The statistics regarding the dangers of welding are daunting to read. More than 560,000 workers are injured each year from welding accidents, according to the Bureau of Labor Statistics. For every 100 million work hours, approximately 1,000 workers suffer a welding-related injury. That’s 100 times worse than the average injury rate for all other workers, making welding safety all that more important.
Because welding is such a dangerous activity, there’s a lot to learn about protecting workers from its dangers. We’re going to look at both the hazards of welding and how to protect workers from its dangers.
Which OSHA Standards Deal with Welding?
The Occupational Safety and Health Administration (OSHA) provides multiple standards for welding, cutting, and brazing. 29 CFR 1910 provides guidance for general industry. 29 CFR 1915 provides guidance for the maritime industry. 29 CFR 1926 provides guidance for the construction industry.
In general, the standards provide guidance on personal protective equipment (PPE) and protecting the surrounding workspace from fire. There are also specific standards for different types of welding, depending on the industry.
General industry
· Oxygen fuel gas welding and cutting (29 CFR 1910.253)
· Arc welding and cutting (29 CFR 1910.254)
· Resistance welding (29 CFR 1910.255)
Maritime industry
· Gas welding and cutting (29 CFR 1915.55)
· Arc welding and cutting (29 CFR 1915.56)
Construction industry
· Gas welding and cutting (29 CFR 1926.350)
· Arc welding and cutting (29 CFR 1926.351)
Welders and supervisors should inspect each work site for potential hazards and develop a plan to ensure the safety of the welder and surrounding workers in nearby areas.
What Hazards Do Welders Encounter?
The greatest hazard that welders must deal with is fire. Fire prevention is key to maintaining safe operation of welding machines. Hot work, which includes welding, requires that all combustible materials be removed from the welding environment prior to work beginning. If all combustible materials cannot be removed, they must be protected from flame or sparks. Workers must also ensure that their equipment and personal effects, like clothing and gas cylinders, are protected from fire.
Another hazard is the potential for dangerous chemicals to off-gas during the welding work. OSHA provides specific instructions on dealing with the potential for off-gassing while working with chromium and cadmium. When working with these metals, welders must have the appropriate respiratory protection.
It’s also possible that welders may suffer from cuts, eye damage, burns, or crushed extremities. The best way to protect workers is to wear the required PPE.
Welders are also susceptible to electric shock. The most common type is from an arc welding circuit, which ranges from 20 to 100 volts. Shocks of 50 volts or less can be enough to injure or kill a worker depending on the conditions.
What PPE is Required for Welding?
OSHA Standard 1910 Subpart I details the requirements for personal protective equipment or PPE for welding operations. Employers are required to provide effective PPE that includes face and eye protection, hearing protection, and head, foot, and hand protection. Employers are also required to take safety precautions to ensure that the area is free from toxic welding fumes, which may involve providing suction to remove hazardous air or ensuring adequate ventilation.
Welders are required to wear eye and face protection to prevent eye injuries. Welder’s flash is a common condition caused by exposure to intense UV radiation. It can result in temporary blindness and extreme eye discomfort. Typical safety glasses won’t provide enough protection. Welder’s helmets protect workers from light radiation and are graded by the amount they allow to pass through. Helmets are rated on a sliding scale using what is called a DIN rating. The higher the number, the darker the filter. Workers are allowed to choose the shading rating based on the type of work they are performing. In addition, helmets protect welders from flying particles, hot metal, and chemical vapors. Today’s helmets are made out of lighter materials and are more comfortable to wear. This helps reduce fatigue and soreness that may lead workers to not wear them.
Most welders will use earplugs because they do not interfere with other PPE they are required to wear. Today’s ear protection devices provide significant protection while being comfortable to wear.
Foot protection must be provided as defined by ASTM F-2412-2005 and ASTM F-2413-2005, ANSI Z41-1999, or ANSI Z41-1991. It must protect workers from injury due to falling or rolling objects, static discharge, and electric shock. Note that safety toe caps, which are considered necessary for most welding work, are mentioned in the ASTM standards that OSHA refers to.
Leather welding gloves, welding jackets, and cotton sleeves are also required by OSHA’s general construction PPE requirements.
What Does a Safe Welding Area Look Like?
A safe welding area is designed to protect the surrounding environment and the worker from fire and dangerous heat and fumes. With this in mind, all flammable materials should be removed from the area, if possible. If this is not possible, then guards shall be used to protect those materials. Workers should wear the appropriate PPE to protect them from flying sparks and light radiation. Workers should also wear a mask or respirator if there is the potential for hazardous welding fumes.
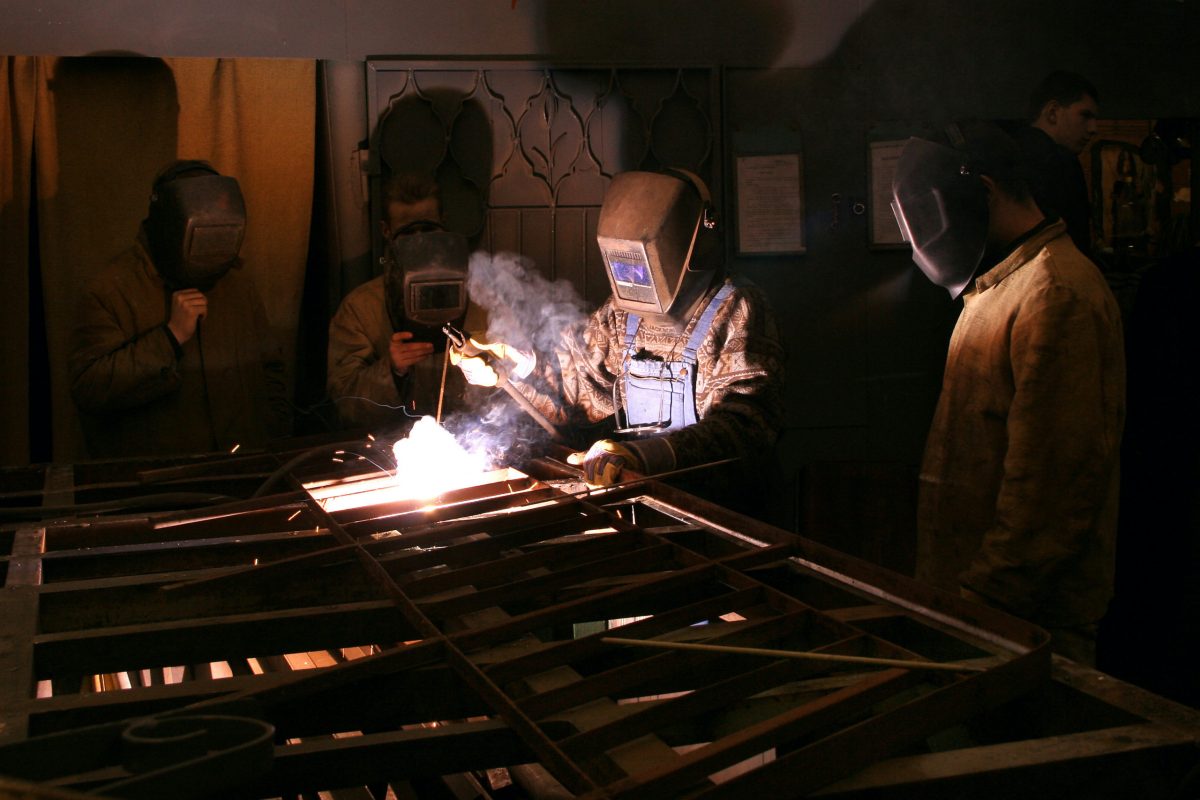
What are the Top Safety Tips for Welders?
1. Know your equipment
Be sure to read the operating manual and safety data for the welding equipment you will be using. It contains important safety information as well as guidance to maximize its performance. Know the safety practices and PPE requirements for the work you’re performing.
2. Ensure local exhaust ventilation
Local exhaust ventilation (LEV) is an engineering control that reduces exposure to airborne contaminants. LEV intercepts the emission at the source and transfers contiminants away from the area where work is performed. LEV can include a hood, ducting, an air mover, and the point of exhaust.
If you are unsure whether a hazardous atmosphere exists, conduct an exposure assessment.
3. Secure clothing
Sparks and other debris can become caught in open pockets, shirt cuffs, or pants pockets. Be sure to button up shirt collars, cuffs, and pockets to prevent catching sparks, and cover exposed skin.
4. Wear the proper clothing
Don’t wear shorts or short-sleeved shirts. Wear only flame-resistant clothing with the proper PPE.
5. Use a respirator when needed
When working in confined spaces or with certain materials, toxic fumes may accumulate. An exhaust hood can help remove fumes from the area. Respirators may be required when working with certain materials or in certain environments.
6. Wear the proper helmet
Make sure your welding helmet fits properly and provides enough shade to protect you from light radiation. Auto darkening helmets are available with sensors that change the shade in a fraction of a second. These helmets must meet ANSI Z87.1-2003.
What are Real Examples of Welding Safety Violations?
A Connecticut-based contractor was fined over $167,000 for failing to make corrections from a previous inspection. Violations included failing to provide welding screens, not having suitable fire extinguishers available, not providing workers with adequate training on hazardous chemicals in their work area, providing a guardrail, and installing safety guards on machinery. The company was also fined for blocking access to electrical panels.
A Florida tank manufacturer was fined $106,100 for 23 safety and health violations. These violations included exposing employees to toxic chromium fumes. Chromium is known to cause cancer, and it targets the respiratory system, kidneys, liver, skin, and eyes. Workers were exposed to chromium levels above the eight-hour exposure limit set by OSHA (5 micrograms per cubic meter of air over an eight-hour shift). The company also failed to provide medical surveillance and appropriate respirators, and failed to protect nearby workers from ultraviolet welding arcs.
In Mississippi, two temporary workers were involved in a lethal blast caused by ignition of methane and hydrogen sulfide gasses. One of the workers died, while the other was injured with a fractured skull, internal injuries, and broken bones. The workers did not receive training that would allow them to know that the storage tank beneath them contained explosive gasses. Four different companies were cited for various violations from failing to train workers to not providing the required protection when welding.
Promote Welding Safety with a Smarter Safety Program
In order to avoid OSHA violations and keep workers safe, employers and safety managers must provide proper training and PPE. Tracking this training and the use of PPE will help keep workers safe and prevent potential violations and fines.
Safesite can help you maintain the safety records needed to show you are in compliance with safety requirements. For example, our hot work and welding inspection template can help you track the safety of the welding environment. If problems are found, they can be quickly communicated to the appropriate parties for remediation to keep your production on schedule.You can learn more with our free app for managing and maintaining your PPE and equipment.