According to the CDC, tens of millions of workers are potentially exposed every year to damaging noise. Hearing loss is a preventable condition, and employers are responsible for providing hearing protection to workers to safeguard from overexposure.
The threshold for providing hearing protection for workers is 85 decibels (dB). If you need to raise your voice to speak to someone 3 feet away, the noise may be over the threshold. Noise may be a problem in the workplace if you experience ringing or humming in your ears, have to shout to be heard, or experience temporary hearing loss after leaving work. To measure noise in a work environment, employers can use a calibrated sound level meter (SLM). And to measure noise exposure on the individual level, an employer can provide a worker with a personal noise dosimeter.
If your workers are exposed to elevated noise levels, you have a responsibility to protect them from overexposure. This article provides information on the requirements for hearing protection in the workplace.
What Are the OSHA Standards for Occupational Noise Exposure?
OSHA standard 1910.95 deals with occupational noise exposure. It states that employers must provide noise protection for their employees when sounds are above an average of 85 dB per eight hours. Note that if sounds are above 85 dB for less than eight hours, noise protection may be required. For example, exposure to a sound level of 100 dB only needs to occur for two hours to reach the hearing protection threshold. Employers are to start with administrative and engineering controls before using personal protective equipment (PPE), such as earplugs and earmuffs.
Employers whose employees deal with loud noise exposure must create and administer a hearing conservation program per standard 1910.95(c). The program must include sound monitoring, employee notification of monitoring results, and audiometric testing of employees. Testing includes a baseline test and annual testing to determine if the employee has suffered any impairment or loss.
For help assessing your workplace and determining the proper PPE, check out our inspection template. It will help you identify potential hazards and select the appropriate equipment to protect workers.
Supervisors can use a toolbox safety talk on hearing protection to help employees take ownership of their hearing and know when to use hearing protection.
Who Should Wear Hearing Protection?
Any worker exposed to more than 85 dB on average over an eight-hour period should wear hearing protection. This also includes anyone with current hearing loss or impairment. Employers need to offer their employees a variety of hearing protection devices (HPDs) and allow employees to select what works best for them.
The employer must also provide annual training in the use and care of all HPDs. The training includes information about the effects of noise on hearing, the variety of HPDs available (including advantages and disadvantages of each), care and use of HPDs, and the purpose and explanation of audiometric testing.
What are the Qualities of Effective Hearing Protection?
Hearing protection devices are designed to reduce the level of sound reaching the eardrum to below 85 dB. HPDs are used when engineering and administrative controls don’t work or aren’t feasible. They should be the last resort to protect a worker’s hearing.
Engineering controls modify the equipment to reduce noise. Administrative controls reduce worker exposure by reducing work hours or the amount of time a particular piece of equipment can be used.
All hearing protection devices are rated for the amount of noise reduction they offer. This rating is called the noise reduction rating or NRR. It is based on the real-ear attenuation at threshold (REAT) method of testing, as described in ANSI S3.19-1974. However, these ratings have been shown to differ in the real world as opposed to in the laboratory where the measurements are taken. OSHA recommends that all noise reduction ratings should be reduced by 50%. NIOSH recommends reducing the NRR by the factors below:
- Earmuffs—less 25%
- Formable earplugs—less 50%
- All other earplugs—less 75%
For example, if a formable earplug claims to reduce noise by 32 dB, the real reduction is closer to 16 dB. These adjustments should be applied to all HPDs.
Noise-canceling headphones and earbuds and Bluetooth hearing protectors are not effective hearing protection. They are designed to block ambient sounds using noise control for low-frequency sounds and soundproofing for higher frequency sounds. They only provide soundproofing and are not effective for controlling occupational noise exposure.
What are the Types of Noise Protection?
There are three types of hearing protection: earmuffs, earplugs, and ear canal caps (also called semi-inserts).
Hearing protection earmuffs are designed to be worn outside the ears and provide the best noise protection. Muffs are made with sound-attenuating material and soft cushions, and are held together with a headband.
Earplugs are designed to be worn inside the ears and are available in formable and non-formable varieties. Many of these foam earplugs are disposable or reusable. Plugs made from plastic or silicone are also available. Custom-molded earplugs are available and can be purchased from an audiologist or other hearing professional.
Ear canal caps are not designed to be inserted fully into the ear. They stay in place just over the ear canal by a rigid headband connecting the earplugs. They are not custom-made and do not always work for everyone. Because ear canal caps (semi-inserts) do not extend into the ear canal, they do not offer as much hearing protection. However, they are useful for situations that require taking hearing protection on and off on a frequent basis.
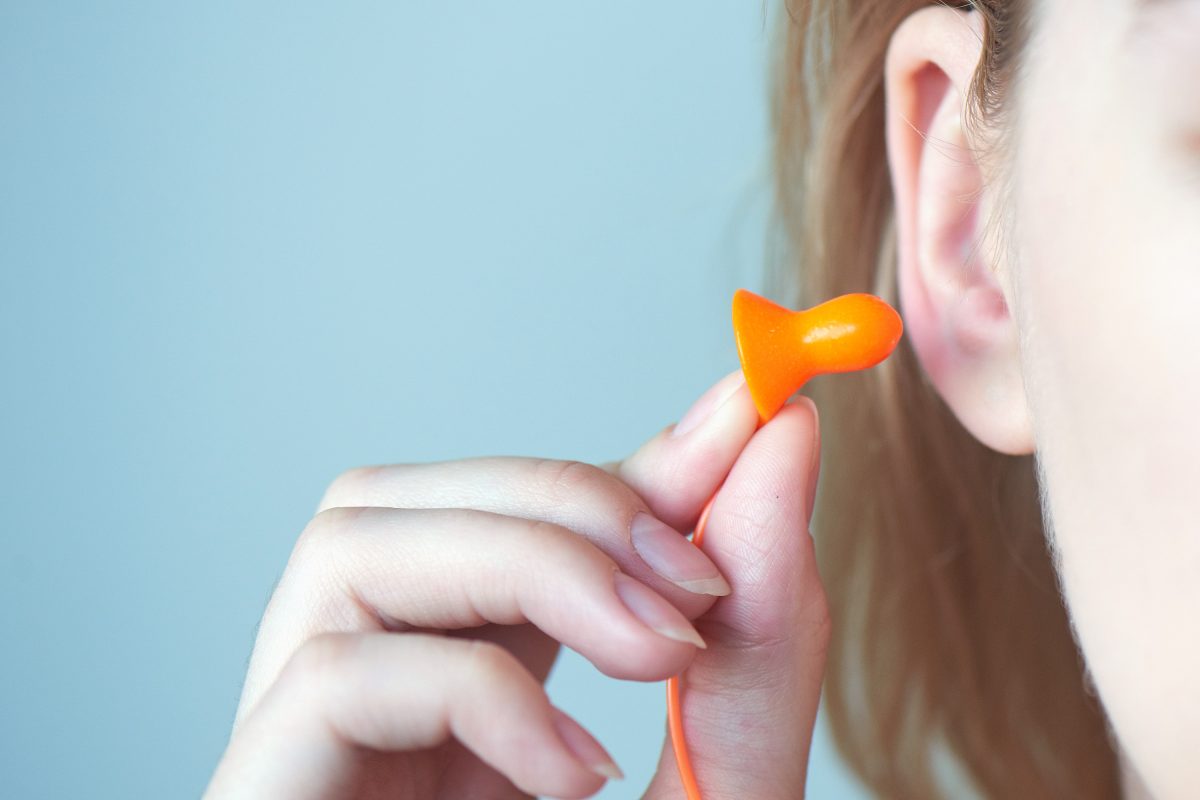
Selecting the Right Hearing Protection for the Job
Other than removal of hazardous noise from the workplace, the most effective hearing protection is one that a worker will wear willingly and consistently. If hearing protection is not worn, workers are susceptible to occupational noise exposure, which can cause hearing loss or impairment.
In order to properly protect workers’ hearing, ear protection must be worn correctly, fitted properly, and be appropriate for the noise. Allowing workers to select their own hearing protection device will help ensure that it is properly used when necessary. It may take experimentation to find the best device for the environment and worker use.
According to the American Industrial Hygiene Association, the following factors improve worker acceptance of hearing protection and increase the likelihood that workers will wear them consistently:
- Convenience and availability
- Belief that the device can be worn correctly
- Belief that the device will prevent hearing loss
- Belief that the device will not impair a worker’s ability to hear important sounds
- Comfort
- Adequate noise reduction
- Ease of fit
- Compatibility with other PPE
Source: American Industrial Hygiene Association
Manage Your Hearing Protection and All PPE
Your employees’ hearing and safety depend on the inspection and management of PPE, including hearing protection devices. As a safety coordinator or safety manager, it’s imperative that you help your workers protect themselves from loud or extreme noises.
You can help your employees stay engaged in safety by adopting a digital process for managing and maintaining equipment. This process allows you to schedule equipment inspections and send automated alerts to employees to help enhance your safety program.
Learn more about our free app for managing and maintaining your PPE equipment as part of a total safety management solution.