The purpose of head protection is to safeguard workers from falling debris, low-hanging objects, electrical hazards, or even direct sunlight. Industrial and construction workers generally wear hard hats or safety helmets to protect the head from impact. However, there’s more to protective headwear than just wearing a hard hat or helmet.
Before selecting a hard hat or protective helmet, workers and managers should know the classes and types available and their purpose. We put together this guide to help workers and managers choose appropriate protection before they make a purchase.
What are the Guidelines for Using Head Protection?
Head protection should be used when objects or debris may fall from above, a worker may bump their head against a fixed object, or there are electrical hazards present. These conditions often occur in construction and industrial jobsites. Many of these sites require head protection, even if active hazards aren’t visible.
Head protection safeguards workers from potential head injuries and may be part of the additional personal protective equipment (PPE) required on a jobsite.
Workers should inspect their hard hats or helmets on a regular basis, using a guide like our hard hat inspection template. This will ensure that the protection is in good working order.
What are the Qualities of Good Protective Headwear?
Good head protection should be able to do the following:
- Resist penetration and blows to the head
- Provide a suspension system to absorb impact
- Provide insulation from electrical shocks, when necessary
- Be water resistant and slow burning
- Shield a worker’s scalp, face, neck, and shoulders
What Standards Apply to Head Protection?
OSHA standards 29 CFR 1910.135 and 29 CFR 1926.100 apply to industrial and construction workplaces. Both standards require employers to ensure that workers are provided with head protection that meets the required certification. In both standards the protection must meet standards laid out by the American National Standards Institute in ANSI Z89.1, which provides overall standards for certification of head protection. It provides directions to protection providers on the testing procedures needed to meet certification standards. Hard hats and helmets that comply with the standards are appropriately marked on the inside, to ensure workers that they meet the requirements.
In addition, the ANSI standard classifies the different kinds of hats and helmets according to their use and protection. All hard hats and helmets are marked with the appropriate class and type of protection.
Finally, the standard states that workers should not alter or modify their hard hats or helmets for any purpose, as doing so will limit their reliability.
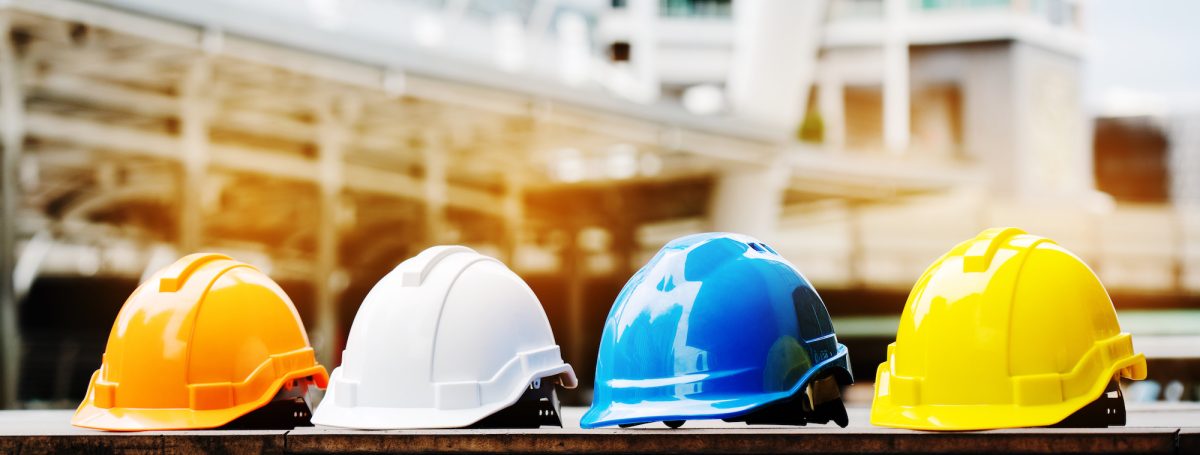
What are the Three Classes of Head Protection?
There are three classes of head protection based on the amount of electrical protection they provide: Class E, Class G, and Class C. Class E (electrical) has been tested to withstand up to 20,000 volts of electricity. Class G (general) has been tested to 2,200 volts. Class C (conductive) offers no electrical protection. Hard hats and helmets are labeled with the appropriate class.
What are the Two Types of Head Protection?
Type I protects the head from impacts to the top, like falling debris or objects.
Type II protects the head from impacts to the top and lateral sections, like bumping into a stationary object.
Hard hats and helmets are labeled with the appropriate type of protection they provide.
Who Should Wear Protective Headgear?
Construction and industrial workers who are subject to hazards from falling debris or objects, bumping into fixed objects, or electrical shock hazards should wear head protection. The class and type will depend on the specific nature of the hazard and where the worker will most likely be hit.
What Hazards Require Head Protection?
While many construction job sites require hard hats as part of the basic PPE to be worn at all times, safety standards require head protection in only a few situations. Protection should be provided when there is:
- Potential falling objects or debris
- Low hanging objects or protruding objects
- Electrical hazards
The type and class of protection will depend on where the worker is working and what potential dangers are around them.
How Do Hard Hats and Safety Helmets Differ?
As protective headgear, hard hats and safety helmets differ by where workers are working when they wear them. Hard hats are worn by workers on the ground subject to potential falling debris or protruding objects. Safety helmets are worn by workers at height who have the potential to fall. Safety helmets are rated and certified the same as hard hats.
Safety helmets and hard hats also look different. Helmets typically sit closer to the head, have built-in chin straps, and little to no brim around the edge. They also have more internal padding to protect the head on impact, and may include attachable visors, ear protection, and be made from high visibility materials. Safety helmets generally offer enhanced protection from lateral impacts over hard hats. Contractors may find that safety helmets are slightly more expensive than hard hats. The higher cost is mainly due to the extra protection for both the top of the head and the side, along with the optional added equipment.
When Should a Company Upgrade Their Head Protection?
Workers should regularly inspect their hard hats and helmets for damage or degradation. This includes not only the helmet or hat surface, but also the suspension system. If damage or degradation is found during this inspection, the hard hat or helmet should be replaced immediately to ensure continued protection. A sample hard hat inspection checklist is available.
When a company or contractor takes on new work with new potential dangers, like electricity, they should review and upgrade their head protection as necessary.
Streamline Management of Head Protection and All PPE
It is critical to ensure that your company is adequately maintaining all PPE, including head protection. For a safety coordinator or safety manager, PPE inspection is just one area of responsibility among a host of tasks. But it’s an area that frequently gets overlooked.
Those responsible for occupational safety find that a digital process for managing and maintaining equipment raises the safety engagement rate. By scheduling equipment inspections, the automated alerts enhance your overall safety program.
Learn more about our free app for managing and maintaining your PPE equipment as part of a total safety management solution.