How many electrical hazards can you count around you right now? Unless you are off-grid, there’s at least a handful of electrical outlets and electrical tools nearby you right now. When functioning as they should and used correctly, they pose little risk. However, even a 120-volt household current can be deadly.
Managing health and safety at any workplace requires you to account for electrical hazards. After the introduction of 29 CFR Part 1910 Subpart S in 2007, electrical fatalities began to decline. But now, they have leveled off and range between 130 and 160 annually for the United States.
It’s not only electrical workers who face serious risks at work. According to the Electrical Safety Foundation International (ESFI), the construction and extraction industries made up 44% of all electrical fatalities in 2020.
Everyone needs to understand the power of electricity. In this guide, we’ll show you:
- Why electricity is dangerous
- What the consequences are of electrical injuries
- How electric shock becomes electrocution
- Who encounters electrical hazards
- What safety standards apply to electrical hazards
- Where the National Electric Code (NEC) fits
- How to reduce or prevent electrical incidents
Why Is Electricity Dangerous?
Electricity is a serious workplace hazard because it has the ability to cause both direct harm and indirect harm to anyone near it.
Depending on the type of hazard and exposure, electricity can cause electrical shock, fire, and explosions and lead to direct injuries like electrical burns. However, there can also be secondary injuries, even if the harm from the electrical shock is still minimal. For example, if you make contact with a live electrical part while working at height, you may also fall, which can compound or exacerbate the injuries, even if you’re tied on or wearing fall protection.
Electrical hazards are also dangerous because they’re both incredibly common and misunderstood. Unfortunately, this is true even for professionals who deal with significant electrical hazards every day.
A survey completed by Littlefuse Inc. found that the majority of workers whose job includes direct exposure to electricity believe it’s safe to work with up to 500 volts of electricity.
It’s not safe to work directly with any electricity. Why? Because you don’t need to make direct contact with an electrical hazard to experience electric shock. You can experience shock without ever touching a live electrical part.
What are the Consequences of Electrical Injuries?
Research shows that even if the injury doesn’t seem severe initially, you can still face long-term consequences. In one study published in 2021, 82% of patients studied had at least one complication following their injury.
The potential long-term consequences of an electrical injury may include a mix of psychological, neurological, and cardiological effects. These can include:
- Neuropathy
- Seizures
- Tinnitus
- Loss of balance
- Weakness
- Poor coordination
- Memory or attention difficulties
- Depression
- Muscle spasms
- Headaches
- Fatigue
- Joint stiffness
How Electric Shock Becomes Electrocution
What characteristic of electrical hazards is most likely to lead to a severe injury or fatality? If you‘re like most people, your answer is “high voltage“.
However, voltage alone isn’t what causes electrical shock: current plays an important role. And the issue with current is that there are many different ways that your body resists—or fails to resist—current.
Your skin is the most important barrier against electrical currents, and your internal body has very little resistance. If you have a cut, burn, or bruise or if your skin is wet, you will have less protection and the current will be better able to enter your body and course through it.
Electrocution is a fatal injury. It occurs when an electric current shuts down vital organs and burns your tissues. Whether an electric shock becomes electrocution depends on:
- Voltage
- Amount of internal body resistance to the current
- Path of the current through the body
- Length of time the current flows through the body
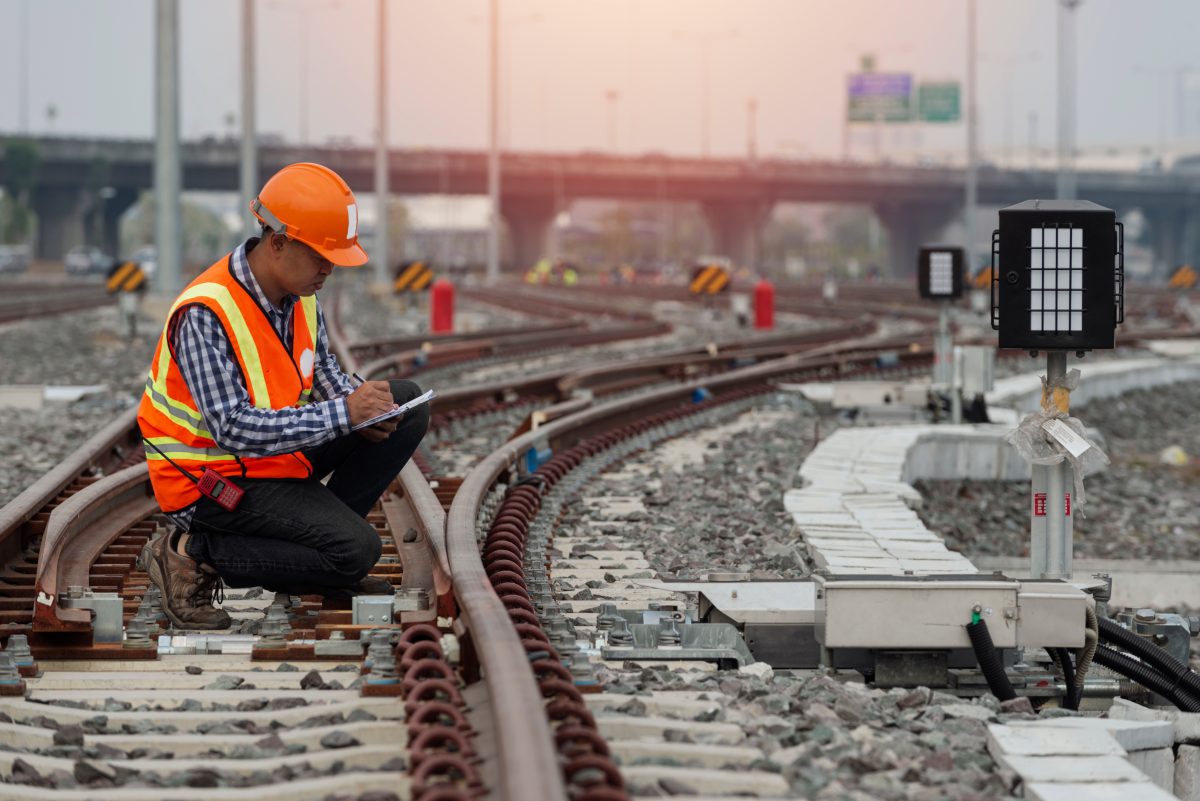
What Are Common Electrical Hazards?
The most common electrical injury is electric shock, but you can also experience arc flashes, thermal burns, and falls.
According to OSHA, these hazards are the most frequent cause of injuries:
- Contact with underground or overhead power lines
- Use of equipment outside the manner prescribed
- Failure to use ground-fault protection
- Missing path to ground
- Using extension and flexible cords improperly
Other potential electrical hazards include:
- Portable generators
- Exposed wires
- Faulty wiring
- Energized parts
- Damaged electrical outlets
- Overloaded circuits and outlets
- Worn, damaged, or faulty electrical cords
- Improper grounding
Certain working conditions also substantially elevate the risk of electrical hazards:
- Wet conditions
- Unrestricted access to exposed parts
- Inadequate wiring
Who Encounters Electrical Hazards?
If there is electricity in the workplace, anyone can encounter electrical hazards.
Even using extension cords outside of manufacturers’ guidelines is an electrical hazard, and it can happen in almost any line of work without the correct hazard communication and training.
Remember: you can encounter electrical hazards both in private residences and on industrial sites. The setting doesn’t dictate the risk. According to the Census of Fatal Occupational Injuries (CFOI) report for 2020, 33% of electrical fatalities occurred at private residences, whereas 31% occurred on industrial job sites.
What Safety Standards Apply to Electrical Hazards?
The OSHA standards covering electrical hazards focus on two subjects:
- Design of electrical equipment or systems
- Use of electrical equipment or systems
For safety professionals, both of these focuses are important. In essence, you need to make sure that the electrical components chosen for use on a job site are constructed and installed in a way that minimizes the risk of danger. This consideration includes making sure that any equipment or parts are tested in a recognized lab. Then, you can move on to ensuring everyone who encounters these hazards understands the risks and knows how to encounter these hazards as safely as possible.
The OSHA standards that apply to electrical hazards include:
- 29 CFR 1910.137, Electrical protective equipment
- 29 CFR 1910.269, Electric power generation, transmission, and distribution
- 29 CFR 1910.301-1910.399
- 29 CFR 1926 Subpart K, Electrical standards for the construction industry
- 29 CFR 1926 Subpart V, Electric Power Transmission and Distribution
- 29 CFR 1910 Subpart S, Electrical (General Industry)
If you operate in a marine environment, you’ll find the OSHA standards relevant to your work in 29 CFR 1917 (marine terminals) or 29 CFR 1918 (longshoring).
Where Does the National Electric Code (NEC) Fit?
In addition to OSHA regulations, certain industries may also opt to follow industry consensus standards, like National Electric Code requirements. The NFPA 70, National Electric Code (NEC) sets the benchmark guidelines for electrical design, installs, and inspections. While there is no legal requirement to follow consensus requirements, these are the rules that OSHA used when forming its own electrical standards.
Violating the NEC standards doesn’t come with fines or citations. However, OSHA can use a failure to meet or exceed NEC standards as evidence in an investigation not only for 1910.132 and Subpart S but also including a General Duty Clause citation.
How to Reduce or Prevent Electrical Incidents
Electrical current is a known hazard that is well understood. That means that incidents are highly preventable with the right strategies.
If you want to reduce and prevent serious injuries caused by electrical hazards at your workplace, there are a number of strategies that you can take.
Eliminate or Substitute Electrical Hazards Where Possible
The best way to avoid electrical incidents is to prevent exposure to these hazards. There is almost always space to eliminate some hazards.
Here are a few examples of ways you can eliminate or substitute an electrical hazard on a job site:
- Call 811 prior to starting a project. With advice, you can mark out buried utility lines and prevent workers from going near them.
- Ask the power company to de-energize overhead power lines before beginning work. Don’t begin work until you have confirmation that it’s safe.
- Switch from power tools powered by mains electricity over to cordless power tools. Remember that overloaded outlets and damaged power cords are two common culprits of electric shock.
- Reduce the voltage with transformers.
Use Engineering Controls to Reduce Remaining Risk
The primary cause of electrical incidents is often the lack of engineering controls. A few controls you might deploy include:
- Choose the correct type of cables, ideally well-insulated cables
- Use protective conduits in outdoor spaces to protect cables from crushing
- Ensure fuses are correctly fitted
- Only allow a qualified electrician to complete installations and make repairs
- Install circuit breakers to detect and prevent electrical fires
- Use ground-fault circuit interrupters (GFCI) to shut off power in the event of a “leak”
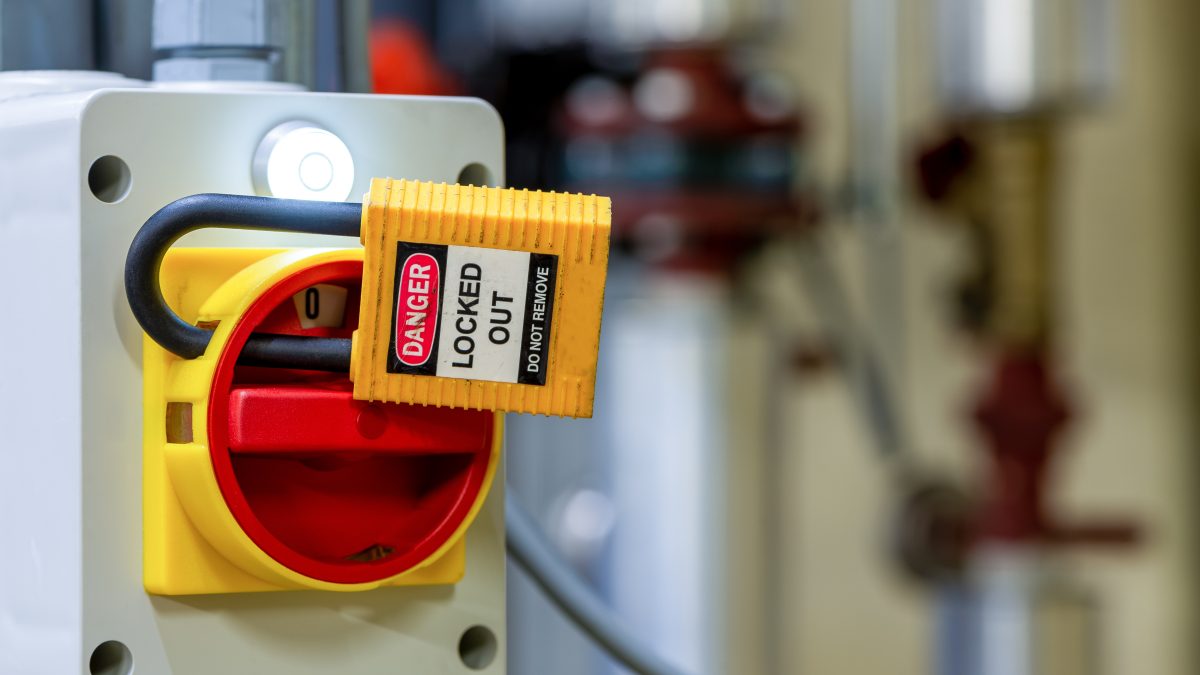
Make Lockout/Tagout (LOTO) Part of Your Culture
Lockout/Tagout (LOTO) is an effective method for protecting workers from electrical energy. With LOTO, the system is de-energized before an employee works on it so they are protected from the electrical hazard. A LOTO policy also happens to be part of OSHA’s general industry standard. Yet, taking shortcuts around a LOTO policy remains common. And every LOTO shortcut could lead to a fatality.
So how do you make sure LOTO becomes the default method of working?
- Provide regular LOTO training and refreshers for anyone who might perform LOTO, not just maintenance or electrical teams
- Make LOTO equipment and procedures accessible for those who need to use them
- Use spot inspections and regular audits to ensure your LOTO policy continues to meet best practices
- Mark locks and tags with names or photos
Are you looking for more LOTO resources? Use these to support LOTO compliance at your site:
- OSHA’s Lockout-Tagout Interactive Training Program
- Safesite’s 4 Essential LOTO Safety Meeting Templates
- Safesite’s 3 Essential LOTO Inspection Checklists
Keep a Strict Preventative Maintenance Schedule
Maintenance plays an important role in preventing electrical incidents, particularly when you are using anything that connects to your power supply. Regular visual checks on plugs, connectors and cables help identify damage that increases the likelihood of malfunctioning and injury.
Workers should never use damaged or faulty electrical equipment, and any repairs should be taken care of by a competent person.
Post the Required Hazard Signage
OSHA requires you to post Danger, Warning, and Caution signs in relevant areas to warn and remind workers of hazards. You’ll need signs for the following electrical hazards:
- High voltage and voltage rating
- Electrical panel
- Electrical room
- Electrical equipment
- Overhead power lines
- Battery charging
- Static grounding devices (ESD)
- Arc flash
- Transformer
Run Hazard Recognition Training
For workers to best understand the risk posed by electrical hazards, you need to let them know about those risks.
Electrical hazard training should make a regular appearance in your safety meeting calendar. Regular reminders tempt workers away from working in ways that can override your engineering controls and ramp up the risk of an electrical shock.
Some electrical safety training topics include:
- Basic electrical safety
- Electrical hazards
- Electrical PPE: how and when to wear it, how to maintain it, and what its limitations are
- Electrical injuries
- OSHA electrical safety regulations
- Lockout/Tagout (LOTO)
- Electrical emergency response
- Electrical safety inspections
Provide, Maintain, and Inspect Personal Protective Equipment (PPE)
As safety pros, you know PPE is the last line of defense. Even still, it’s an incredibly important factor in minimizing what’s left of the threat, especially in electrical work.
Electrical hazards vary greatly, and a hazard analysis can help identify necessary PPE. While one list cannot cover all situations, here is some potential PPE along with other protection that you may find yourself using in the field when working with live electricity.
- Insulated gloves
- Dielectric safety glasses
- Voltage detectors
- Insulated mats
- Insulated ladders
- Rescue rods
The PPE needs to be non-conductive and rated for the electrical current encountered. Inadequate PPE will not only provide little to no protection, but it will give the wearer a false sense of security.
However, you need to go further than ordering and providing PPE. According to the 2022 edition of the annual Fluke Safety Survey, 78% of electricians, who are most frequently at risk, say they will skip wearing the right PPE. Why? They say it’s a matter of convenience rather than ignoring safe work practices.
In this cohort, electrical work requires precision. When provided with gloves not up to the take, they take them off because they feel it’s more efficient or even safer than wearing oversized or poorly fitted gloves.
So, when ordering PPE, start with samples from providers and figure out what products work best for your team. Adding another step into your order process could protect your teams from serious injury caused by electrical current.
A Smarter Way to Manage Electrical Safety
Electrical safety is an important topic that’s worthy of regular attention. Whether at work or at home, electrical hazards are everywhere. The only thing protecting us from electrical shock is our knowledge of health and safety, along with meeting good standards of design, manufacturing, and installation.
Like most hazards, electrical hazards require inspections to ensure they haven’t become an outsized risk to your workers. Safety management software can help you manage hazards across every site by digitizing your inspections, making it easy to report hazards, and storing your electrical safety toolbox talks. Are you ready to get started? Get started free or request a personalized demo of Safesite, our award-winning safety management system for companies of all sizes and industries.