Your lock-tag-try (LOTO) process helps ensure that workers stay safe when around hazardous energy. More importantly, it safeguards workers from severe, debilitating, or deadly injury. A major component of implementing your LOTO process is creating a comprehensive and effective written policy.
Thankfully, if you’re looking to create a new LOTO policy, you don’t have to start from scratch. The following steps will guide you through editing a LOTO policy template document that is suitable for your needs.
LOTO Policy Template
Grab a LOTO policy template to have on hand as you read through the steps below. A good template includes a framework of regulatory requirements and general best practices.
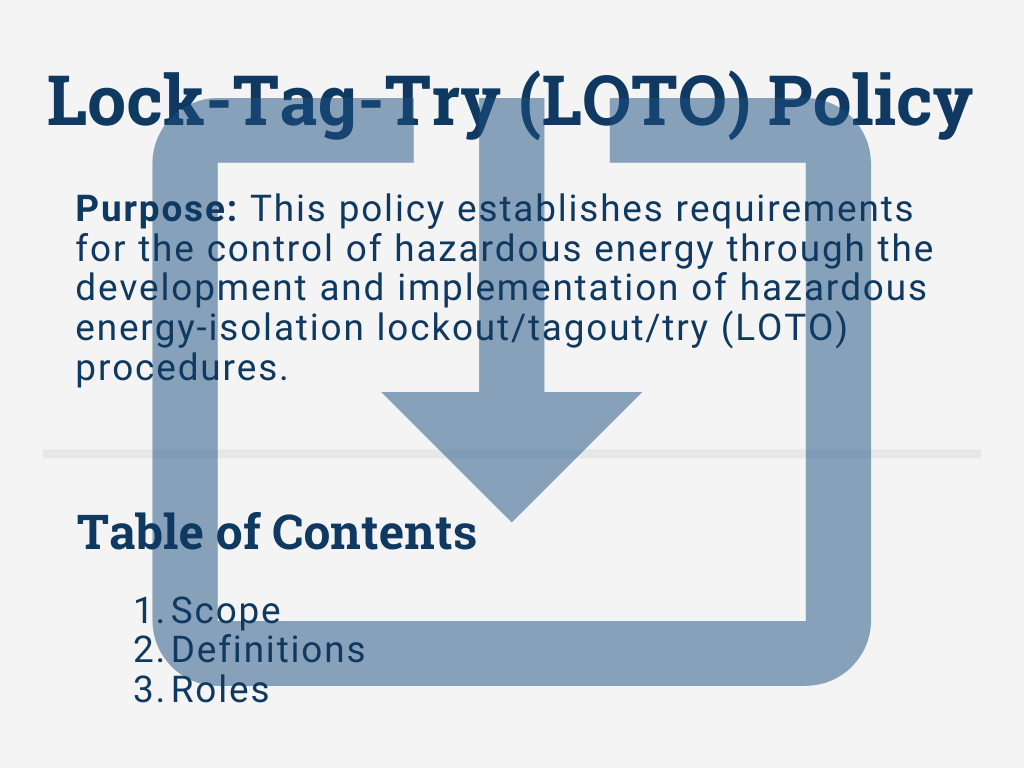
Edit your template to accurately reflect your company’s specific procedures.
State the Purpose of the Policy
As you develop your LOTO policy, it helps to keep in mind what LOTO is and why it’s so important — its Purpose. It’s imperative to then pass along that information to workers so they understand why they have to follow these procedures.
As you know, lockout/tagout or lock-tag-try is the manner in which a company makes sure that machinery and equipment that are powered by hazardous energy are shut down properly so they can be serviced and undergo regular maintenance.
When it’s not respected and properly cared for, hazardous energy can seriously injure or kill workers and other bystanders. According to OSHA, LOTO procedures prevent 120 deaths and nearly 50,000 injuries each year.
The introduction of your policy should include language that explains why LOTO is necessary for safety and why all employees should take it seriously. This section will also explain how the written policy will accomplish the goals of lockout/tagout.
Define Who and What the Policy Covers
OSHA sets most of the LOTO standards that US companies follow. Some companies may also follow voluntary standards from organizations like the National Safety Council. These standards provide guidance on who your LOTO policy should cover and what is required in the way of processes.
This section of the company LOTO policy, sometimes called Scope or Policy, should provide details on how OSHA and voluntary standards apply to your company and the steps you take to comply with them.
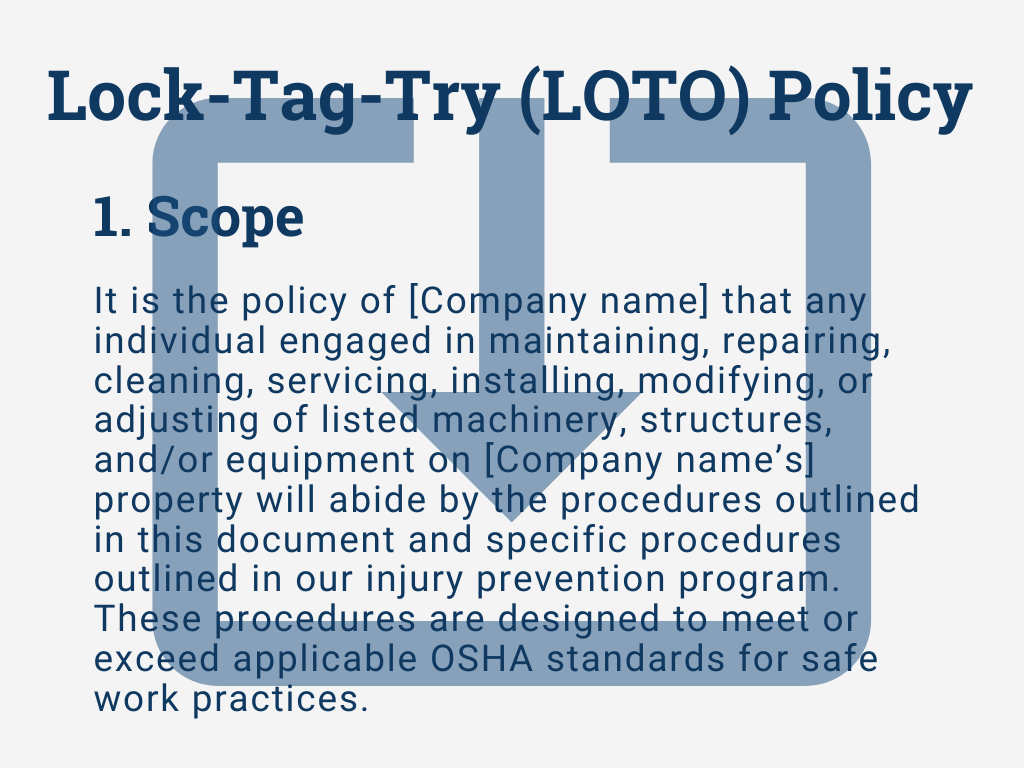
The Scope should also list what pieces of equipment or types of machinery need LOTO, as well as when LOTO should be utilized. It should also clearly define who in the company needs to follow the LOTO procedures. Some policies also lay out when LOTO does not apply.
If your company has numerous pieces of equipment that need LOTO or a variety of different types of machinery utilizing LOTO, be as specific as possible, naming each type of equipment. Otherwise, more general wording that covers in-kind machinery is acceptable.
Provide Definitions for Common LOTO Terms
It’s important that company stakeholders reviewing your policy can understand it on a basic level. Provide a Glossary or Definitions section to explain what different LOTO terms mean for HR and policy teams that aren’t as familiar with safety processes.
Some common LOTO terms that could be defined in the policy include authorized worker, affected worker, lock, tag, energy control procedures, hazardous energy, and energization.
If you work from a glossary template, be sure to add terms specific to your industry. In its LOTO policy documents, for example, BP defines terms that apply to the pipeline industry such as double block and bleed, operating pressure, and single valve isolation.
Describe Responsibilities and Roles
The Scope or Policy section tells who must follow the LOTO procedures, but it’s important to explain those responsibilities in greater detail. The Responsibilities section doesn’t have to list each individual role but can group responsibilities by job types. Some common groupings include:
- Department chairs/directors/CEOs
- Managers/supervisors/team leads
- Authorized workers/employees
- Affected workers
- Safety team
Responsibilities can be spelled out in detail or can be more general; both have their benefits. Providing lots of detail assures that there are not any questions and everything gets covered. Being more general means fewer edits and reprints when policies and procedures change or when positions shift.
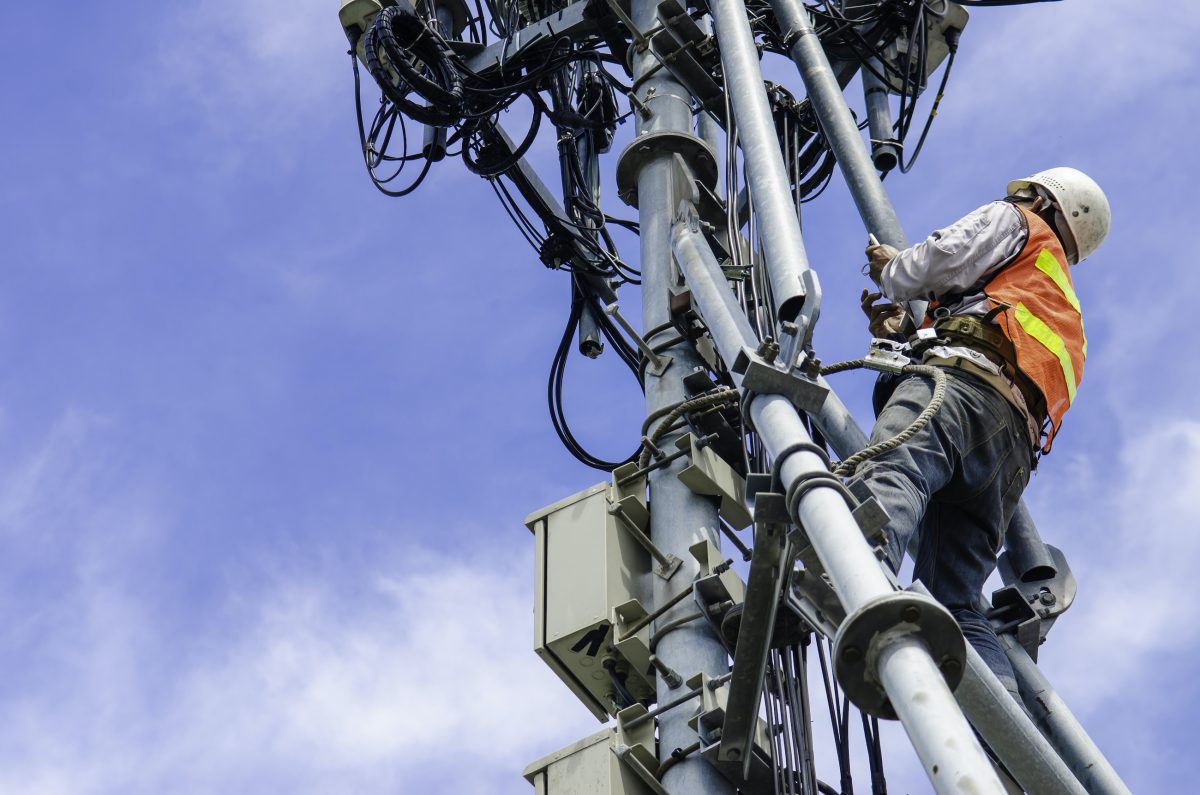
Here are some examples for different job types:
- Department chairs/directors/CEOs: implement LOTO policy, provide funding for LOTO policy, set up LOTO training
- Managers/supervisors/team leads: issue and maintain LOTO equipment to workers, oversees LOTO policy, audit LOTO procedures, ensure all workers understand their roles in LOTO procedures
- Authorized workers/employees: safely follow the LOTO procedures, inform supervisors of any issues with the LOTO process
Explain the Lockout/Tagout Process in Detail
The next section of the LOTO policy should provide detailed step-by-step instructions for the LOTO Procedures.
While the exact lock-tag-try procedure will look different for every company, a typical procedure follows these steps:
- Prepare for shutdown. This includes making sure the correct equipment has been identified for LOTO.
- Notify employees, alerting any workers who use or will be around that machine that will be locked out. Let workers know how long the work is expected to take and when the machine will be available again for use.
- Shut down the machine following the specific and detailed instructions provided by the employer.
- Disconnect or isolate the machine from its energy source or sources, including electricity, steam, water, gas, compressed air, and others.
- Release or restrain any stored or residual hazardous energy. This can include trapped heat in a thermal system, excess fumes, or tension in a spring assembly.
- Apply the lockout and/or tagout devices.
- Verify that all the steps were completed and the machine is safe. Try starting the equipment to be sure the lockout is working.
After service or maintenance, employees should follow a sequence of steps to put the machine back into use. Only the authorized employee who applied the LOTO devices may remove them. Sample steps for removing lockout/tagout equipment:
- Inspect the machinery or equipment to make sure that it is still intact and the area is clear.
- Make sure everyone is away from the machines and once they remove the device, be sure that any workers that use that machine know that the lockout/tagout devices have been removed.
If you use tagout procedures in place of or alongside lockout procedures, include specific instructions for tagout procedures.
Other procedures that may be applicable to you include:
- Spending stored energy
- Maintenance by outside contractors
- Group LOTO
- Temporary removal
- Maintenance with undisrupted energy
Regardless of the steps your policy includes, it’s important that the employees follow each of the steps exactly and in order. Include your enforcement policy (or list where it can be found) so that employees understand how you will deal with violations.
Training and Other Program Processes
Your LOTO policy should also provide details on the training required for each role, and the records required to document your training.
Inspections are another important process you’ll want to include. Specify which inspections are current for each type of equipment, where they can be found, and where to store the records of completed inspections and corrective actions.
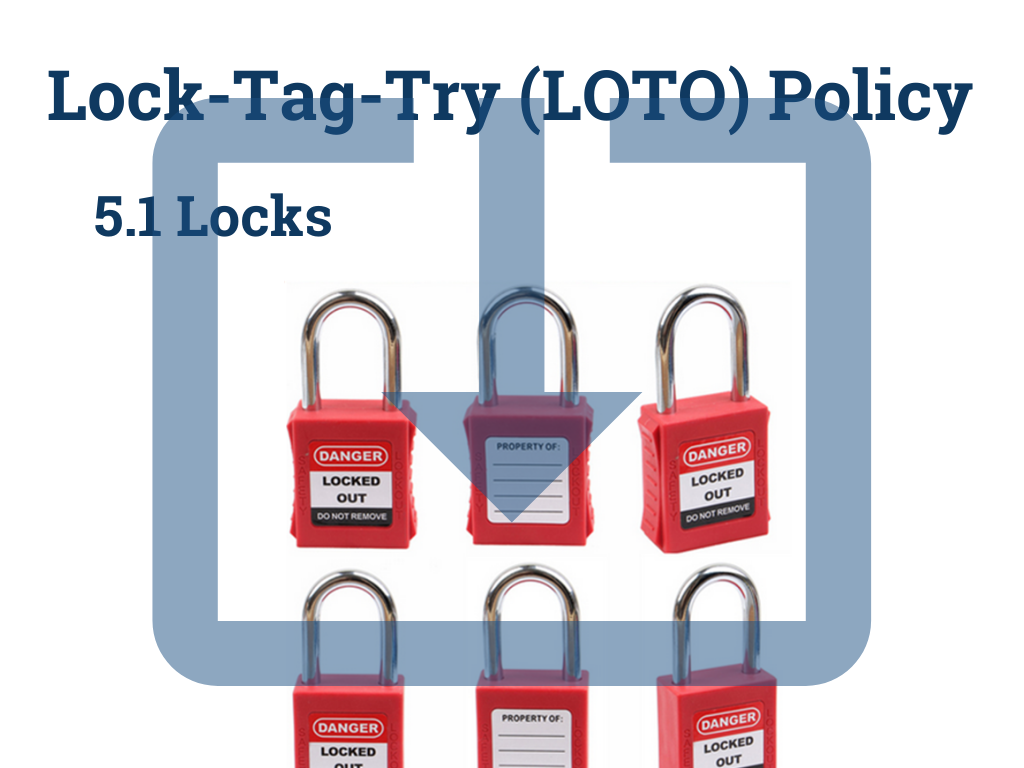
It may also be beneficial to include photos, charts, and diagrams in your written policy. These may include:
- Photos of lockout/tagout equipment
- Diagrams or photos showing proper usage of energy control devices
- Photos, names, and contact info of authorized and affected workers
- Photo and ID # of all pieces of equipment that require lockout/tagout
Finally, list your emergency contacts and procedures.
Make Your Policy Known
Once your LOTO policy template is edited to include your hazardous energy sources, be sure that every employee involved in the LOTO procedures receives a copy in their first language. It is also helpful to have printed copies easily available near the applicable equipment.
Creating a written LOTO policy is crucial to successfully implementing LOTO procedures. Use yours to build a more efficient and unified hazardous energy program.