No one thinks a fall accident will occur until it does. In fact, fall protection was the most-cited standard enforced by OSHA in 2019, and falls remain the leading cause of death in construction workplaces.
Fall hazards can’t be ignored — even when it’s crunch time. A robust fall protection program not only safeguards your employees, but it also bolsters your financial health by preventing costly claims and legal issues.
The Most Common Workplace Fall Incidents
The construction industry leads the way in the most fall-related injuries in the workplace. In fact, construction workers are seven times more likely to have a fatal fall than any other industry. But that doesn’t mean other industries are immune. Ladder-related injuries are all too common across all industries.
Falls usually happen due to the following reasons:
- Inadequate safety equipment
- Improper behavior/use of equipment
- Failure to use safe procedures
- Neglecting safety measures during projects
It’s essential to identify the weaknesses in your current fall protection program so that you may create a more reliable plan to avoid these issues.
Falls Are Completely Preventable
The good news is that falls in the workplace are entirely preventable. By using a few safety precautions and ensuring that equipment is up to standard, you will solve a ton of issues.
Keep the following worker guidelines in mind:
- Wear proper slip-resistant shoes when on a ladder or scaffolding
- Determine what safety equipment should be used before the project begins
- Avoid leaning or reaching while on ladders or scaffolds
- Make sure that the work area is hazard-free at all times
- Notify management or another responsible party if a hazard is identified
- Use proper equipment and follow the directions for proper use
- Check all equipment before use
Preview the Fall Prevention Checklist Template >
A quality fall protection plan will help you avoid an issue in the future. Knowing your current problems, such as outdated equipment or inadequate training, will help you start the process of strengthening or creating your new fall protection plan.
Understanding Fall Protection Standards
You may feel your fall protection training plan has few gaps, if any. It is important to understand the nuances of your governing fall protection standards. Many companies overlook critical areas regarding damaged equipment and a cultural push toward safe work at heights to prevent shortcuts when no one’s watching.
OSHA fall protection standards comprise the basic requirements US companies must meet for all employees, including temporary and contract.
State plans incorporate these standards as a minimum, so your governing body may have more stringent requirements. We’ve condensed the standards down into key takeaways and highlighted points.
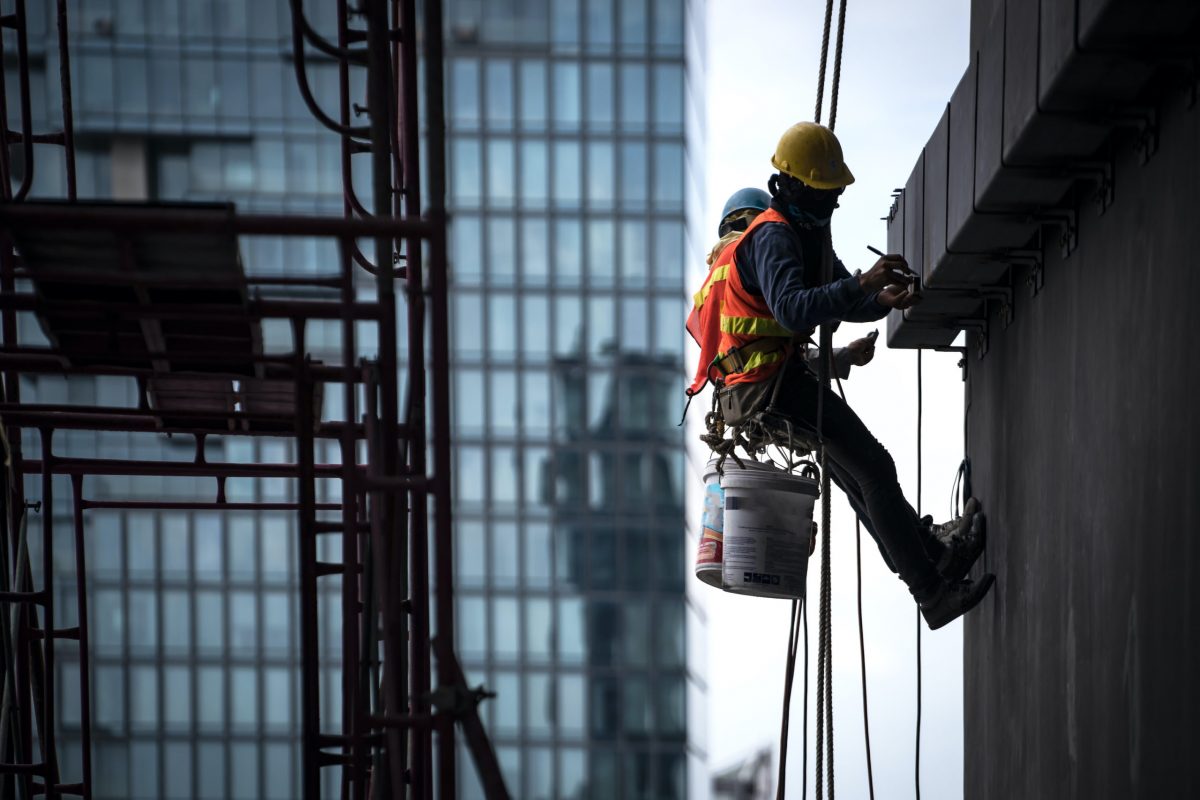
General Industry Fall Standard – 29 CFR 1910.28
The standard outlines essential fall protection requirements for employees. These guidelines focus on the employer’s requirement to provide adequate protection for all employees who are exposed to falls and falling object hazards in the workplace.
Construction Fall Standard – 29 CFR 1926.501-502
This is the foundational standard for fall protection in construction. The standard includes information about proper durability of working and walking surfaces that can hold the capacity of the employee’s weight, utilizing proper fall protection when the employee is working with unprotected edges, and other specifics regarding minimum fall protection standards that should be in place at every worksite.
ANSI A10.32
This standard establishes performance criteria for personal fall protection equipment in use in construction and demolition workplaces. Additionally, this guideline provides specific information regarding the proper inspection of the equipment.
Evaluating these standards are an excellent place to start when managing fall protection programs at your place of business. At the bare minimum, your current program should include these guidelines as well as any additional requirements that may be specific to your business.
Fall Protection Selection and Evaluation
Then next phase is identifying the threat in your workplace and understanding what type of fall protection equipment and training that you should put in place.
When it comes to establishing proper fall protection policies, it’s best to start with the hierarchy of controls that can assist with this process. If possible, completely remove the fall threat risk.
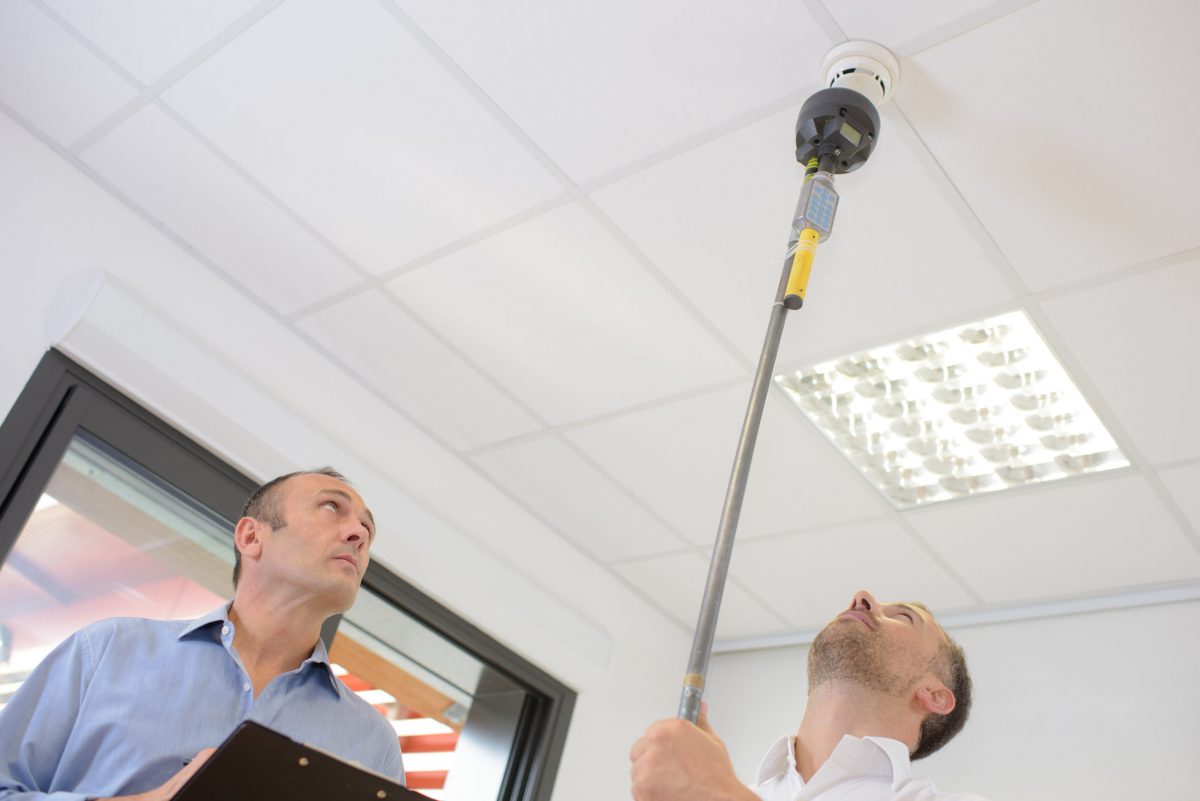
This may mean structural changes are necessary in order to remove the threat completely. You may be able to address this via administrative controls, policies, procedures, or work instructions. However, if the fall hazard cannot be removed, then a fall arrest system may have to be put in place.
The Difference Between Fall Restraint and Fall Arrest
You may hear the terms “fall restraint” and “fall arrest” used interchangeably by individuals outside of the industry. However, they are not the same thing. A fall restraint should be used when working near the leading edges of rooflines and from aerial lifts.
Although both systems use a harness to secure the worker, a fall restraint system uses a positioning lanyard that prevents the worker from getting too close to the roofline or too close to the edge of the man basket. To be clear, a fall arrest is a system that is used to stop a person who is actively falling. You may need to employ both fall restraint and fall arrest systems depending on the specifics of the project and workplace.
Understanding the Components of Fall Arrest Systems
In order to properly use a fall arrest system, you must also understand anchorage points requirements. For instance, all fall arrest systems require an anchorage point certified capable of supporting at least 5,000 pounds per worker attached or two times the maximum arrest force in an engineered system designed by a qualified person.
A lanyard is the part of a fall arrest system that prevents a person from getting too close to the edge of the working platform. Lanyards are designed to support a free fall of 6 feet. Because of this, ensure anchorage points are located overhead and are NOT located below the worker. You should be mindful of the amount of swing action capability of a fall arrest system. Too much swing could cause the individual to hit hazardous objects and sustain serious injuries.
Fall Protection Equipment Inspections & Documentation
Incorporate systems for caring for and inspecting fall protection equipment. There are a variety of equipment types that fall into the fall protection category. Commonly used are:
- Lanyards
- Harnesses
- Lifelines
- Hardware
However, simply acquiring this safety equipment and a short training session is not enough to ensure fall protection. It is essential to inspect the equipment thoroughly before each use.
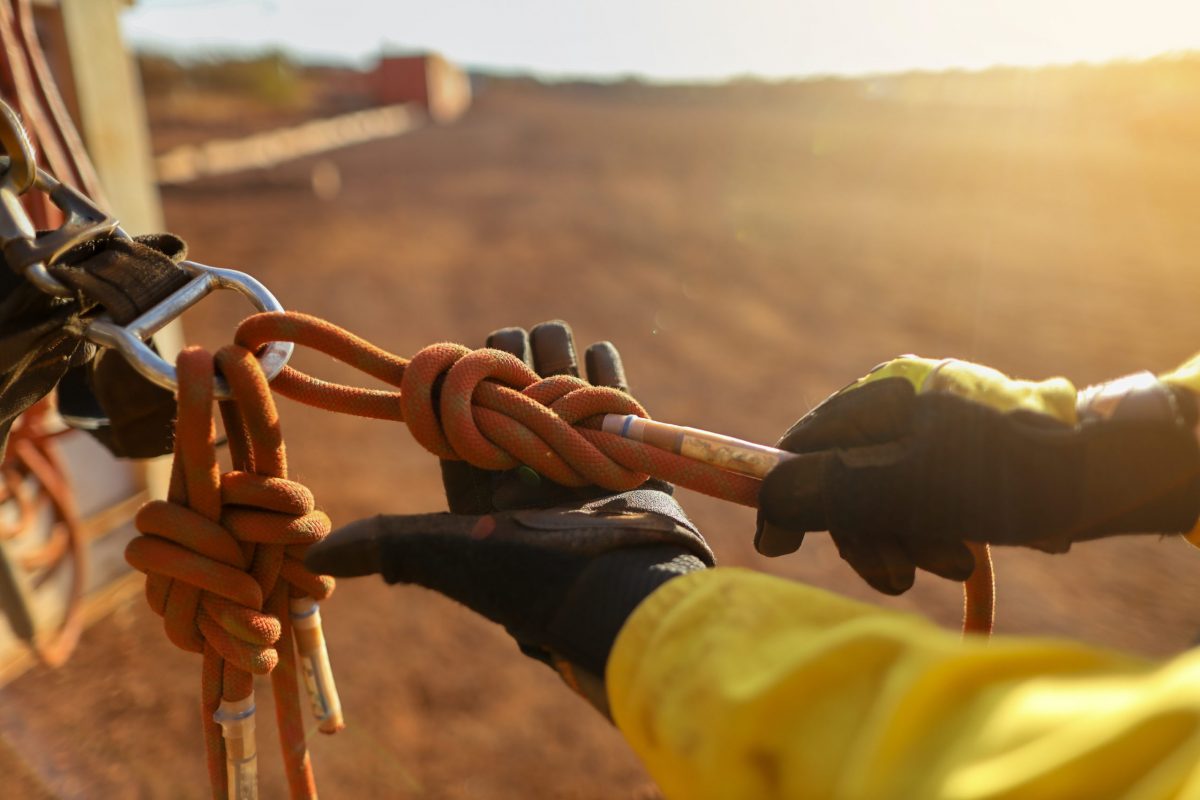
Create a dedicated inspection checklist for employees to consult. It is also important to create a new-employee training plan to ensure that each employee has a clear understanding of how to use the equipment and how to identify issues or concerns.
At the bare minimum, fall protection equipment and components inspection should be conducted annually. The inspection should be conducted by a person who has a thorough knowledge of equipment and can readily identify any problems.
However, it is best practice to complete routine inspections more often and with consistent documentation. To streamline the process and to create transparency and consistency, the equipment inspection checklists can be created and maintained with Safesite. This allows you to track your inspections and observations, raise hazards, and identify any trends that may help them remedy fall protection safety concerns.
Managing Fall Protection Training
Your fall protection plan must include a training program. In order to establish a quality fall protection training, you should adhere to the following guidelines:
- Train new employees about the fall protection plan, and offer training if the program changes or if there are significant changes in the plan such as the type of equipment used or if new OSHA guidelines are published.
- Consider making fall protection training an annual requirement for all employees.
- During training, ensure that employees understand the proper use of equipment via demonstration. Require that employees demonstrate the proper way to inspect, wear, adjust, and remove safety equipment.
- Provide live, personal fall arrest demonstrations. Many PPE suppliers and harness manufacturers provide this service. Consider consulting with their services to include in your worksite safety training.
Not only can employees learn a lot about fall protection via these annual training sessions, but the company can also identify and adjust any training requirements. Use Safesite to track training and identify gaps in employee understanding of your policies. Not only does it benefit you as the safety manager, but OSHA mandates a proper record as well.
What Level of Training Should You Employees Have?
Fall protection training can be classified into four categories: awareness, authorized-user, competent person, and qualified-person training. Every employee may not need the same level of fall protection training, but every employee can benefit from minimizing fall hazards.
Awareness Training
Awareness training is essentially an overview of fall hazards in the workplace. It is a more general and basic approach to understanding fall risk, and many professionals do not consider this an adequate training level for most employees.
Authorized-User Training
Authorized-user training is more job-specific training for individuals who need to understand fall protection for their regular on-the-job activities. This training will ensure that individuals know and understand OSHA standards and teach them how to be in compliance with those standards.
Competent Person Training
Competent person training is geared more toward supervisory-level roles. This training ensures that individuals have an understanding of all types of fall hazards in the workplace as well as appropriate measures for protection. This type of training would prepare an individual for how to suggest changes or additional training in the event that a new fall hazard presents itself.
Qualified Person Training
Qualified person training is the highest level of fall protection training available. It usually requires that the person possess a higher-level degree or specialized training. Ultimately, this person would be able to address technical issues that may arise. It is up to the employer to do their due diligence to identify if an employee is considered a qualified person.
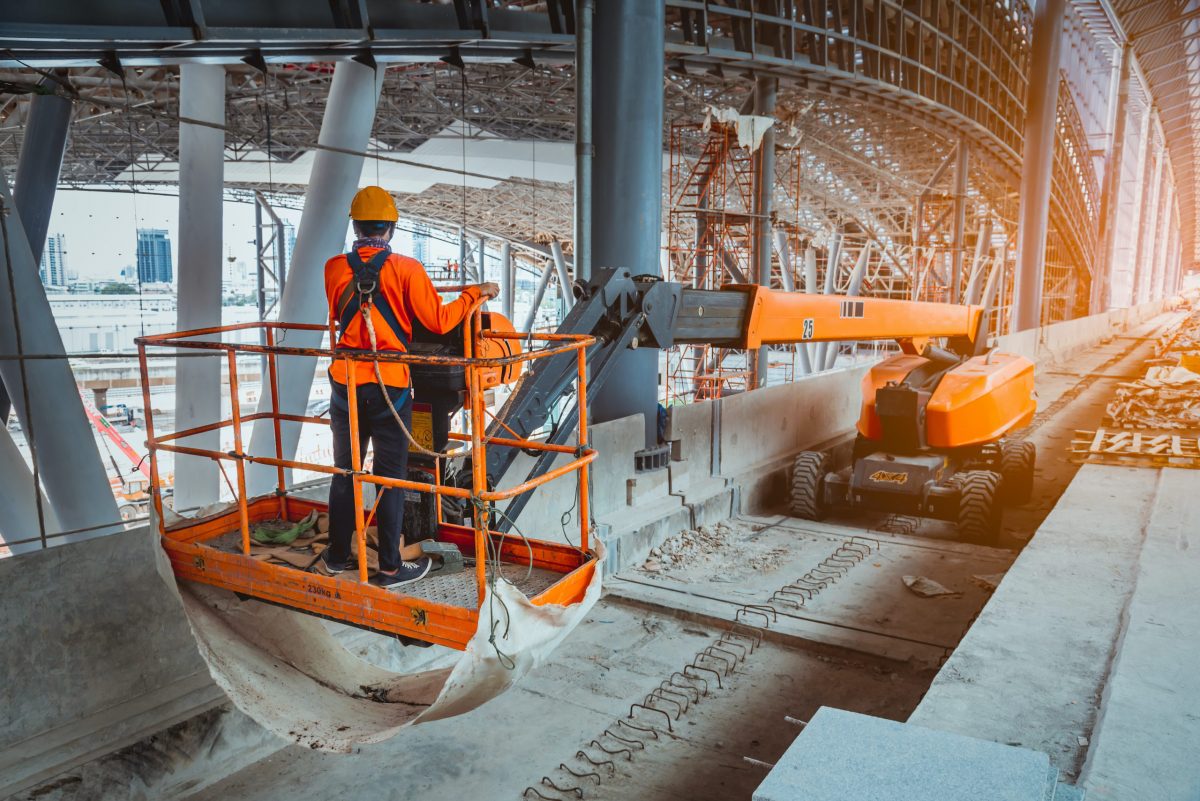
How to Choose a Trainer
A company must do its due diligence to find a reputable fall protection trainer. You should rely on certifications, reputation, and the course overview to help you identify which trainer is most likely to reach your needs. You can rely on internet searches or peers in the industry to direct you toward the top trainer professionals. Make sure that there is a measurable outcome for the training and that it matches up well with your company’s goals.
Other considerations to keep in mind:
- The trainer should have adequate experience and proper training.
- There should be an on-the-site training, or a facility larger enough to have hands-on training experiences.
- The student-to-instructor ratio should be kept low for better learning experiences.
- Hands-on practice should be a requirement for the training experience.
Overall, you should evaluate the experience for your employees and consider how well the training will prepare your employees for avoiding, identifying, and remedying fall hazards in the workplace. Students should leave the training program with a thorough understanding of fall protection and more confidence in their abilities.
The Bottom Line in Fall Prevention
Due to the fast-changing nature of business today, it’s likely your fall protection program could use some updates. Don’t wait. Do it now to identify any weaknesses in your current fall protection plan and employ proper changes to ensure the health and safety of permanent, temporary, and contract employees.
Outsmart fall risk by unifying your training, equipment selection, audit, and documentation efforts toward one purpose: creating company-wide engagement in fall protection.