safety a core value of your company by holding safety meetings and providing the necessary training to those who need it.