Major change is bound to happen in any organization, no matter how big or small. Events such as a transition in leadership, corporate expansion, product changes, or technical equipment upgrades can have a dramatic impact.
Management of Change (MOC) is a formalized process for leading your employees through a smooth and safe change process.
What Is Management of Change?
Management of Change (MOC) is a systematic approach to dealing with organizational change, typically in industrial facilities and operations. The goal of this approach is to safeguard workers from potential harm during the crucial period of transition.
In the United States, MOC is required for a relatively small subset of industrial companies. However, any company seeking to control risk during process transitions or updates to equipment can benefit from MOC.
The Risk of Change
Numerous studies and historical data shows that the safety risks to workers during change is many times higher than during routine production operations. Workforce safety is one of the biggest concerns that go along with managing organizational change.
A change to core processes, even temporary ones, can endanger the health and even the lives of the workers. These risks are further magnified in companies dealing with chemical substances and hazardous energy in their production system.
It’s critical to recognize and define change before introducing it to the process.
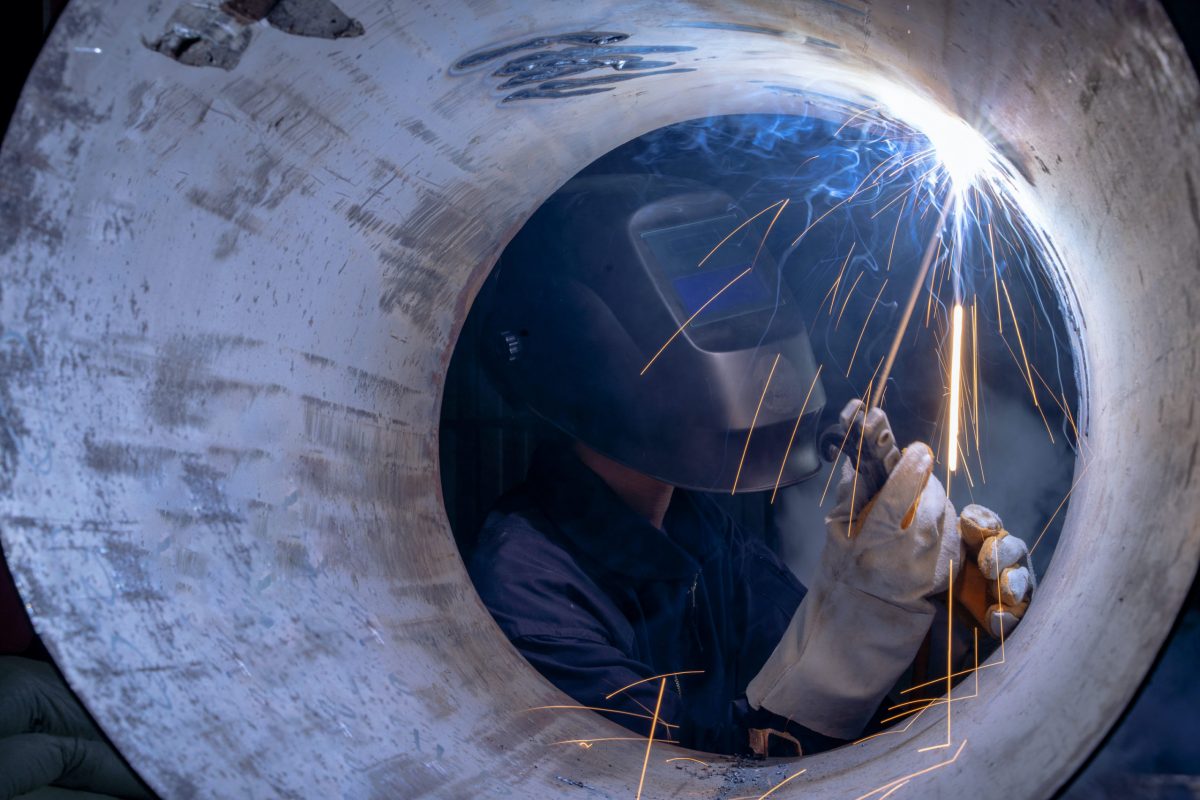
Addressing Change Risk with MOC
Without MOC, change can become more painful and challenging than it already is. Sudden changes in procedure and workflow can cause confusion among workers and contribute to process breakdowns.
A lack of familiarity with new processes and equipment can lead to accidents that could impact the environment, lives, and property.
While the concept sounds simple in theory, the reality is that organizations tend to either ignore that changes are happening, or rush changes to just “get it over with.” In the workplace, the focus is often on getting the job done, not on preventing risk.
The best argument for having an MOC process in companies not required to have one by OSHA is risk recognition, which may involve safety, quality, production, or other key performance areas.
In the environmental health and safety area, neglecting change management causes management executives to fail to anticipate catastrophic events that can stem from the change process.
MOC forces organizational leaders to take a step back, analyze proposed changes and evaluate all of the potential risks. This allows them to develop a systematic plan on how to prepare the organization to reduce or prevent those hazards. In other words, MOC is a temporary safe program for the organization.
Examples of Changes to Manage with MOC
Since every company has different types of risk exposure and different tolerance for failures, it is up to each business to analyze the hazards of the proposed changes and to define its tolerance for risk.
A few examples of types of changes that should be assessed are:
- Addition of new process equipment or critical business system (including software)
- “Not in Kind” replacement of process equipment or parts
- Modifications or minor additions to process equipment
- Modifications or minor additions to infrastructure / non-process equipment
- Changes to process control and/or instrumentation
- Changes in critical process parameter operating limits
- Alterations to safety systems (interlocks, shutdowns, fire or explosion suppression, etc)
- Revisions to standard operating procedures (including emergency procedures)
- Changes in site-level organizational structure
- Changes to maintenance procedures
- Changes in raw material/component specifications or sourcing
- Alterations or new connections to utility systems (air, electrical, gas, water, steam, etc).
- Changes to QA procedures or critical test equipment
To assess risk, engage a cross-functional team in a few hours of what-if brainstorming. Do this early, while you’re still in the planning stage. Develop the definitions and examples that apply to your situation and the risks your workers will be exposed to.
If risks can be reduced with a formalized change process, MOC will benefit your organization.
Agencies Involved With MOC
Management of Change can be implemented in any organization, but it is mandatory for industries dealing with certain chemical hazards. Below are some government bodies that deal with MOC compliance.
OSHA
The Occupational Health and Safety Administration (OSHA) is the primary agency responsible for ensuring compliance with workplace safety guidelines in the United States. This agency is in charge of implementing a systematic approach called Process Safety Management (PSM) and does so under 29 CFR 1910.119.
Only certain industries are regulated under PSM, according to OSHA, “PSM applies to those companies that deal with any of more than 130 specific toxic and reactive chemicals in listed quantities; it also includes flammable liquids and gases in quantities of 10,000 pounds (4,535.9 Kg) or more.”
It contains requirements and procedures for minimizing or eliminating threats arising from dangerous chemicals. Compliance with PSM standards is important because it prevents the negative effects associated with hazardous chemicals.
EPA
The United States Environmental Protection Agency (EPA) is another regulatory body that implements risk management program guidelines. They deal mainly with organizations in danger of chemical-related accidents. Management Of Change (MOC) is a critical part of the EPA’s chemical accident prevention program.
The EPA has a full list of regulated substances, provisions, guidelines, and requirements that organizations must follow to ensure full compliance.
COMAH
The Control of Major Accident Hazards (COMAH) is the equivalent regulatory body in the UK. Just like the OSHA and the EPA, their primary goal is to set forth safety guidelines and standards for everyone to follow. Their primary objective is to prevent major accidents (especially chemical-related accidents).
The COMAH also seeks to limit the effects of chemical hazards on the environment in the event of any major accidents.
When is MOC Needed?
As outlined above, it’s important to identify circumstances when Management of Change must be applied. Below are some of the situations and applications when MOC is needed.
Changes in Equipment Design
Whenever there is a change in the operational specifications of the equipment used within a company, there is a greater danger for workers to make mistakes. Therefore, it’s important to indicate the changes in equipment design (and specs) within the Process Safety Information.
Employers also need to come up with a safety plan on how to shield employees from potentially adverse events arising from these changes. For example, if a piece of equipment gets upgraded with a vital feature such as a valve installation or a new alarm, these require MOC implementation.
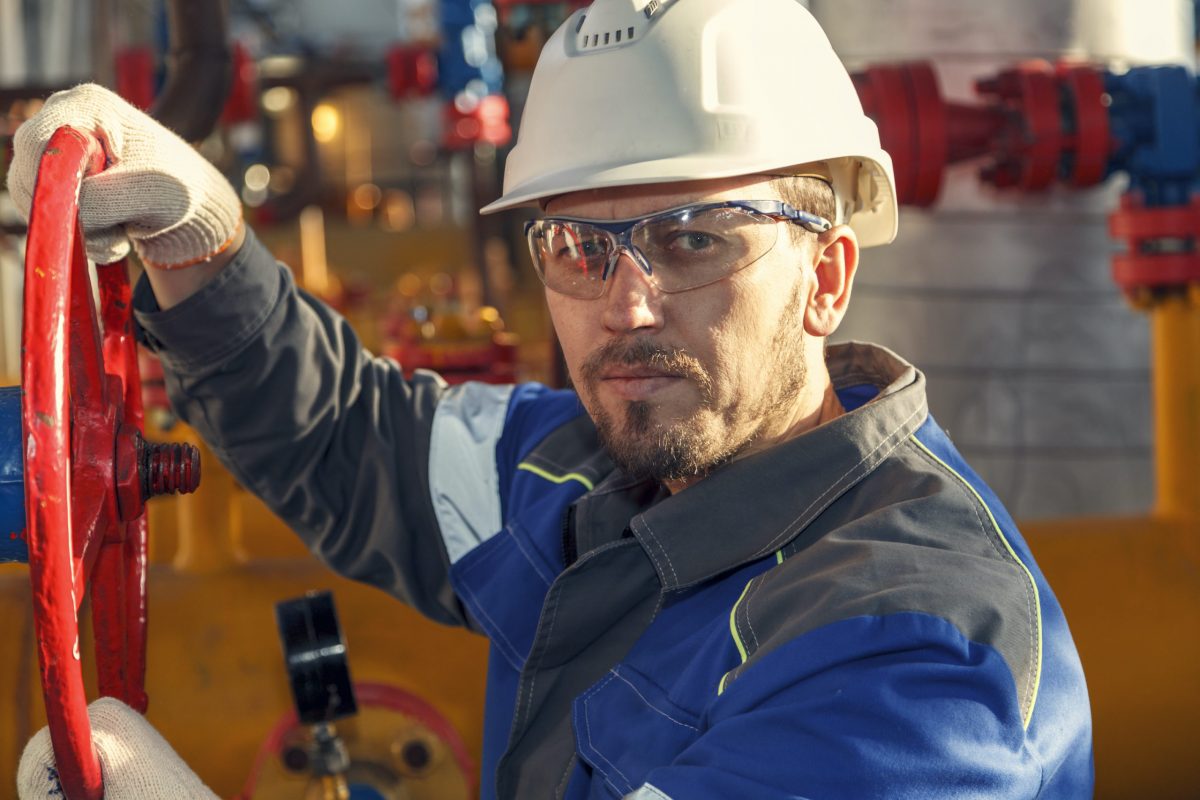
Changes in Operating Procedures
Each piece of equipment comes with step-by-step procedures on how to operate. Furthermore, each aspect of work in a firm has systematic end-to-end procedures that employees can simply follow and execute repeatedly.
Whenever operation guidelines or procedures are changed or updated by the company, there is a risk for workers to continue with old processes because they are more used to it.
Years of following a particular process can lead to muscle memory, and employees may enter a stage where they have difficulty adapting to new workflows. Of course, accidentally following old procedures is extremely dangerous. MOC is also required in these situations.
Changes in Inspection and Test Maintenance Procedures
MOC is needed when a company’s way of inspecting and maintaining their equipment changes. This ensures that employees don’t get exposed to chemically associated hazards.
For example, procedures related to preventive maintenance of machines, an inspection of piping, and servicing of equipment should be properly documented. Any changes to these maintenance procedures must go through MOC.
Facilities Changes
MOC is also required whenever there are changes to the facilities themselves. For example, when a new structure is built close to a PSM-covered piece of machinery, or if it is modified in some way, MOC must be performed. Proximity to machines and equipment can increase the risk of accidents.
Temporary Changes
Temporary events such as the examples below require MOC:
- Transfer of equipment to a temporary location due to infrastructure expansion
- Temporary procedure changes due to the installation of new equipment features
Even though these changes will not become a part of your standardized processes, it is still important to be prepared for any negative impact they may have on the organization, its facilities, and its people.
It is also critical for organizations to close out any MOC documentation of a temporary change or to update the program if the temporary change becomes permanent.
Hazard recognition is the most important aspect of successful MOC implementation. Rather than hyper-focusing on the changes themselves, your goal is to anticipate and understand the hazards that will arise from change.
Likewise, all affected employees should be trained, equipped, and empowered to expose hazards.
The Steps of MOC by Industry
Management of Change is a major component of a bigger process called Process Safety Management (PSM). Compliance with PSM as a whole requires a thorough knowledge of MOC best practices and steps.
You’ll notice that hazard recognition is the most important step in successful MOC implementation. In this stage, the main focus is not on the actual changes that are happening in the organization, but in anticipating and understanding the hazards that will arise from such changes.
To do this, there must be a thorough review of things that could go wrong and how to prevent those situations. There must also be a safety plan put into place if and when an accident occurs.
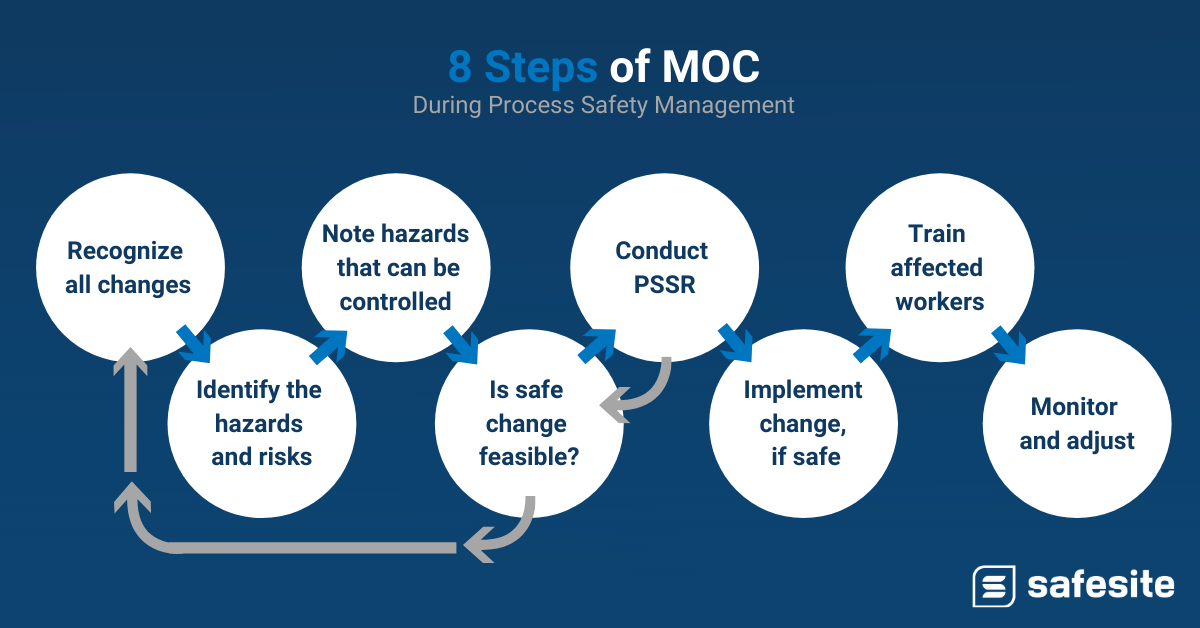
Employers and organizational heads should never underestimate this process hazard analysis stage. The overall success of MOC depends upon it.
Murphy’s Law states that “whatever could go wrong, will go wrong.” And so, people in charge of MOC should put any risk or danger in consideration, no matter how unlikely they may be to cause any significant trouble.
8 Steps To Management of Change
Although the specific process of MOC may vary a bit for each industry (there are different types of MOC), the general steps are pretty much the same.
Here’s the step by step rundown of what it takes to perform Management Of Change:
1. Recognize all changes. Without a thorough understanding of what changes are going to happen, it is difficult for a management team to evaluate its potential impact to the organization. Know the details of the change, so that it can be properly managed.
2. Identify the hazards and risks. A careful risk analysis must be done to cover every potential hazard that the change will cause. Seemingly minimal effects should never be overlooked. Instead, they should be treated as though they can impact the organization in a big way. Worst-case scenarios for each risk must be identified, so that steps can be made to avoid them.
3. Note hazards that can be minimized, controlled, or totally avoided. Management needs to accept the reality that not all risks can be avoided. Some can only be managed or reduced. It’s important to determine which risks can be totally avoided. Plans should then be initiated to reduce or manage unavoidable hazards.
4. Find out if the change is feasible or can be implemented given the circumstances. This is more like a risk-reward analysis. The management team can ask themselves, “Can the changes be done with the least amount of danger possible, or do the hazards caused by the change outweigh its rewards?”
5. Conduct a Pre-Startup Safety Review (PSSR). The PSSR is a thorough review of equipment and its related processes to ensure that safety measures are in place. It is most often used in processes involving chemical substances. This is more like a verification check of the entire rocket ship before take-off (you get the picture).
6. Implement the change — if safe to do so. The organization must implement the change, knowing all the risks in advance and how it might impact the workers. The goal of responsible leadership must be to help employees smoothly glide through the painful process of change without endangering them. Emergency measures should also be in place if a potential accident turns into a real one.
7. Train all affected workers. Any involved employee, as well as all managers who will execute your new processes, should be carefully trained on the new procedures. More knowledge and hands-on-training will lead to fewer or zero instances of mishaps, or to less serious consequences when failures occur.
8. Follow new procedures and continue to evaluate feedback from the ground. As changes are rolled out, management should continue to evaluate the worker’s exposure to risk. This can be receiving continuous feedback and reports from the organization’s day-to-day operations.
Management Of Change does not mean that risk management is conducted only during the change. The truth is, MOC happens long before a change is even implemented.
Ideally, employers conducting MOC have already anticipated workforce safety issues even before changes are introduced.
The above general steps may vary a bit depending on the type of MOC required. The three most common types are administrative MOC, organizational MOC, and technical MOC.
Industry-Specific Steps
For companies requiring MOC procedures under OSHA, documentation is a critical component. Petroleum, pyrotechnics/explosives, storage facilities, and small businesses dealing with hazardous chemicals each have unique demands surrounding change.
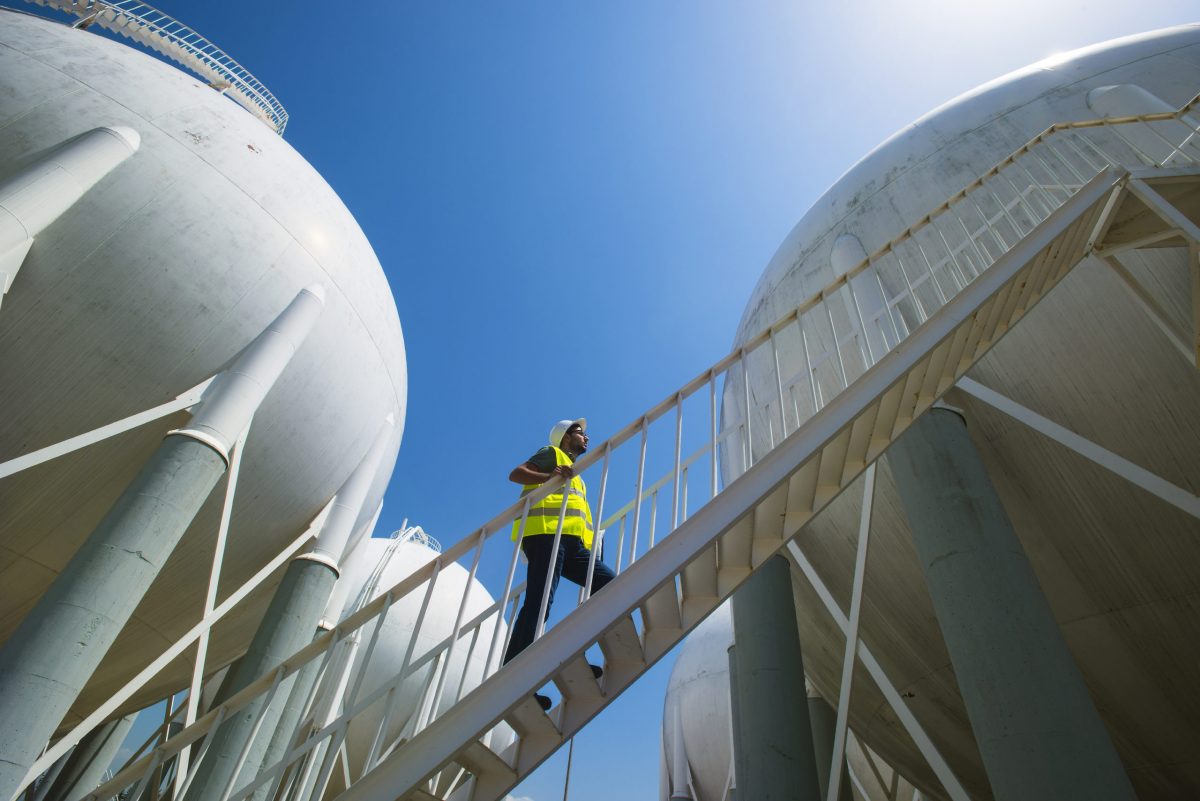
Petro-Specific MOC
For petroleum refineries, your MOC plan should include descriptions of:
- The technical basis for the change
- The impact on safety and health
- Modifications to operating procedures
- The necessary time period for change
- Appropriate authorizations
- Training of affected employees
These written descriptions may be used to fulfill the OSHA requirements for MOC. Be sure to include all relevant changes in your documentation and MOC process.
Some commonly (and unlawfully) overlooked changes include:
- Installing a control valve bypass
- Installing a spill guard berm under a fracturing tank along with
proper grounding and bonding - Changes to an alarm set point
- Changes to materials of construction
- Changing procedures for the manual addition of methanol to a
chloride injection tank - Procedures for installing a new type of relief device
- Changing inspection intervals for piping circuits
- Changing the number of thickness measurement locations (or
condition monitoring locations) on a pipe - Changes to a control room located within a PSM covered
process unit
The full guidelines and requirements for petro-specific MOC are discussed in this procedure document for petroleum refineries.
Explosives Manufacturing MOC
Those who manufacture explosives and pyrotechnics are required by OSHA to regularly inspect their equipment. Each thorough inspection must be properly documented to serve as proof of PSM compliance. The recorded inspection data may also be used to assess the long-term degradation of equipment after many years of use.
If the periodic inspections show deficiencies and malfunction in the equipment, the use of the equipment may be limited or stopped. During this time, an MOC procedure will be implemented. The employer will be required to assess and document the potential hazards of continued usage.
MOC For Small Businesses
Small business changes require MOC if the development and distribution of their products expose their workers to hazardous chemicals.
Here are some examples of hazardous chemicals which may be used by small businesses:
- Asphalt paving or roofing materials
- Pharmaceuticals and/or byproducts
- Plastics and rubber
- Stone, glass, and concrete
- Other chemical products
The MOC process for small businesses don’t vary much from that required in other business types. However, many small business owners are still not fully aware of process safety management standards.
MOC For Storage Facilities
OSHA requires storage facilities to conduct a process hazard analysis to ensure that hazardous chemicals are properly handled within designated storage areas.
Some of the factors that need to be considered are:
- Incompatible materials should be separated, especially combustible materials that might cause a fire.
- Temperature levels must be ideal for the type of chemicals being stored.
- High temperatures for flammable materials should be avoided, while extremely low temperatures that could hurt the integrity of certain chemicals should be prevented as well.
- Storage areas must maintain a safe distance from fire zones.
If an outdated operation is discovered in the storage procedure, employers must develop and implement MOC to address the issue. The newly updated process must undergo the usual hazard analysis. It must also be properly documented then communicated to the affected employees.
MOC Resources
The most valuable resources for MOC management are information/assistance provided by your regulatory body, MOC checklists and forms, and safety management software.
MOC Forms
Your company’s change request process likely has an official form that allows you to officially initiate and monitor the process.
If you haven’t already, create a change request form to support the applicable steps of MOC (1-4):
- Recognize all changes.
- Identify hazards and risks.
- Note hazards that can be controlled or minimized (and how).
- Find out if the change is feasible given the circumstances.
If you don’t already have a Change Request Form or MOC Change Form, you can customize this template.
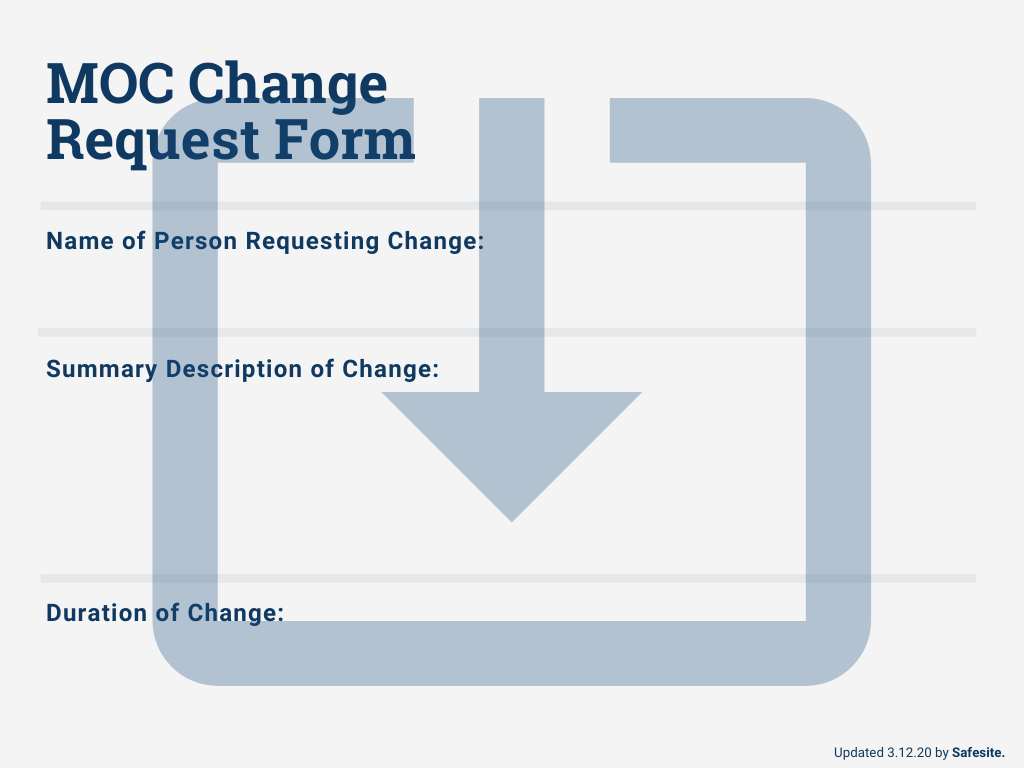
Your change form should include sections for:
- Requester’s contact info and date of submission
- Description of the proposed change
- Rationale and data to support the change
- Hazard identification and risk assessment of change
- Hazards and risks associated with not changing
- Business impact of proposed change, including cost
- A list of all persons responsible for the change procedure
- Estimated duration of change and proposed start and end dates
- A place for stakeholders to sign off on your request
When every change is documented from the moment it’s introduced, management can easily review records when needed.
MOC Checklists
Checklists allow you to facilitate and oversee your MOC plan.
You may want to build from past checklists used in your company or edit a checklist template that will allow you to implement and monitor all the steps in your plan.
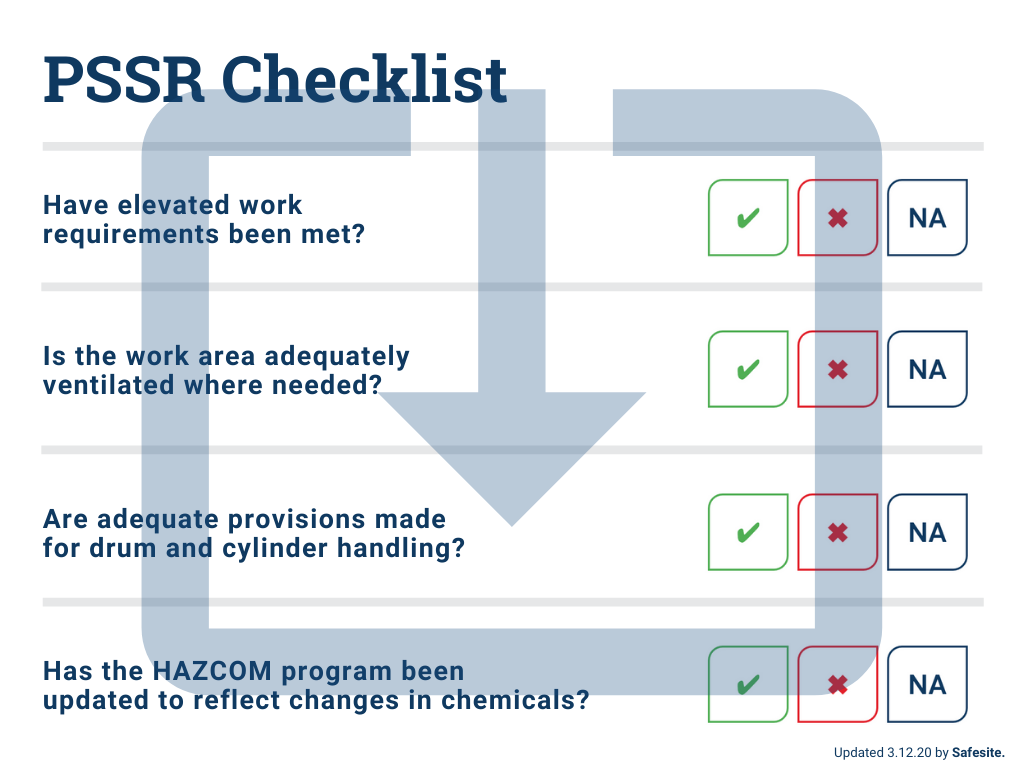
Search the Safesite template library for more MOC checklists, or upload your own for free.
Safety Management Software for MOC
Safety Management software is designed to support safety processes like training, inspections, and hazards. You can use software like Safesite to reduce the paperwork and improve hazard recognition related to your MOC process.
For example, as you conduct your PSSR, you can use data from mobile inspections (including images of hazards and equipment inspection logs) to inform your assessment. You can also use a master PSSR checklist to ensure you’ve completed every step.
The implementation phase is where safety management software becomes invaluable. Run your new process, inspections, and test procedures in the field with mobile checklists. Document employee training and attendance related to the train so no worker is left behind. Finally, report and share near misses with your team to prevent incidents.
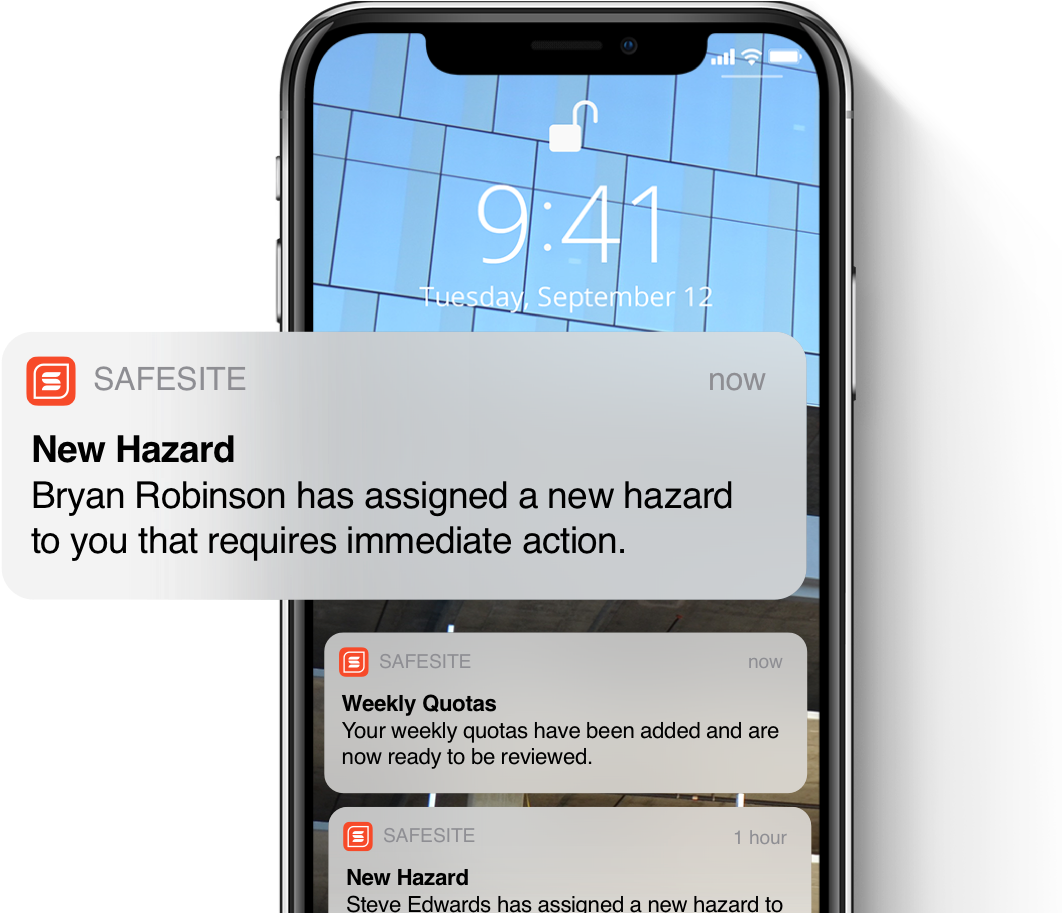
Through real-time reports and notifications, management will be able to monitor all aspects of the change and recognize warning signs before something goes awry.
OSHA MOC Resources
OSHA provides a dedicated resource page for Process Safety Management, which includes Management of Change. Pages dedicated to applicable standards, hazard recognition, and evaluation/control outline common hazards and provide insight into changing your processes safely.
This section also houses OSHA publications for covered industries, including petroleum, explosives, small business, storage facilities, and chemical facilities. This literature includes ways to remain in compliance with OSHA standards, but it may also be helpful if you’re not explicitly covered under the PSM standard.
For example, Process Safety Management for Petroleum Refineries lists commonly overlooked changes. Choosing to upgrade equipment, changing emergency procedures, and changing valves/switches are just a few changes that many companies — not just oil and gas — choose to make without a documented MOC plan. The resulting risks to workers’ lives could be avoided with Management of Change.
OSHA also has an electronic newsletter, QuickTakes, which helps employers stay updated on recent developments in the field.
Assistance is also provided to non-English-speaking employers via the Spanish version of the website.
The OSHA Outreach Training Program offers courses and seminars for the general public. Courses may take 1-4 days to complete. They discuss the most important areas of PSM compliance, such as:
- Hazardous materials
- Machine safety
- Construction topics
- PSM documentation
- And many others
Sending your staff to undergo these courses, or attending them yourself, can be a great help to your organization.
If you need a more hands-on approach to MOC compliance, you can try OSHA’s Onsite Consultation Program. With this free and confidential assistance service, your company will be visited by an OSHA compliance assistance specialist to help identify areas of potential hazards within your workplace.
The assistance specialist will then provide suggestions on how you can comply with agency standards. You will also receive tips for improving workplace safety and how to facilitate smooth MOC procedures. This is a consultative visit and will not be treated as a formal inspection by OSHA.
Third-Party PSM Compliance Assistance
If you prefer to limit the OSHA’s involvement during your internal review of your organization’s hazards and safety measures, you can opt to seek the help of third-party compliance assistance specialists.
These third-party assistance specialists are private entities that are not affiliated in any way with the OSHA. They provide a variety of consulting services that will help your organization improve in all aspects of PSM. They can also suggest standard procedures that you can implement in your company. This is not just for OSHA compliance purposes, but for the overall safety of your employees as well.
To select a Process Safety Management (PSM) and Management of Change (MOC) team lead or consultant, look for individuals with field management experience. Knowledge of the specific hazards you’re dealing with — and the safety training required to address those hazards — is also critical.
Change Management During MOC
So far, we’ve talked about Management of Change (MOC). It deals with the technical side of change and how to avoid or minimize risks arising from changes in equipment, process, and handling of chemicals.
However, change also has a ‘people aspect’, wherein the role of management is to influence people’s behavior in reaction to technical changes.
Dealing with the people side of change is known as Change Management (CM). The challenge for any organization is to smoothly perform change management during MOC.
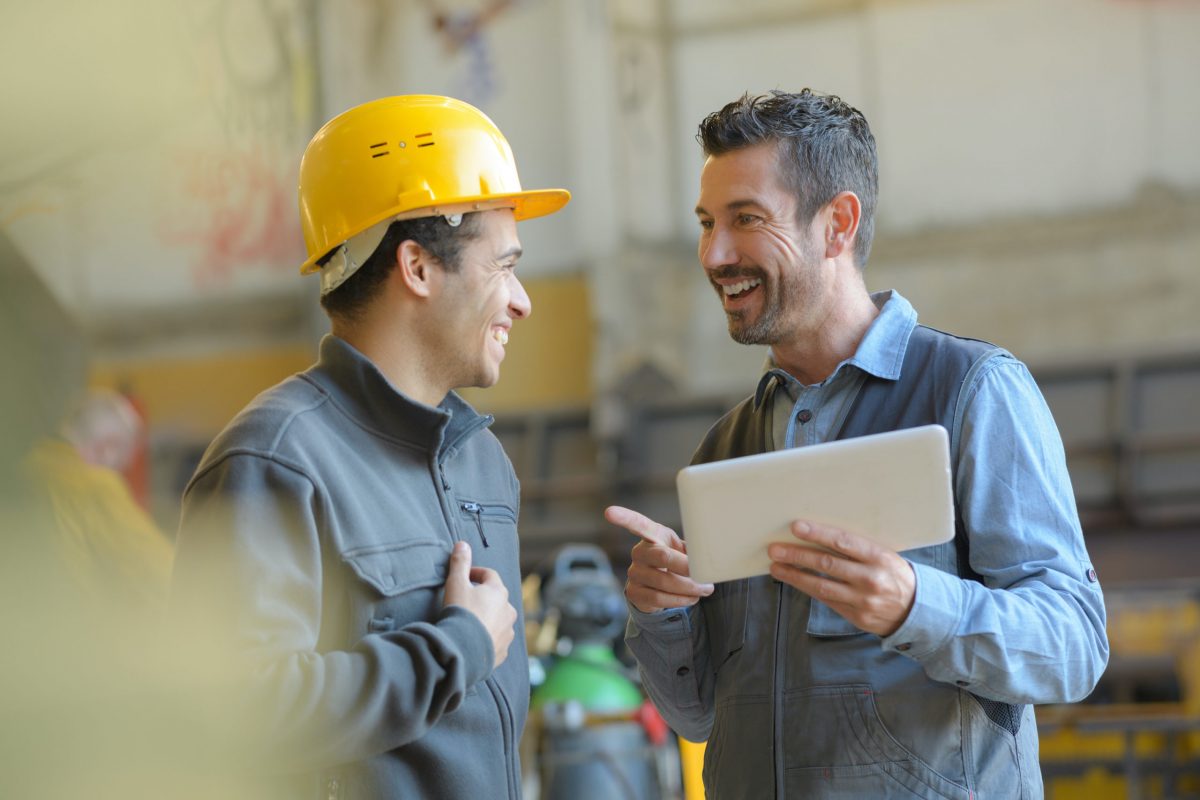
To effectively differentiate MOC and CM, it’s important to note that change management’s main goal is to effectively guide people to transition from a past/present state to a future desired state.
For example, if the manual operations required to be performed are reduced due to more advanced equipment introduced within the company, Management of Change (MOC) is needed to document the changes in processes, equipment handling, and associated risks involved.
On the other hand, Change Management (CM) is required to deal with the impact of the change on the individual operating the equipment itself. Because lesser manual operations are now required on his end, the employee’s workload may decrease. This may lead the company to add more items to his job description. In more severe circumstances, the company might have no choice but to initiate a reduction in pay or even declare the position as redundant.
These types of changes to work circumstances can impact the behavior of employees. The goal of Change Management is to minimize the risks associated with people’s behavior during changes. This can be done by using the following managerial elements:
- Effective communication
- Competent leadership
- Proper feedback
- Implementing a system of rewards and reinforcement
To smoothly transition through major changes in an organization, employers and managers should implement a good balance of MOC and CM. This ensures that both the technical side and people side of change are dealt with simultaneously.
How Can MOC Benefit Your Company?
It’s true that evaluating and documenting organizational change can be time-consuming and costly. But it’s 100% worth it.
Equipment and facilities will eventually fail, and people will be exposed to chemical, health, and other job-related risks when they do. It’s your job to protect your employees, both legally and because it’s the right thing to do.
Expect changes to happen, and execute the Management of Change (MOC) steps to keep your organization thriving. Use safety management software to ease your administrative burden, increase visibility, monitor your new process — and repeat.