A successful safety culture isn’t compartmentalized and separate from other areas of the company. It permeates all aspects of the company.
“Safety cultures endure when they are part of an overall successful organizational culture.” – David Paoletta, MS, CSP
It should be more of a concern, then, when safety culture is seen as one arm of the safety program instead of its head. You can’t put safety first if your culture is reduced to tasks, meetings, or gift cards.
In this article, we examine the core attributes of world-class safety cultures to help you take a fresh approach toward establishing a safety program that gets results.
Want to download this article and read it later? Get the PDF straight to your device.
What is Safety Culture?
Safety culture is the set of shared attitudes, beliefs, and practices demonstrated by workers at all levels of the company.
A positive safety culture connects everyone in the company around a common goal to measurably reduce near misses and incidents. It goes beyond following safety procedures and rules. Great cultures elicit safety buy-in from employees.
Behavioral psychologist and expert in behavior-based safety E. Scott Geller defines a total safety culture (TSC) as one where “everyone feels responsible for safety and pursues it on a daily basis.”
Anne Richter and Christian Koch have also explained safety culture in terms of shared experiences. They define it as having “shared and learned meanings, experiences, and interpretations of work and safety expressed partially symbolically, which guide people’s actions toward risk, accidents, and prevention.”
In a strong safety culture, everyone, from management on down, buys into what needs to be done to keep everyone safe and take the steps to get it done. Common attributes include:
- Shared values
- Contribution and engagement from all levels
- Transparency
- Continual education
- Proactive rather than reactive solutions
The safety committee is an excellent way to make top-down and tradesmen involvement official — but it doesn’t have to end there.
“Establishing and maintaining a positive safety culture takes work, investment and time, it doesn’t just happen,” says Paoletta. “It takes involving the entire organization and listening to and valuing each individual’s contribution; [that’s when] safety becomes personal and cultural change happens.”
Safety Culture as an Investment
Safety should be a pillar of a company’s values rather than an afterthought. New business owners should invest the same time, energy, and money into safety as they do in finding the right location, hiring the best workers, and gathering the necessary assets. Already established companies should reevaluate its current safety and take the required steps, no matter how expensive or arduous, to make sure safety is a top priority if it isn’t already.
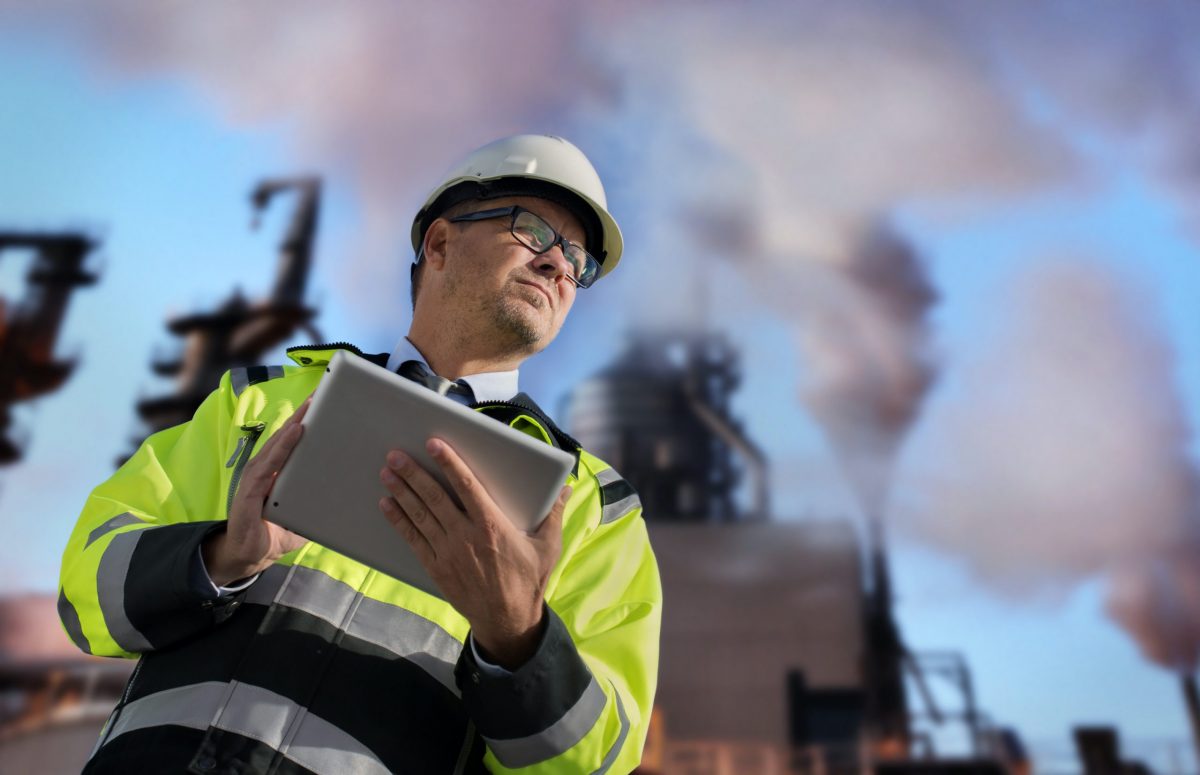
“Safety culture not only drives health and safety but it drives the organization as a whole,” explains John White, CSP. “An organization that values safety as paramount bears fruit in all other areas.”
Ensures Your Longevity
A robust safety culture not only drives health and safety decisions within the company but should also permeate all other areas of the company. An organization that places a high value on safety will see fruit in all other areas.
In 1987, Alcoa’s CEO Paul O’Niell spoke to shareholders, focusing on safety rather than other company initiatives to improve dismal profit numbers. His continued focus on safety rewarded the company and its shareholders handsomely. Within one year of his inaugural speech, Alcoa’s profits hit a record high and when he retired 13 years later, market capitalization was five times higher than when he started.
Accidents, and the injuries that result from them, cost money. From workman’s comp payouts to revenue lost from workers not being able to do their job, the price of accidents in the workplace can be steep. The fewer accidents you have, the more money you add to your bottom line.
Builds Employee Morale
When a company is built around safety, its employees notice. “A world-class safety culture improves employee morale,” says White. “When an employee feels valued and truly cared about, his or her outlook towards the organization and organizational goals is different.”
In 2017, the Queens School of Business and Gallup Organization found that disengaged workers with low morale led to 49 percent more accidents and 60 percent more errors and defects. A strong emphasis on safety engages employees and builds morale because the employees know they are cared for, listened to, and valued.
Companies with a robust record of safety (and less accidents and injuries) are more desirable and can attract the best talent in that industry.
Improves Consumer Confidence
And it’s not just employees and shareholders of the company that care about its safety. Consumers want to know the products they’re buying are safe and the company that they do business with is safe as well. One CEO realized this fact and started publicly publishing leading and lagging indicator metrics on the company’s website. Customers and competitors alike saw these numbers, but rather than hurting the company, it gave them more legitimacy in the marketplace and increased sales.
12 Core Attributes of a World-Class Safety Culture
Whether you’re building a safety culture from the ground up along with your company, or adding a new emphasis on safety to an already established business, the ingredients for success are the same.
Engaged Management
A strong safety culture starts at the top with the management team. If the management team makes safety a priority and leads by example, employees are more likely to follow suit. Here are some ways that management can set the tone for safety:
Involve all levels of management: From the CEO to line supervisors, anyone in a management or leadership role should be educated and passionate about safety and specifically their company’s safety culture. Management should walk alongside line supervisors, teaching them how to engage with employees and lead them successfully. Any management role that doesn’t spend time on the floor or out on the jobs isn’t going to get the full picture of safety.
Continually remind all employees about safety: You can’t talk too much about safety. Start each employee meeting with safety reminders and offer frequent opportunities for employees to refresh and retrain on safety. And don’t just focus on what to do or what not to do; reinforce why safety is important. You have to change employee negative employee attitudes on safety, including the belief that fast work is better than safe work and a lack of incidents makes them invincible.
Support safety supervisors and professionals: Every member of the management team should defend and support any safety employees in the company. If employees don’t see management supporting safety supervisors, they won’t take safety seriously either.
Active Safety Committee
Safety training and discussions should not become just another thing that an employee has to check off their to-do list. The safety committee should accurately represent the full array of your workforce roles, primary languages, and employee types. Your safety committee should meet regularly and offer value-added activities to employees so that the employees will want to engage. Other components of a productive safety committee include:
Variety of viewpoints: Make sure your safety committee is made up of employees from every area of your company. You’ll want to have representatives from all levels, from management down to line workers. While it would be ideal if everyone on the committee was passionate about safety, you need to have at least one or two “cheerleaders” who can keep the momentum going.
Clear purpose and organization: Follow the standard procedures for committees and meetings, creating a mission, bylaws, procedures, and goals. Set up meetings at the same time each month and follow the same basic agenda for each meeting. Having these outlined will help your committee focus on safety and not get lost in the details of running a committee. Being highly organized does not equal boring, however; make the meetings interactive and interesting with outside speakers, opportunities for conversation, and hands-on activities.
Follow through and accountability: All that talk is worth nothing if you don’t follow through with action. End each meeting with actionable items and someone assigned to fulfill those action items. Everyone on the committee, not just the chair, should be committed to keep everyone on track and accountable.
Apply Behavior-Based Safety
Depending on which stats you look at, unsafe behaviors cause anywhere from 80 percent to 98 percent of all workplace accidents. By adopting a behavior-based safety culture, companies can reduce workplace accidents. Behavior-based safety is a comprehensive look at safety and focuses on the behaviors of employees. It looks closely at accidents caused by unsafe behaviors and develops ways to change those behaviors and prevent injuries.
Behavior-based safety programs designate observers, who are employees trained to conduct on-site safety reviews. These observers watch every employee, making a list of behaviors needed to complete the job and a list of unsafe behaviors they observe. This checklist is then used by supervisors to check that workers under their watch are performing their jobs correctly and safely.
Include a system that monitors the quality of safety conversations being held and how all employees act in regards to safety. Rather than just reporting unsafe conditions, make note of what behaviors could change to improve those unsafe conditions.
The process of creating a behavior checklist shouldn’t be a one time deal; set up a schedule to revamp the checklist every few weeks or months.
Human and Organizational Performance
Sometimes called “New View” or Safety-II, Human and Organizational Performance (HOP) strives to use social sciences to create better systems. Managers who adhere to the HOP philosophy work to change not just their behaviors as a leader, but their beliefs toward their employees and leadership.
Essentially, HOP calls leadership to put themselves in their employees’ shoes. If you’ve never operated heavy equipment, you won’t have the necessary knowhow to create safety rules about operating heavy equipment. HOP pushes management to become educated on every job in their company and use that education to shape a safety plan.
Discovering these details is done through Operational Learning, where you learn directly from those doing the work. Another aspect of HOP is Learning Teams, which brings together those doing the work and those creating the safety systems together onto one team to put together a proactive or reactive safety plan. A HOP-inspired safety plan looks at systems as a whole rather than just individual workers or machines.
These new ways to look at safety have filtered into safety management systems, which are programs companies use to promote safety and reduce risk. The systems approach of HOP is seen throughout the ANSI Z10 standard (OSH Management) and ISO 45001 standard, as well as Occupational Safety and Health Administration safety management recommendations.
Safety Training
A key part of your safety culture is frequent training opportunities. Make it easy for employees to attend training sessions by offering after-work or weekend classes, or even providing paid time off for training. Online safety training sessions can also be helpful for making sure employees can get the training done.
The National Safety Council has a ton of resources available for companies including safety training modules, training packages, and on-site and online classes. Track employee completion of any training, classes, and workshops to ensure that all employees are informed of safe work practices.
Safety training should also include teaching supervisors and management on how to lead behavior-based safety conversations with employees. Leaders should be able to effectively convey how important safe behaviors are to the overall safety of the company. They should also practice what they preach.
Leading Indicators
Instead of just relying on incidents as the only metric for safety, companies should use leading indicators to measure success and/or failure While both lagging and leading indicators can provide feedback on your safety program, leading indicators look forward and allow a company to be proactive. Leading indicators help gauge the health of the organization’s safety culture and alert management to unsafe trends. Implement leading indicators in your safety reporting to get a comprehensive look at how your company is performing when it comes to safety.
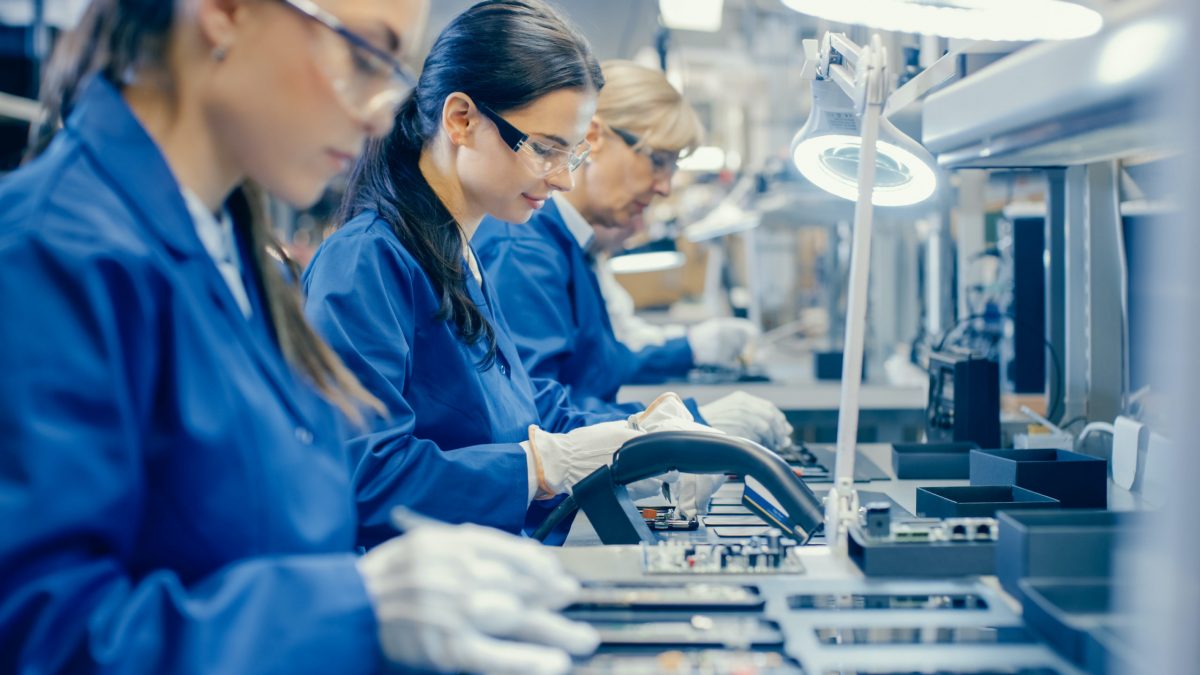
Some leading indicators that are most helpful include:
Near-miss reporting: While often used as a lagging indicator, near-miss reporting gives you the ability to investigate and correct unsafe conditions and trends before they happen again. By studying near-miss incidents, you can see what went wrong, what prevented it from escalating to a full incident, and what you can do to prevent it in the future.
It also helps to know the difference between a near-miss, an actual incident, and an unsafe condition. A near miss is a circumstance when no one actually gets hurt, but the potential for injury was imminent. An actual accident occurs when a worker is actually injured because of safety issues. Unsafe conditions lead to near misses and actual accidents; employers should pay close attention to them and take proactive steps to keep them from occurring in the future.
Corrective action completion: Take action quickly once an unsafe condition or incident is reported. Investigate and correct as soon as possible so that employees, shareholders, and the public see you take safety culture seriously.
Safety Recognition Programs
Instead of rewarding all environment, health, and safety activities, only recognize with incentives and rewards those employees that go above and beyond. Encourage and support all employees performing these basic EHS safety activities, but they should know these are expected as part of their job. You don’t have to and shouldn’t reward everyone, but you should show appreciation for everyone doing their part.
The employee safety committee should play a key role in safety recognition program ideas, implementation, and operation. Because they are employees themselves, they’ll have a better pulse on what types of recognition is most motivating to employees.
No matter what your recognition program looks like, never reward employees for covering up incidents. A safety recognition program should never discourage incident reporting but rather be motivating enough to encourage more incident reporting.
Any safety recognition program should be sustainable. Many safety recognition programs have started strong but petered out, becoming routine, ineffective, and useless. Just as you evaluate safety training programs, assess your safety recognition programs to improve and keep the programs motivating.
Continuous Improvement
Never stop learning, growing, and improving. Each company should perform frequent audits to identify new safety hazards. Constructive cultures constantly evolve and change as needed, improving processes and behaviors based on the findings of each new safety audits. Safety experts agree that complacency kills; don’t rest easy on low incident rates and few accidents. Companies should also strive to improve their safety cultures every single day.
Provide frequent training sessions, continuing education classes, and other ways for employees to keep growing and learning. Frequently update your company’s behavior checklists and adapt to the growing needs of your company and its employees.
Employees Who Are Comfortable Speaking Up
Your safety culture should make employees comfortable speaking up when they see safety hazards or unsafe behaviors. Employees shouldn’t fear retaliation from management or other employees for saying something when they see something.
Consider implementing a whistleblowing system or another anonymous way for employees to report unsafe behavior. Work to create a system of positive reinforcement rather than discipline. The fear of discipline for messing up or reporting a mess up can actually be more detrimental, as that fear could lead to hiding issues rather than bringing them out in the open. Positive reinforcement also builds trust, increases morale, and promotes employee engagement.
Dedicated Resources
It takes money to make money and it takes resources to make your safety plan work. Be sure that your company’s budget includes money to cover safety programs. These funds cover everything from safety committee meetings to safety training to rewards and incentives for employees.
Consider Contractors, Customers, and Competition
A company’s safety culture should extend beyond the walls of the factory and worksite. Involve your contractors and customers in discussions about safety, gauging what safety practices would make them more likely to do business with you.
You should also be willing to share safety best practices with competitors because a safer industry is good for everyone. The oil and gas industry saw this play out. Those companies with a flourishing record of safety were successful, while those who were unable or unwilling to develop their culture found themselves failing in the industry.
The National Academies of Sciences, Engineering, and Medicine convened a committee to study the cultures of the offshore oil and gas industry. In 2016, it published a report based on the findings. Several of the recommendations that came out of the report spoke to the importance of sharing of experiences, information, research, tools, and more related to creating a safety culture. The report encouraged more sharing of information to make the industry as a whole safer.
Open Communication
Open communication is key to all of the ingredients of a great safety culture. If the lines of communication — whether in-person, in writing, or online — aren’t open, employees won’t have clear direction and management doesn’t receive the feedback it needs to make the culture successful.
Common Mistakes with Safety Cultures
The old saying goes that “Rome wasn’t built in a year” and the same applies when building a reputation for safety at your company. Creating an effective safety culture is a marathon, not a sprint; it takes patience, dedication, and endurance. It may take a year or more to see measurable results, but the effort is worth it.
Not Being Flexible
To be most effective, your company should follow a well thought out plan with measurable goals and milestones to mark your progress in safety. Unfortunately, no matter how thorough your plan, you’ll run into issues along the way and will have to be flexible. You may run into roadblocks and detours and the ability to adapt on the fly will be integral to your plan’s success. “A strategic roadmap will help you and management stay on course while fighting the day-to-day fires,” says White.
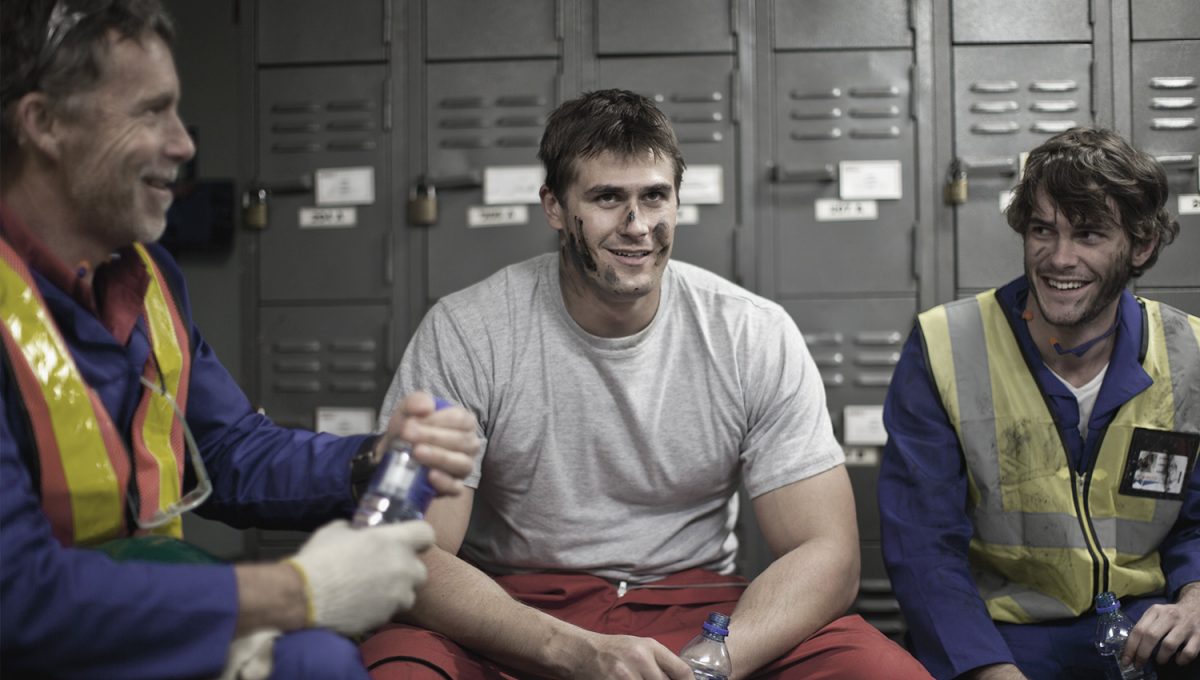
You must create an effective roadmap with milestones for how the organization plans to achieve world-class excellence. However, you must also be flexible and willing to deal with issues tactically as they come up. Make your goals highly visible to everyone in the company and celebrate wins big and small.
Not Being Transparent
Trust is a major component of any relationship, and especially between employer and management. If management isn’t honest and upfront about the process of building a safety culture, employees will be less likely to buy in. Be open about how long the process will take, what all will be involved, and how you plan to deal with unexpected issues.
Not Focusing on Behaviors
Your company’s culture can’t rely entirely on compliance but must also focus on behaviors. As mentioned above, behavior-based safety makes your company proactive rather than reactive. When a company uses only compliance for safety, it ignores the ways that worker behavior plays a role in causing and preventing accidents.
“Behavior-based safety is proactive and addresses behaviors which lead to smarter and safer work practices,” observes White. “The behaviors in turn help make regulatory compliance sustainable and not just the safety professional’s battle. Compliance alone will not create a world-class safety culture.”
Not Paying Attention to Systems
As important as it is to look at behaviors, making behaviors the sole focus is a common mistake of behavior-based safety. As mentioned above, companies integrating behavior-based philosophies can’t look at just one worker or a certain piece of equipment. It must look at how each employee and all pieces of machinery work together as a system.
Not Involving More Than One Personality
Having a face for your safety culture is important because it gives employees a rallying point and provides a personal touch. These leaders model safe behavior, connect with all employees and create a climate of teamwork, transparency, and respect. They aren’t always a member of management but exude the confidence to lead and act as a liaison between all levels.
However, companies run into trouble when only one person or face leads the cause for safety. If that company’s safety leader retires or moves onto another company, the culture can suffer. Without that one personality cheering them on, workers can lose a sense of the shared responsibility and buy-in that made it successful.
Measuring the Success of Your Safety Culture
One of the hallmarks of a successful safety culture is measurable goals and attainable milestones. But how do you measure success when you have a mix of subjective and objective factors? The safety committee is key to measuring goals and evaluating success, but other factors can also indicate how well a company is doing.
Safety Surveys
Regularly survey employees to gauge their views on the actual culture of the company. The type of survey (paper, online, etc.) you use doesn’t matter as much as the data you collect. It’s helpful if your survey has a mix of different types of questions. Multiple-choice, rating, Likert scale and short answer questions are easy to answer and create helpful numerical data, while open-ended or long answer questions give more specific insight into employee behaviors and thoughts.
In 2005, Thomas Krause created a survey tool that measures the level of safety culture perception among employees. This tool, called the “Organizational Culture Diagnostic Instrument”, takes a company’s survey data and compares it to a database of prior data from other organizations. The OCDI draws on organizational performance dimensions that have been shown to correspond to safety culture effectiveness. These four dimensions include:
- Procedural justice (fair decision making, lack of bias, correctable)
- Leader-member exchange (supervisor/worker relationships)
- Management credibility (honesty, consistency, communication and concern)
- Perceived organizational support (concern for needs and interests of employees)
The National Safety Council has numerous safety survey resources for creating your own surveys or using premade ones, as well as interpreting the results.
Focus Groups
Another way to measure how a culture is working is through employee and management focus groups. By involving all employees, every employee can feel like they really are making a difference and that their opinions and views matter. Focus groups are an easy and cost-effective way to measure success.
Follow Through
No matter how you measure success, if the tools you use find gaps and issues, you need to address them quickly and thoroughly. Paoletta encourages companies to take action or risk losing credibility with the workforce.
“When these tools yield actionable data on areas that can be improved, the company should embrace the learning opportunity and set up a cross-functional, employee-centered team to discuss the current situation and suggest positive changes that will address the gaps that were shown from the survey,” he says. “Management should work with the team and support changes to show organizational support for safety improvements. Over time, this cooperative approach to assessing current practices and being open to changing and improving them becomes part of a positive safety culture that is sustainable over the long term, regardless of who the safety manager or management leader is.”
The Bottom Line
Safety culture goes beyond promoting safety first to your employees. A world-class safety culture requires adopting a complete safety infrastructure for your business.
To improve your company culture, research behavior-based safety, HOP philosophies, and safety management systems and standards. Do an audit of your company’s current safety systems, looking for what needs to be fixed and thinking proactively about what could go wrong. From there, you can create a plan that’s specifically tailored to your company, assign roles and responsibilities, and work toward achieving your safety goals.
Building a safety culture from scratch or modifying a current culture to be more successful takes time, dedication, and patience. Everyone in the company — from the highest-paid member of management to every employee working on the floor — must buy into what you’re selling. All employees must be well-trained and the lines of communication open.