Ask ten experienced safety professionals what elements they need for an effective safety management program, and you will probably get ten different answers.
In truth, the best safety management program is one that results in the fewest incidents and injuries for your workers. At the same time, the best program is also one that is easy to manage and maintain over a long period. As a bonus, it should also require the smallest investment in person-hours and budget to be effective.
In Part 2 of our Ultimate Guide to Safety Management Systems series, Dave Paoletta presents time-tested approaches to safety management systems that prove effective in a wide variety of industries and companies.
(Did you miss Part 1? Read The Ultimate Guide to Safety Management Systems here.)
What is the Purpose of a Safety Management System?
The purpose of a safety management system is to define and integrate written programs and workplace procedures required by federal, state, and local regulatory authorities, like the Occupational Safety and Health Administration (OSHA), the Environmental Protection Agency (EPA), the local Fire Marshall, and the Air Quality Bureau.
Companies may add additional programs and procedures in cases where they are:
- Industry best-practice
- Required by the company’s insurance underwriters
- Under a union contract
For example, a company may choose to implement the electrical safe work procedures required by NFPA 70E, a consensus standard.
Keeping track of the implementation, training requirements, documentation, and effectiveness of all of these programs requires that program owners or the Safety Department hold clear responsibility for managing them. They also need an integrated management system to ensure all of the required elements are in place and utilized effectively.
In today’s workplace, only the smallest companies can do an adequate job using spreadsheets and binders for the task. Most companies choose a safety management/training management software (SMS or TMS) product, like Safesite, to reduce the administrative burden and more easily share information across the business.
Note: OSHA does not mandate or approve the use of any specific SMS or TMS. Instead, OSHA evaluates compliance on the performance observed during an audit or post-accident inspection.
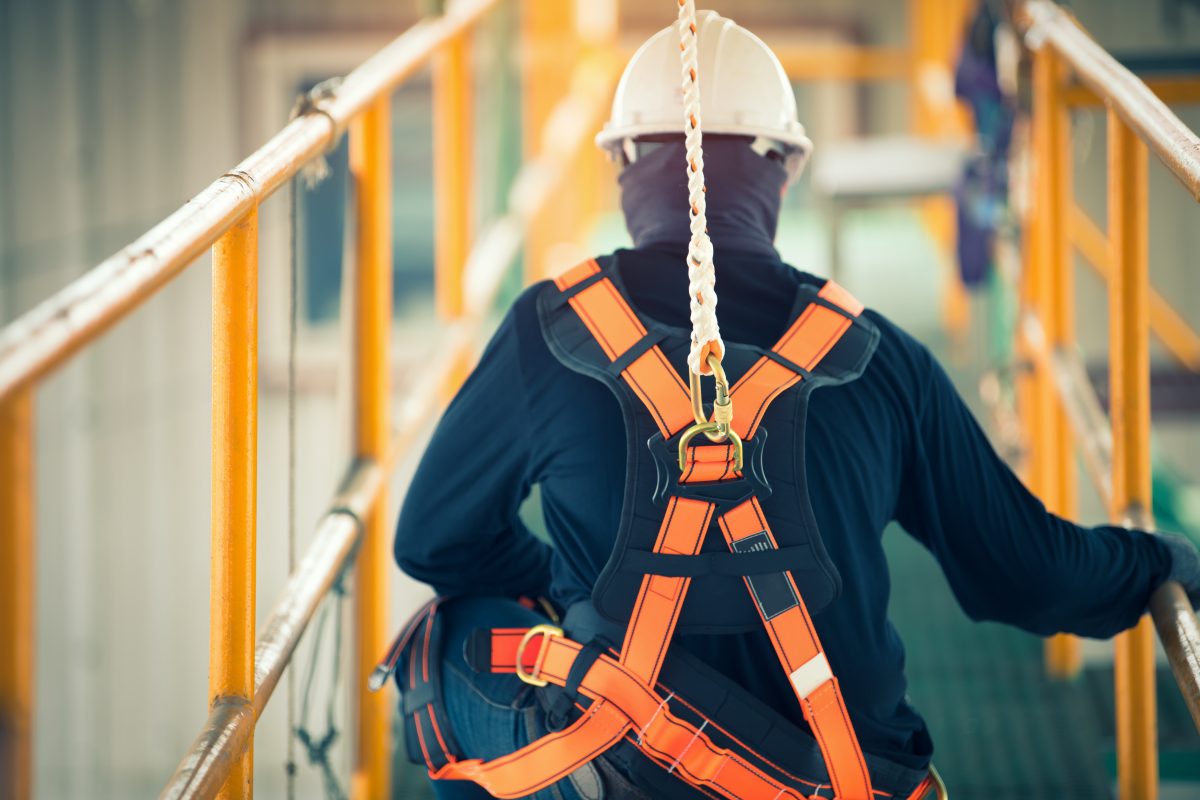
Key Elements of a Safety Management Program
What goes into a safety management program?
Every organization’s safety management program should reflect the work done and regulatory requirements. Even so, you will find that almost every safety program includes these elements in some form:
- Management Commitment to Safety
- Written Safety Programs and Procedures
- Employee Involvement
- Employee Training
- Hazard Recognition and Control
- Accident and Incident Reporting
- Incident Investigations
- Using Incident Analysis
- Communications
Management Commitment to Safety
Management commitment to safety is how members of management (Owners, Plant Managers, Supervisors, etc.) take an active posture in the control of safety and health. Their commitment includes defining and putting into practice policies and systems for recognizing and minimizing hazards to ensure a safe and healthy workplace for all employees.
In addition, management ensures that safety becomes an integral part of all company activities and objectives.
Leadership should support, encourage, and recognize workers who work safely. They should also recognize those who participate in making the company safer by taking actions like reporting hazards or proactively suggesting safer ways of accomplishing tasks.
Most written safety plans include a declaration that “management is committed to employee safety” or “safety is job #1.” However, these declarations are only words. Effective management demonstrates commitment when they:
- Set an example by making time and funds available for safety improvements
- Modify rules and procedures when a better suggestion appears
- Make themselves visible to and take an interest in employees
- Follow the same rules set for all employees
Written Safety Programs and Procedures
Low-hazard general industry businesses that do not manufacture products and have office-bound employees may require as few as five written plans and programs.
Construction companies, manufacturers, utilities, and higher-hazard industries may have 25 required written programs in their Safety Manual. You can find some OSHA sample programs on the OSHA site.
To identify the programs needed, people from all company departments with knowledge of operations and procedures should conduct an evaluation and compliance gap analysis.
The evaluation is a comprehensive safety audit. You can use it to determine what areas require compliance with safety standards and which topics don’t apply to company operations. Many standard inspection templates exist.
The OSHA Small Business Handbook contains guidance on evaluating which safety programs apply to your company.
Standard Operating Procedures (SOPs)
Standard operating procedures (SOPs) provide detailed guidance on routine and repetitive operations. These tasks may include maintenance procedures, tool set-ups, and machine operating instructions. SOPs are also useful for specifying the “who” and the “how-to” for standing procedures such as building evacuation, emergency actions for medical emergencies, fire, etc.
An SOP works when the “how-to” is static, but the personnel assigned to take action may change over time. Because SOPs are shorter and more detailed than written programs, you will find it easier to change them when necessary.
Along with the “high level” guidance program documents (i.e., Hazard Communication Program, Lockout-Tagout Program, Emergency Action plan, etc.), the safety management system also requires other more focused procedures and standard forms.
Job Hazard Analysis (JHA) forms evaluate hazards and risks to personnel. JHA forms are also tools to analyze the personal protective equipment or respiratory equipment required for the plant’s job tasks or areas. The Hazard Recognition section below discusses the JHA and Risk Matrix process in detail.
You must store all of the written procedures, forms, and documentation in an accessible location (either physically or electronically, or both). Records must be kept of revision history, so only the document’s current version is available for use.
Employee Involvement
Implementing a safety management system should happen from the “ground-up” rather than from the “manager’s office down.” A ground up approach involves employee input, which is critical to an effective, functioning safety program.
Employees from all organization levels should work together when developing written programs, creating JHA’s and JSA’s, and choosing new processes and equipment for installation.
Running Safety Teams
Many companies have an Employee Safety Committee or Safety Team. OSHA considers such involvement to be critical to a company’s safety success.
According to OSHA: “In an effective safety and health program, all workers:
- Are encouraged to participate in the program and feel comfortable providing input and reporting safety or health concerns.
- Have access to information they need to participate effectively in the program.
- Have opportunities to participate in all phases of program design and implementation.
- Do not experience retaliation when they raise safety and health concerns; report injuries, illnesses, and hazards; participate in the program; or exercise safety and health rights.”
Employees must have the time and resources necessary to participate in safety-related activities. They also need the authority to bring issues to management for resolution without fear of reprisal.
As a result, participation in safety committees should be voluntary. Acknowledge those who participate and possibly even reward them for going above and beyond their job description to make the workplace safer and healthier for everyone.
Employee Training
Part of the importance of assessing which OSHA compliance topics apply to your business is that it allows you to determine the type and quantity of training required for safer work.
Most safety regulations involve some form of awareness and understanding. However, not all of them require in-depth skills-based training or specific documentation.
First, you must determine which topics require specialized training (i.e., Confined Space Entry, Lockout-Tagout, etc.) and which ones you can roll into new hire orientation or annual awareness training (i.e., electrical safety for non-electrical workers, ergonomics, safety signs and tags, etc.).
Note: You may need to provide additional training depending on the job responsibilities of individual workers, supervisors, and managers.
Practical training and education can happen outside a formal classroom setting. Peer-to-peer training, on-the-job training, daily toolbox talks, and worksite demonstrations are effective in conveying safety concepts, ensuring understanding of hazards and their controls, and promoting good work practices.
Hazard Recognition and Control
According to OSHA, the goal of hazard control is to “…furnish…a workplace that is free from recognized hazards that are causing or likely to cause death or serious harm.”
To accomplish this, the management needs to make hazard recognition and control a key part of the safety program.
Hazard recognition starts with frequent facility or site walks designed to identify likely unsafe conditions.
These walks identify hazards like wet or uneven walking surfaces, which could lead to trips and falls, unguarded equipment, spills, or leaks.
Other aspects of hazard recognition and control include:
- Collect and review information about workplace hazards
- Investigate injuries, illnesses, incidents, and near-miss accidents to determine the underlying hazards, their causes, and safety and health program gaps
- If possible, fix hazards as you find them. If you can’t, take steps to isolate the hazard from employees and put a plan in place to remove it as soon as practicable
- Analyze the hazards of complex or non-routine operations, identify interim control measures and communicate hazards to company personnel
Hazard Control Never Ends
Hazard recognition and analysis is not a task that is ever truly complete. It’s a continuous process. As soon as you recognize and deal with one hazard, you will inevitably observe another introduce by a new substance, process, or facility modification.
That’s why you need both formal and informal hazard analysis inspections.
Your hazard control program will benefit from involving different (even outside) personnel. Why? Because plant operators get used to seeing the facility over time. Familiarity means you can miss issues that are obvious to a fresh set of eyes!
Accident and Incident Reporting
Regulations issued under OSHA require all employers with ten or more employees at any time during the previous calendar year to maintain records of occupational injuries and illnesses using the OSHA 300 Summary.
The purposes of the OSHA recordkeeping requirements are four-fold:
- Assist compliance offers in the determination of the company’s injury experience.
- Ensure you gather uniform statistical information.
- Inform employees of their employer’s injury/illness experience by posting the information.
- Assist the employer in identifying trends of occupational injuries and illnesses and determining corrective actions.
OSHA defines a recordable injury or illness as:
- Any work-related fatality
- Any work-related injury or illness that results in loss of consciousness, days away from work, restricted work, or transfer to another job.
- Any work-related injury or illness requiring medical treatment beyond first aid.
- Any work-related diagnosed case of cancer, chronic irreversible diseases, fractured or cracked bones or teeth, and punctured eardrums.
There are also particular recording criteria for work-related cases involving:
- Needlesticks and sharps injuries
- Medical removal
- Hearing loss
- Tuberculosis
Keeping the OSHA 300 Log
Each employer must keep injury and illness records for every establishment. An establishment is defined as a “single physical location where business is conducted or where services are performed.” This means each separate location such as a construction site, plant, office, shop, lab, or warehouse.
- Obtain the OSHA Log sheets from the Safety Department. (Normally, the safety department is responsible for the log).
- Record all occupational injuries and illnesses within seven calendar days of your knowledge of the occurrence (sooner if possible).
- Keep the Log in the file with your First Reports of Injury. The OSHA 300 Summary shall be completed and posted no later than February 1 of the year following the calendar year covered and shall remain in place until January 31 of the following year.
Incident Investigations
Accidents are unplanned events that result in disruption of the workflow, personal injury (or illness from exposures at work), or property damage. Since the word “accident” implies something that happens by chance, we should stop using it in occupational safety. Instead, we should substitute the word “incident,” which simply means an “event or occurrence.”
It is critical for companies to track and learn from incidents that result in injuries or serious loss. OSHA requires companies to do more than report injuries and fatalities. Companies must also understand the causes and fix unsafe equipment or process failures that may have led to the incident.
Incident investigation determines how and why the event happened. The value of incident analysis lies in thoroughly understanding all of the factors that led to the incident. This includes identifying the safeguards in place and why they did not prevent the incident.
Although there are dozens of approaches and techniques available for incident investigation, the basic methodology involves the following steps:
- Assign Responsibility for the investigation, define the scope, assemble the team.
- Fact-Finding: (i.e., visit the incident site, review statements, and photos, interview witnesses, assemble written procedures, maintenance logs, etc.)
- Develop a Narrative: (i.e., assemble a timeline of events leading up to the incident based on the results of fact-finding.)
- Causal Analysis: (i.e., using the information from steps two and three, determine the key points where alternate action could have avoided the incident. If possible, try to find the most direct or “root” cause of the occurrence.)
- Corrective Actions: Select corrective actions based on the causal factors from step 4. Avoid the “blame the worker” mindset. Practical corrective actions follow from the hierarchy of controls, with engineering solutions being the most effective. Administrative corrective actions like “re-training” and “install warning signs” are prevalent. However, they are not effective in the long-term because they depend solely on employee action. Installing guards and interlocks, substituting less toxic substances in the process, or separating workers from the hazard are the most effective ways of preventing a recurrence of a similar incident.
- Lessons Learned Communication: Although not part of the incident investigation per se, communicating the knowledge gained from the investigation and the corrective actions taken throughout the organization (and filing them for future use) is a great way to show employees you are serious about improving safety.
Using Incident Analysis
Incident analysis focuses on behavioral and system failures that result in injuries or process interruption. The effort you put into understanding “what went wrong” and fixing it prevents the recurrence of the exact same failure (assuming the corrective actions selected suffice).
However, focusing solely on preventing recurring failures precludes an understanding of 99.99% of the other actions that do not result in accidents. In other words, safety staff often spend time looking at the wrong things.
The process of incident analysis can be used proactively to look at high-hazard operations before an incident. The results can determine where the possible failure points might be and what the current workers are doing right.
Often, incident analysis reveals process steps and innovative techniques developed in the field or on the line that do not appear in the standard operating procedures or worker training.
The ability to align management guidance and expectations with how the work really gets done and cooperatively develop acceptable procedures is the hallmark of a world-class safety management system.
Communications
To establish and maintain a safety-centered workplace, all levels of the organization must have access to safety information and guidance. Access is achieved through effective communications. Safety guidelines and rules, emerging safety hazards, warnings and goals, and progress status are examples of information shared throughout the company. Traditional communication media such as posters, bulletin boards, and stand-up meetings still have a role. However, companies who use a distributed, mobile workforce need to use digital tools to spread the word about safety.
Implementing an efficient and effective way to provide regular safety updates to field employees is critical. By embracing these digital means of communications, companies have the ability to reach all employees — whether they are in a field 100 miles away or at their desk in the corporate office.
Safety software collects, analyzes, and prepares data to display on an array of media. This information used in real-time creates a safer and more productive workplace and keeps every employee up to date.
How to Begin to Implement a Safety Management System
With the key elements of a safety management system taken care of, let’s get into the second step: implementation.
As usual, implementation starts with documentation. And much of your documentation revolves around the safety manual.
Create a Safety Manual
OSHA does not specifically require a Safety Manual. Even still, most companies opt to include the OSHA-mandated written programs that apply to them (such as the Emergency Action Plan, Hazard Communication Program, Lockout-Tagout Program, and others) in a single document available for employee training and ready reference. Along with the mandatory programs, other guidance regarding responding to, investigating, and document incidents and near misses is included.
Pre-written “boilerplate” safety manuals are available online. However, the best approach is to follow the steps below and create one specifically for your business.
Creating the Safety Manual and its specific programs should be a cooperative effort between the EHS Department and all of the company stakeholders affected. All facets of the organization, including Human Resources, Risk Management (if you have one), Operations, Warehousing, Maintenance, and Administrative groups should contribute or at least review and comment on the document before you finalize and implement the Safety Manual.
After upper management finalized and approve the Safety Manual, you should implement document version control procedures to:
- Establish review timelines and procedures
- Establish “version control,” so only the most up-to-date revision is available for use
- Archive older copies and retain records per OSHA requirements
- Implement procedures for reviewing and updating sections when regulatory requirements, plant equipment or processes change
You should introduce and review the document during New Employee Orientation. Employees can then use it as a reference for subsequent safety training on the specific programs within it.
Tips for Starting Your Safety Manual
Use a reputable EHS Consulting Company, leverage occupational safety resources from your insurance underwriter, or refer to OSHA guides like the “Small Business Handbook” or OSHA’s online compliance guide for Construction to determine the minimum requirements for a Safety Manual customized for your business.
Avoid adding sections that might not pertain to your company, or being too prescriptive with training requirements and operating procedures. Once they are in writing, regulatory agencies will consider them enforceable, even if they go far beyond the “letter of the law.”
Finally, the Safety Manual is only useful if it is a living document. It must be familiar to workers and readily available to all levels of employees. It must also be accurate in addressing workplace hazards.
Hazard Assessments in the Safety Manual
Hazards and unsafe conditions can come to the attention of management in several ways. The worst way to find out about an event is when it becomes a “self-disclosing event” (a term coined by investigators at the US Department of Energy for fire, explosion, or catastrophe that can’t be ignored!). A self-disclosing event may include:
- an employee becoming ill or injured from the work
- a report or complaint about a potential plant or process-related problem
- possible failure before it happens
To find potential unsafe conditions, management must expend time and energy looking for them. However, they must also empower the workers to speak up when they think they see a problem.
Waiting for a self-disclosing event is not safety management. It is safety malpractice.
Below are some ways to formalize “walking around and looking for unsafe stuff.” Giving this process structure means it has:
- a definite purpose
- a schedule when hourly workers and managers are expected to participate
- a structure that allows for the assessment of large or complex operations in a systematic way, and so any problems found can be fixed in a timely manner
Spotting Hazards with Gemba-Walks
The Gemba walk is a Japanese technique that comes from Lean Manufacturing. It is also a useful concept for hazard recognition.
To complete a Gemba walk, a cross-functional team, including an EHS representative, management, and hourly workers, takes time out of their regular activities to visit “the actual place” (the literal meaning of Genba in Japanese) or what Japanese detectives termed “the scene of the crime.”
The team walks the whole floor or the percentage that can be slowly walked and seen in about an hour. During the walk, a broad range of safety practices and conditions are looked at, relative to the processes taking place, and employees are asked questions about their concerns. A note-taker records any safety, health, or environmental management deficiencies.
At the end of the walk, the group reflects on what they saw (both good and bad) and decides what actions should be taken to address any safety issues.
Making hazard recognition into a regularly scheduled, somewhat formal process ensures it goes ahead as planned and that the Genba team members are responsible for participating in the spirit of continuous improvement.
Spotting Hazards with Job Site Walks
Job walks in the construction industry identify safety issues that crop up during the constantly changing conditions at a construction, demolition, or renovation site.
These walks are usually the site safety representative’s duty. However, they are often more effective when construction site superintendents and other supervisors also attend.
Using a checklist (digital or paper) is a good idea. Documentation ensures that vital areas like fall protection, electrical safety, and hot work safety are assessed and provides a written record of the inspection and issues noted.
Harnessing Employee Reporting
Most companies provide a means for reporting unsafe acts and conditions so any employee can raise issues or ask questions about safety. Typically, there is an email address, phone number, or suggestion box available for this purpose.
Companies with effective safety management programs read and respond to these issues quickly and provide feedback to the reporting individual.
After identifying an unsafe process or condition, a Job Hazard/Job Safety Analysis (JHA/JSA) can help the worker better understand how to remove or reduce the hazard.
The JHA/JSA is both a hazard recognition and hazard control tool. You can use both to evaluate a process, piece of equipment, or proposed procedure. The JHA process starts by breaking down each work procedure into specific steps. It’s then decided what (if any) hazards are present and what kind of control can mitigate or eliminate the hazard.
Some form of hazard analysis includes the estimated severity of a failure during a step and the estimated probability of that happening to determine if the process is low or high risk. The process can be very simple or very complex, depending on the analysis method used.
Below is the simplest form of JHA (also sometimes called Job Safety Analysis (JSA):
The more detailed “risk matrix” approach is shown below:
This process is “unmitigated.” In other words, no engineering controls or PPE have been considered to mitigate the risk.
Ref: Lyon B. and Popov G.; Communicating and Managing Risk, The Key Result of Risk Assessment, Professional Safety Magazine, November 2017
After completing the risk matrix, determine if lowering the likelihood of an incident or the severity of an incident is possible to do using the hierarchy of controls.
The hierarchy of controls is an effective way of reducing or removing hazards using one or a combination of the following mitigation strategies:
- Elimination: Remove the hazard.
- Substitution: Replace the hazard with a less hazardous substance.
- Engineering Controls: Isolate the worker from the hazard (i.e., guarding or ventilation).
- Administrative Controls: Introduce safe work procedures or guidelines.
- PPE: Protect workers with personal protective equipment.
Note: Elimination, Substitution, and Engineering Controls are the most effective. They do not depend on any worker’s action or cooperation to control the hazard.
Safety Training and Education
Training and education are critical to establishing safe work habits and sharing knowledge. All levels of employees, from the most senior managers to new hires, require training. Training programs prepare you to:
- Recognize and fix hazards
- Know the safe way of operating equipment
- Understand what to do in an emergency like sudden illness or fire
Approximately 100 OSHA standards require the employer to train workers. Alternative standards require only “certified,” “competent,” or “qualified” workers to perform specific jobs.
OSHA requires employers to train and examine those workers and designate them competent to carry out their job tasks safely. The obligation puts a serious burden on companies to:
- Determine which standards pertain to them and identify the training required
- Source or create training programs
- Determine which employees must participate in specific safety training
- Provide the training in an effective way
- Create a Training Management System (TMS) to organize the scheduling, administration, and recordkeeping for company-wide training
- Continually evaluate training programs and update them as necessary
Safety Training Needs Assessment
To determine which safety topics to provide the employees, employers must first conduct a “Training Needs Assessment.”
The needs assessment is a survey of the Safety Manual sections requiring training for compliance purposes. It also serves as a detailed task assessment to understand what types of jobs pose risks to employees that can be mitigated by training.
Example: if a Maintenance Technician climbs ladders, uses hand tools, and performs minor electrical work, all of those tasks would require some form of training and education. The Maintenance Technician will not need Forklift driver training if they never operate a powered industrial truck.
The needs assessment should also look at the company’s OSHA 300 logs, near-miss reporting, and workers compensation injury data. The data will help them determine whether the training program adequately addresses tasks that caused injuries in the past.
Office and Industrial Ergonomics are topics that are not specifically required under federal OSHA standards. Yet, back injuries and strains and sprains are significant factors at some companies and should be addressed with a proper training program.
Training Program Organization
The purpose of the training and education program is to ensure that employees understand the safety and health hazards associated with their work.
A successful training program shall include all employees, including managers, supervisors, and administrative and engineering employees.
Key Training Program elements include:
- Qualified persons educated in both technical safety compliance requirements and adult learning techniques should design and implement the program
- A mixture of various instructional design types should be used, including classroom instruction, computer-based learning, on-the-job training, peer-to-peer and manufacturer’s technical training, etc.
- Training should be presented in the language and at the level of understanding appropriate for the individual(s) being trained. Instructional materials should also be available in the learner’s first language.
- The training program should include a means for adequately evaluating its effectiveness. The adequacy and frequency of training should be regularly reviewed.
- Job-specific training shall be offered to new hires and workers transferred to a new task before starting work. Each new employee should receive a demonstration of emergency actions, required PPE, evacuation routes, administrative and work practice controls, and any other information required to prevent injuries or occupational illnesses.
Training Program Effectiveness
Having a training program and providing safety training does not guarantee that the message has been received and understood by the classroom employees.
Effective training programs include procedures to determine how much of the information employees internalized after training ended.
Homer Lambie, former Director of Safety for Kaiser Aluminum and Chemical Industries and Safety Management expert, said, “…the value of any meeting is measured in terms of what the group attending the meeting will do differently after the meeting.”.
Apart from observable behavior change, some other methods for assessing training effectiveness include:
- Questionnaires
- Performance assessments
- Personal and group interviews
- Incident and illness records
- Incident reports and investigation
- Post-accident corrective actions that point to training deficiencies
Any low training effectiveness assessment findings are not failures of the training program. On the contrary, negative results are priceless organizational learning opportunities.
Continuous improvement of your training programs will benefit both the employees and the company’s bottom line, as improvements lead to fewer incidents and injuries.