If you aren’t regularly assessing your safety program, then you’re only able to guess its effectiveness. And guessing? Guesses don’t make it easier to prevent injuries, present progress to company leaders, or ask for money to strategically improve safety.
Using KPIs based on leading indicators is a big part of the assessment process. But what do you do if you’re struggling to meet your KPIs and you don’t know why? You can run a gap analysis tool.
Gap analysis requires you to ask some pretty important questions: Where are you, really? Where do you want to go? How do you get there?
Every safety program can benefit from a periodic gap analysis assessment. Keep reading to learn more about the benefits of a safety program gap analysis tool and for a step-by-step guide to running a gap analysis for your program.
Ready to run? Download the free Safesite gap analysis checklist and gap analysis template.
What is Gap Analysis in Health & Safety?
A safety gap analysis is a form of a safety audit that measures your current safety procedures against your safety requirements. In other words, it systematically parses your safety program to:
- Look for gaps in your safety program’s coverage
- Identify strengths in your program
- Find opportunities for improvement
- Determine whether your program will be effective next month, next quarter, or next year
A gap analysis offers more than a clear picture of your safety program. It also indicates what you need to do next to meet your requirements. You can then use these to create a step-by-step targeted safety improvement campaign.
What Are the Benefits of Gap Analysis Tools for Safety?
Gap analysis tools are used throughout organizations to identify and shore up gaps or weaknesses. But why use such a broad tool for your safety program?
Overall, running a gap analysis on your safety program is part of a proactive approach to safety. You’re identifying unknown weaknesses now so those weaknesses don’t translate into losses later.
Beyond the overarching benefit, gap analysis tools reveal their value in a myriad of ways that will save lives, reduce costs, and make everyone from workers to the C-suite happy.
A gap analysis for your safety program can:
- Ensure compliance: Very often, safety program weaknesses can lead to OSHA violations and citations in addition to losses. Running a gap analysis tool can help you pick up areas of high risk, so you can use leading indicators to track and improve them.
- Determine suitability: How well are the current components of your safety program working? Do you need new tools? Could you change your current tools to better support safety? A gap analysis can indicate the suitability of a safety solution or tool, leading to a better fit right away.
- Help meet KPIs & objectives: Every safety program aims to meet or exceed set goals. However, there may be hidden gaps holding you back month after month. A gap analysis will identify those weaknesses and missing parts, so you can better meet your objectives.
- Free up new and existing resources: A gap analysis is a great tool for spotting inefficiencies and reforming them. In the end, you’re usually able to free up resources of some type, whether that’s time, money, or tools.
Across the organization, a safety gap analysis can:
- Improve company and site safety
- Send productivity skyward
- Contribute to a world-class safety culture
- Boost morale and confidence at work
When Is it Time for a Safety Gap Analysis?
A safety gap analysis is a type of audit, which means you won’t run them daily, weekly, or monthly. Instead, you use a gap analysis as a tool of problem-solving.
There are three times where you will see the most benefit from running a gap analysis tool:
- When you struggle to consistently meet safety performance goals
- If federal or state OSHA compliance requirements change in a meaningful way
- In the event of a major incident, such as a reportable injury or death (or even in a very harrowing near-miss)
You don’t always need a safety gap analysis to tell you what the problem is. If your root cause is easily identifiable, then a gap analysis could still benefit you but it may not be what you need, particularly short-term.
Tip: A gap analysis can take days, weeks, or months depending on the scope of your safety program and the size of your organization. However long it takes, you need multiple voices in the room, including key stakeholders, workers, and management.
If you’re unsure whether a gap analysis is a good idea right now, ask yourself: “Is this issue worth the valuable time of everyone involved?” If yes, then run that gap analysis.
How to Do a Gap Analysis Assessment
So how do you get started with gap analysis? To find the most success, you’ll run it in two phases.
Set-Up Gap Analysis Methodology
First, you’ll set up your gap analysis methodology. In short, this means deciding:
- What area will you focus on?
- What information do you need?
- Who will get that information
- Where will they find the information?
- How will they handle the information?
- Who will evaluate and analyze it?
- How will you share the results?
- Who will share the results?
It’s a good idea to fill in a gap analysis methodology template every time you run a gap analysis. Doing so will help you keep the analysis focused on one issue, making it easier to tease out problems and identify meaningful solutions without getting sidetracked
Run the Gap Analysis Template
Once you have the who, what, and how, there are three primary phases:
- Determining your requirements (e.g., compliance, contractual, etc.)
- Identifying your current program’s achievements
- Searching for a gap between the two
Overall, your gap analysis will follow a checklist similar to this one:
- Establish pre-determined requirements (regulatory compliance measures, goals, future requirements, etc.).
- Review existing safety policies and procedures.
- For more in-depth information, go beyond SOPs. Look at KPIs, risk assessments, and safety observation data for more granular, accurate detail.
- Run through a site safety inspection.
- Get quantitative and qualitative feedback using JHAs and interviews.
- Interview employees and key stakeholders to go beyond a comparison of the SOP to what’s happening on the ground. Always remember the Hawthorne Effect.
- Get quantitative and qualitative feedback using JHAs and interviews.
- Identify the gaps between your requirements and your existing plan.
- Is the gap small? Will it require operational changes and change management?
- Identify all issues, big and small, and identify what you can address quickly.
- Use gap analysis techniques and templates to make sense of your data.
- Create and share a report.
- Write and share your findings with key stakeholders, including the size and risk level of the gap(s).
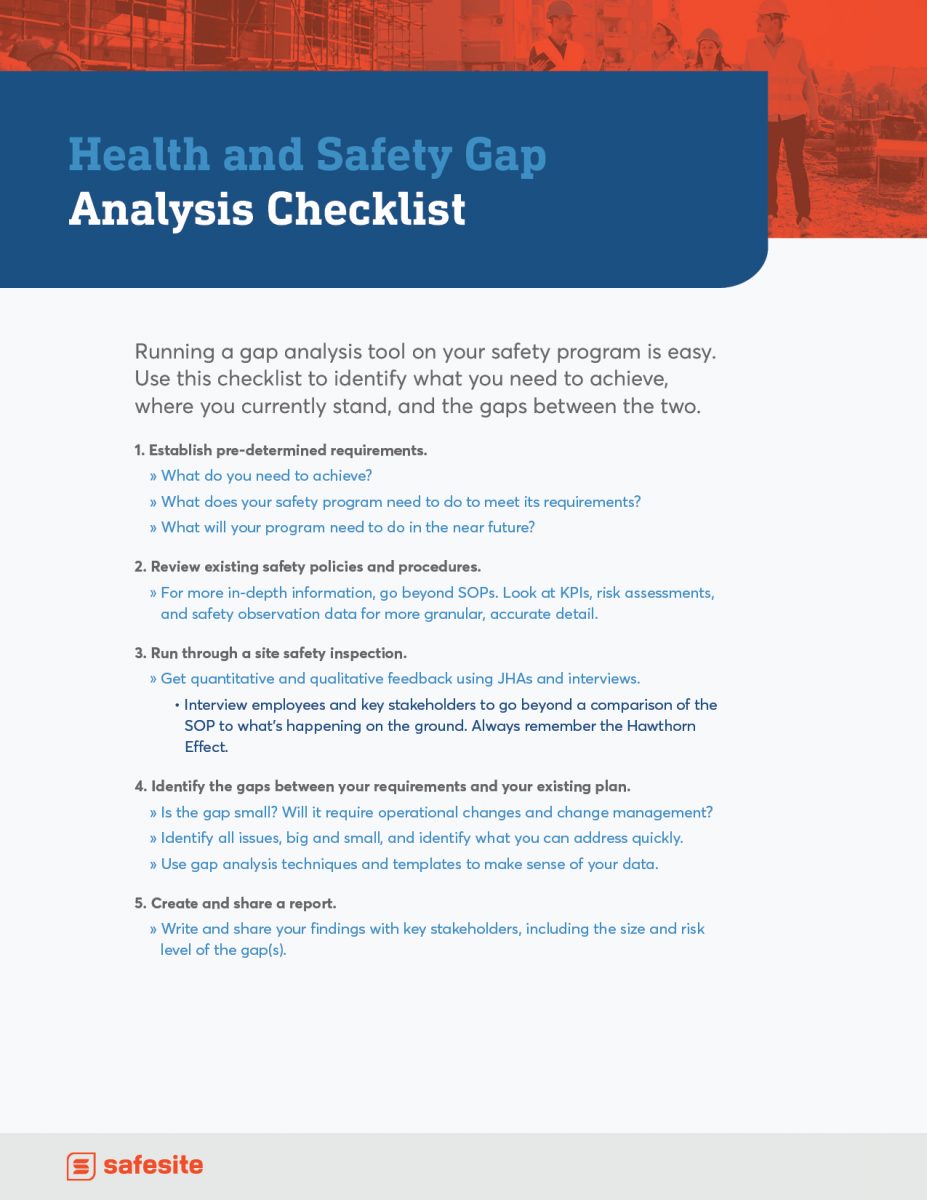
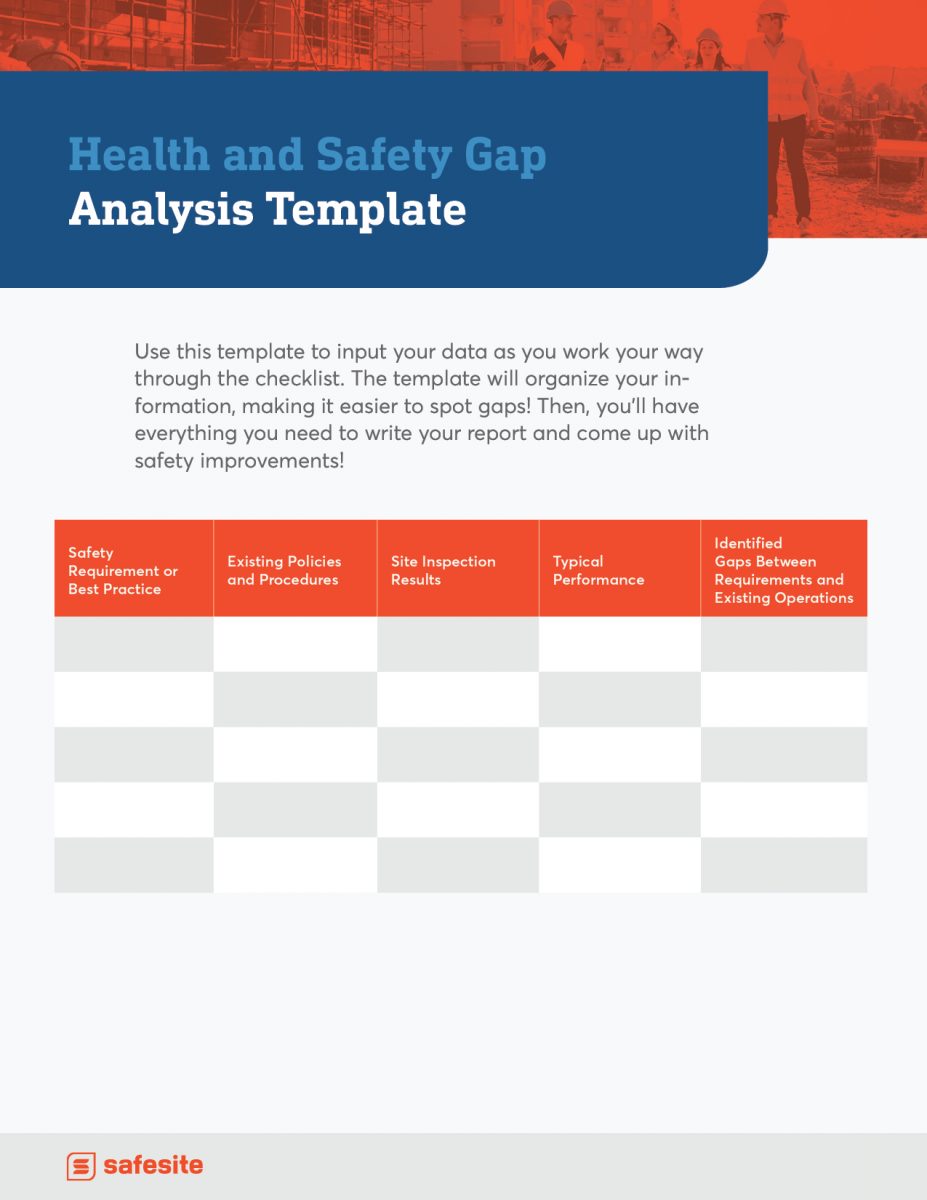
Wrap Up with Recommendations
The gap analysis tool is the first step for proactive safety improvement. You then need to leverage those insights into improvements. In other words, it’s time to close the gap.
A gap analysis report outlines the findings from the process and identifies corrective actions or process changes that can help you build a stronger safety program. Depending on your results, you might find you need to:
- Improve staff training and re-training
- Upgrading equipment
- Write or rewrite SOPs
To make the most impact, these actions should be both corrective and specific, which is why it’s so important to set those limits in your methodology before running a gap analysis.
Identify Gaps and Strengthen Your Safety Program
Are you struggling to reach goals? Wondering why you got an OSHA citation when your existing policy should have prevented it? Maybe you have a few big changes coming up and you’re not sure you’re ready.
A gap analysis tool provides a system for identifying your current state, your ideal state, and the distance between them. As an added bonus, they can help you achieve compliance, meet your safety goals, and improve both morale and safety simultaneously.
When it comes to process improvements, you don’t need to rely on guesswork. There are many easy-to-use tools available to you. Ready to learn more about running a data-driven safety program? Learn more in The Ultimate Guide to Safety Reporting & KPIs.