During Safety Stand-Down week, we should take the time to think a little deeper about how we do our work, how we treat each other, and what we can do to make the job better—and safer!
Teams often talk about “safety culture” but most people don’t really know what it means. Simply put, “culture” is how a company does things—both on and off-site. Most companies think they promote a positive safety culture but does the way we really work always line up with how management thinks we do?
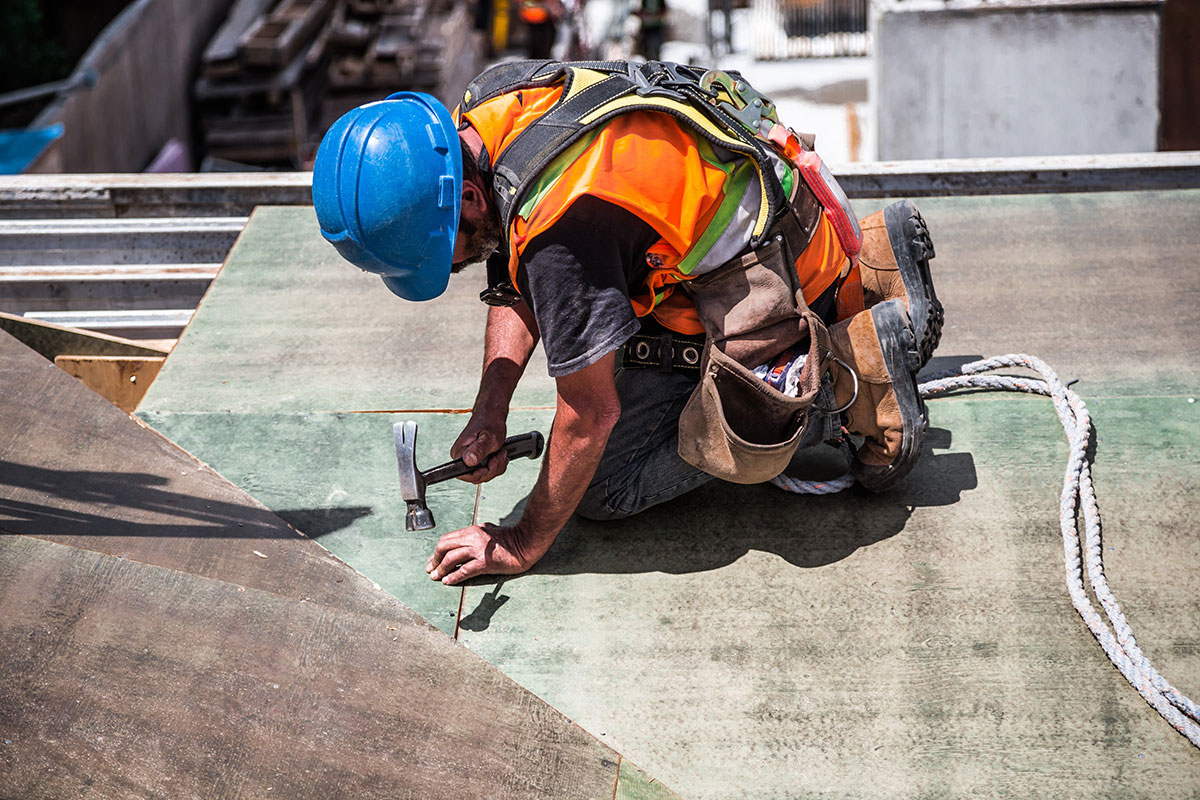
Do You Recognize these 5 Signs of a Broken Safety Culture?
A large study of over 22 companies and 1500 workers found that after most workplace accidents there were employees who were aware of the hazard beforehand, or who knew that people were bending the rules to get that job done but never spoke up. In fact, the study found five main reasons for the non-reporting:
- Get ‘Er Done: Accidents were caused by rushing and taking safety shortcuts to save time because of deadlines or production quotas.
- Incompetence: Workers who are not properly trained or have the wrong experience are given jobs and not properly supervised.
- Just this one time: Unsafe actions justified as one-off exceptions because nobody thinks they will be the one to get hurt if they break a rule.
- Too many rules: Employee resentment at unrealistic or nonsensical safety rules.
- Take one for the team: Unsafe acts justified as “for the good of the company” or thinking that if you report a co-worker’s unsafe actions it betrays group trust.
Knowing that not speaking up causes accidents, let’s look at solutions to the five items above.
- Get ‘Er Done: It’s easy to say “there’s nothing more important than your safety” and many supervisors and managers do—then they send you up on a roof with no fall protection. Use your morning meeting or safety share to talk about the times when it looked like safety wasn’t the number one priority. Send the message that it’s your number one priority because you need to stay healthy for your family.
- Incompetence: If you see someone in over his (or her) head on a job, offer to show them the ropes and tell the supervisor that this person needs more training to do the job safely and correctly.
- Just this one time: Quality work takes time and so does working safely. If you come up with a better, quicker, safer way, let the supervisor or safety lead know. They like good news and don’t hear enough of it!
- Too many rules: Same with new or outdated rules. Don’t ignore them because you think they’re stupid. Instead, have a talk with the safety rep and you will learn one of two things: A) The rule is stupid and we should change it; B) There is a good reason for the new rule and now you know what it is. It’s a win-win.
- Take one for the team: Injuries cause schedule problems, make it harder for the company to get hired for projects, and cost money for medical treatment and insurance. The best thing for the company is to have quality workers like you, who work safely, speak up when they see something unsafe, and ask questions when they’re not sure of the best way to do something.
Taking this a step further, we encourage you to share this information in your safety meetings this week (and beyond). If you’re already using Safesite, head to “Conduct Meeting” and use our template. And if you’re new, download the app in the iTunes or Google Play store and follow the guide in our help center to conduct a meeting.
Stay safe out there!